
Prensa de pastillas Grand vs. Standard: Guía del comprador para 2025
¿Cómo una máquina tamizadora de tabletas perfecciona cada píldora?
Introducción
In the meticulous world of pharmaceutical manufacturing, every stage is critical. From precise formulation to the final packaging, the goal is unwavering: to deliver a safe, effective, and perfect product to the patient. We often marvel at the high-speed prensa de tabletas machines that can produce hundreds of thousands of pills per hour. But what happens in the crucial moments after a tablet is compressed?
It’s here that an unsung hero takes the stage: the tablet sieving machine. This sophisticated piece of equipment is the master of finishing, transforming freshly pressed tablets from a state of raw production into the polished, flawless pills we see in a medicine bottle. It’s the critical link that ensures quality, and in this deep dive, we’ll explore how it works and why it’s an indispensable partner to any serious pill press máquina.
What Exactly is an Uphill Tablet Sieving Machine?
At first glance, it may appear to be a futuristic spiral slide. However, an Uphill Tablet Sieving Machine, such as the state-of-the-art Grand SZS750 Uphill Tablet Deduster, is a multi-functional powerhouse. Its primary purpose is to perform three essential actions simultaneously: dusting, polishing, and elevating.
Imagine a Grand prensa de tabletas finishing its cycle. The newly formed tablets, while perfectly shaped, are often coated in a fine layer of excess powder and may have slightly rough edges, known as "burrs." If left untreated, this powder can cause issues in packaging, affect dosage accuracy, and create a poor user experience.
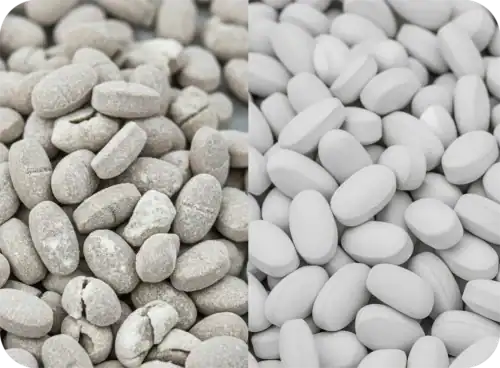
This is where the pill sieving machine comes in. It takes these tablets and gently guides them through a process that removes every last speck of unwanted dust, smooths their surfaces, and lifts them to the next stage of production, like a metal detector or packaging line. It’s a vital quality control step that is essential in the pharmaceutical, food, chemical, and electronics industries.
The Science of Sieving: How Does a Vibro Screener Work?
The magic of the uphill vibro screener lies in its clever use of physics. Unlike a simple downward chute, the uphill design provides a significantly longer and more effective path for cleaning and polishing. The Grand SZS750, for example, features an impressive dusting distance of 7.5 meters (7500 mm).
Here’s the process:
- Tablets are fed into the inlet at the base of the machine.
- A powerful but precisely controlled drive unit, or
The vibrator creates a gentle vibration. - This vibration causes the tablets to "climb" a multi-layered, spiral.
Sieve net (screen). As they travel, they are constantly tumbling and turning over. - This constant, automatic tumbling polishes the tablets on all sides, smoothing burrs and creating a perfect finish without causing any damage.
- Simultaneously, the fine perforations in the sieve screen allow the loose powder to fall away. This dust is captured in the base and can be efficiently removed by an integrated vacuum cleaner, ensuring a clean process.
By the time the tablets reach the outlet at the top of the spiral, they are clean, polished, elevated, and ready for the next step, all accomplished in one seamless, automated motion.
The Perfect Partnership: Integrating a Grand Vibrating Sieve with a Grand Tablet Press
For maximum efficiency and quality, modern manufacturing relies on creating continuous, automated production lines. This is where the synergy between a grandioso máquina prensadora de pastillas and a Grand pill sieving machine truly shines. You can create a fully integrated Grand Pharmaceutical Production Line that operates with minimal manual intervention.
The workflow is beautifully simple. The tablet outlet chute of the Grand prensa de tabletas is positioned to feed directly into the inlet of the SZS750 vibro screener. As tablets are produced, they immediately begin their journey of refinement. This seamless integration eliminates production bottlenecks and ensures that every tablet undergoes the same consistent quality control process.
