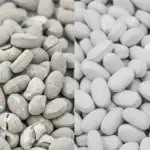
정제 체질 기계는 어떻게 모든 알약을 완벽하게 만들까요?
마이크로 분쇄기는 무엇에 사용되나요?
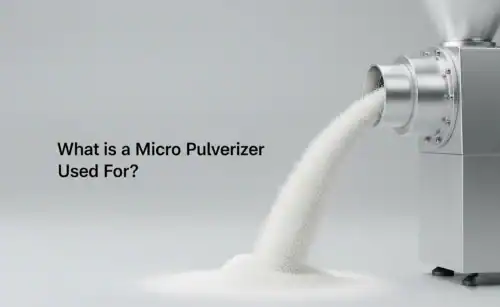
소개
In the advanced worlds of pharmaceutical science, food technology, and chemical engineering, true innovation often happens at a scale you can’t even see. The success of a life-saving drug, the texture of a gourmet food product, or the reactivity of a chemical compound frequently depends on one critical factor: the size of its constituent particles. Transforming coarse, granular materials into an ultra-fine, uniform powder is a foundational process, and the master of this transformation is the micro pulverizer.
This sophisticated piece of 크기 감소 장비 is far more than a simple grinder. It is an instrument of precision, designed to deconstruct materials down to the micron level with exceptional control. But what exactly is a micro mill pulverizer used for, and how does its technology directly impact the quality of a final product?
This guide will journey into the world of particle size reduction, exploring the critical applications of the Pharmaceutical micro-pulverizer. This advanced engineering separates an ordinary mill from a superior one, and this process is the crucial first step in a high-performance production line.
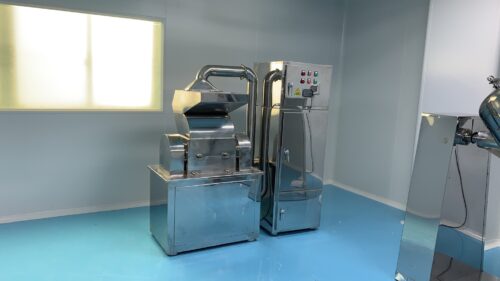

Why Particle Size is Everything: The Science of "Small"
Before we look inside the machine, let's understand why this process is so vital. Reducing a particle's size dramatically increases its surface area, which fundamentally alters its physical and chemical properties.
- 제약 분야에서: The bioavailability of a drug—the rate and extent to which the active ingredient is absorbed by the body—is heavily influenced by its dissolution rate. According to the Noyes-Whitney equation, a cornerstone of pharmaceutics, the dissolution rate is directly proportional to the surface area of the solid. By pulverizing an active pharmaceutical ingredient (API), we create a much finer powder with a vastly increased surface area, allowing it to dissolve faster in the body and become effective more quickly.
- In the Food Industry, Particle size dictates texture, mouthfeel, and solubility. The difference between granular sugar and powdered sugar is purely particle size, but it completely changes the final product. For instant, drink mixes, spices, and nutritional supplements, a fine powder ensures it dissolves smoothly and mixes homogeneously.
- In the Chemical Industry: In processes involving solid reactants, a smaller particle size increases the rate of chemical reactions. For products like pigments, resins, and polymers, a uniform, fine powder ensures a smooth, consistent finish and predictable behavior in formulations.
Deconstructing the Process: How a Modern Micro Pulverizer Works
At its heart, a pulverizer uses mechanical force—typically high-speed impact and shear—to break down materials. A rotor with fixed hammers or blades spins at thousands of RPM, striking the material against a liner or grinding track inside the chamber. However, this is where ordinary mills and advanced systems diverge.
An average mill relies on a physical screen or sieve at the outlet to control particle size. This method has significant drawbacks: screens can clog, they generate immense frictional heat, they are prone to wear, and they offer very limited and often inconsistent control over the final particle size.
This is why a state-of-the-art system, like the Grand Powder Micro Pulverizer, operates on a far more sophisticated principle.
Grand's Advantage #1: The Screenless Air Classifier System
The most significant innovation in the 멋진 micro pulverizer is the elimination of screens. Instead, it features an integrated, dynamic air classification wheel inside the grinding chamber.
- 작동 원리: As material is pulverized, a powerful fan creates a continuous, negative-pressure airflow that draws the particles upward toward the classifier wheel. This wheel spins at a high, variable speed. As particles enter the wheel, they are subjected to two competing forces: the outward centrifugal force from the wheel's rotation and the inward drag force from the airflow.