With a conveyance capacity of approximately 3,000,000 tablets per hour (for Ø5mm round tablets), the Grand SZS750 is engineered to easily keep pace with the highest-output rotary tablet presses on the market. This ensures your production line is never waiting on the finishing step. Furthermore, the system is designed to connect not just with a prensa de tabletas, but also with downstream equipment like metal detectors and upstream vacuum cleaners, creating a fully contained, automated, and highly efficient manufacturing ecosystem.
Key Features of the Grand SZS750: A Closer Look
While the principle is elegant, the specific design features are what make a sieving machine like the Grand SZS750 a world-class piece of equipment.
Unmatched Dusting and Polishing Performance
The core function of this sieve machine is to produce perfectly clean tablets, and it excels thanks to its design. The exceptionally long dusting path of 7500 mm ensures that tablets have maximum time and surface contact to shed any residual powder. The automatic, multi-sided tablet polishing results in a high-quality, professional finish while being gentle enough to ensure the tablet itself is never damaged or chipped.
Precision Control and Total Visibility
No two production runs are identical. The Grand SZS750 features an easily adjustable production speed via an intuitive rotary knob on the control panel. This allows operators to perfectly synchronize the
sieving machine's speed with the output of any prensa de tabletas, accommodating different tablet sizes, shapes, and production requirements. Adding to this control is a large, transparent observation window on the body. This makes the entire production procedure visible, allowing for constant quality assurance and process monitoring without ever having to stop the machine.
Ultimate Flexibility for Any Production Line
One of the most significant challenges in factory design is floor plan integration. The Grand SZS750 solves this brilliantly. Both the tablet inlet and outlet ports can be freely adjusted in a 360° radius. This provides unparalleled flexibility, allowing the machine to be slotted into almost any existing production line layout without costly reorganization. Combined with a fully adjustable height column, it can be perfectly aligned with the output of virtually any máquina prensadora de pastillas model.
Designed for GMP: Easy Disassembly and Cleaning
In the pharmaceutical industry, cleanliness is non-negotiable to prevent cross-contamination. The Grand SZS750 is built with GMP (Good Manufacturing Practices) standards in mind. It is engineered for quick, simple disassembly and reassembly, ensuring that every part can be thoroughly cleaned with no dead angles where powder could accumulate. The process is largely tool-free, involving easy-to-use clamps and hand-turned knobs to separate the body sections and remove the entire sieve net for cleaning.
Robust, Reliable, and Quiet Operation
A production machine must be a workhorse. The Grand SZS750 is built for reliable, high-efficiency performance day in and day out. It operates with a very low noise level—less than 75 dB—which contributes to a safer and more pleasant working environment for operators. This quiet operation, powered by a robust 300W drive system, ensures efficiency without disruption.
Operational Excellence: Safety and Best Practices
A well-designed machine is also a safe one. The Grand SZS750 manual outlines several key best practices to ensure longevity and operator safety.
- Stationary Operation: The machine should never be moved while it is turned on. The vibration can cause collisions and damage components. Before moving, the power must be off, and the vertical column should be lowered to its lowest point to prevent damage to the lifting mechanism.
- Proper Startup Procedure: To protect the drive from sudden stress, the speed control knob must always be returned to its minimum initial position before turning the machine on.
- Correct Cleaning Protocols: To ensure a long life for all components, it is critical to use the right cleaning agents. Alcohol or harsh solvents should never be used on non-metal parts, especially the transparent observation window, as this can cause it to age, turn yellow, or become brittle and crack. Furthermore, the vibrating body and outer cover should never be washed directly with water or alcohol.
Conclusion: The Final Polish That Defines Quality
In the journey from powder to pill, the final step is what separates a good product from a great one. A high-quality tablet sieving machine is not a mere accessory; it is an essential instrument of quality control. It ensures that every single tablet leaving the production line is clean, perfectly polished, and free of imperfections.
By seamlessly integrating a Grand prensa de tabletas with a Grand SZS750 vibrating sieve, manufacturers can build a powerful, efficient, and automated line that delivers unparalleled quality. It’s the final, crucial touch that guarantees product integrity and builds confidence in your brand.
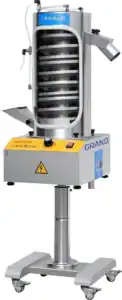