- Larger, heavier particles have too much momentum; the centrifugal force overcomes the airflow and throws them back into the grinding zone for further reduction.
- Finer, lighter particles are overcome by the airflow and are pulled through the classifier wheel to the collection system.
- The Benefit: This creates a closed-loop system that prevents over-grinding. More importantly, the final particle size is controlled with incredible precision simply by adjusting the rotational speed of the classifier wheel. A faster speed creates a stronger centrifugal force, allowing only the very finest particles to pass. A slower speed allows coarser particles through. This allows for an adjustable output from 80 to over 320 mesh, all without ever stopping the machine to change a screen.
Grand's Advantage #2: Cool Grinding with Dust-Controlled Mills
Friction generates heat, and heat is the enemy of many sensitive materials—sugars can caramelize, plastics can melt, and some APIs can degrade. The Grand micro mill pulverizer is one of the premier 먼지 제어 밀 on the market, using its airflow system to solve this problem.
- 작동 원리: The negative pressure system is constantly pulling ambient air through the grinding chamber. This continuous stream of air acts as a coolant, efficiently carrying away the heat generated during milling. This keeps the product temperature low (often below 65°C), making our system ideal for pulverizing heat-sensitive materials like sugar, plastics, and various pharmaceutical compounds.
- The Benefit: This cool-grinding capability preserves the integrity, color, and chemical stability of your material. Simultaneously, the fully enclosed, negative-pressure design means zero dust escapes into the production environment. This ensures operator safety, prevents cross-contamination, and meets the stringent requirements of cGMP manufacturing. All pulverized material is pneumatically conveyed to a high-efficiency cyclone separator and baghouse dust collector, ensuring maximum product yield and a clean workplace.
From Perfect Powder to Perfect Product: The Grand Ecosystem
Creating a uniform, fine powder with ideal characteristics is a monumental achievement, but it's only the first step. The true value is realized when this perfect powder is transformed into a finished product. This is where Grand's expertise extends across the entire production line.
A consistent powder from our Pharmaceutical micro-pulverizer is the ideal input for rotary tablet presses by Grandpackmachine. The powder's excellent flowability and uniform particle size ensure that the tablet press dies are filled evenly, resulting in tablets with highly consistent weight, hardness, and dosage accuracy.
Grand provides a seamless, integrated suite of pharmaceutical machinery. We can design a complete line that takes your raw material, pulverizes it to perfection, blends it, and then feeds it into a tablet press or capsule filler. From there, the journey can continue through our advanced packaging solutions, including blister machines and cartoners. We provide the A-to-Z solution, ensuring every step is synchronized for maximum quality and efficiency.
Conclusion: Investing in Precision, Not Just a Machine
To answer the question, "What is a micro pulverizer used for?"—it is used to unlock the hidden potential within your raw materials. It is the key that enables higher bioavailability, superior texture, and faster reactivity.
However, not all 크기 감소 장비 is created equal. An investment in an advanced system like the Grand Powder Micro Pulverizer is an investment in control, consistency, and cleanliness. The screenless air classifier, cool-grinding capability, and dust-free operation are not just features; they are foundational pillars that lead to a higher quality final product and a more efficient, profitable operation. When you are ready to master the art of the infinitesimal, you need more than a grinder—you need a complete particle processing solution.
FAQs: About the Grand Powder Micro Pulverizer
1.What makes the Grand micro pulverizer ideal for heat-sensitive materials?
The key is our advanced negative-pressure airflow system. Unlike conventional mills that trap heat, our system continuously pulls ambient air through the grinding chamber. This airflow acts as a coolant, carrying away the heat generated by friction and impact. This process keeps the material temperature low, preventing degradation, melting, or caramelization, making it perfect for sensitive pharmaceuticals, sugars, and certain plastics.
2.How precisely can I control the output particle size, and is it difficult to adjust?
Particle size control is both precise and incredibly simple. Our machine uses a screenless air classifier, not physical sieves. The rotational speed of the internal classifier wheel determines the final particle size (from 80 to over 320 mesh). To adjust the fineness, the operator simply changes the wheel's speed via the variable frequency drive (VFD) on the control panel. This can be done in seconds without stopping the machine, offering repeatable and highly accurate control over your powder's specifications.
3. Our facility operates under strict cGMP guidelines. How does the Grand micro mill pulverizer handle dust control and cleanability?
Our system is designed from the ground up for cGMP environments. The entire pulverizing and collection process operates under negative pressure, meaning dust cannot escape into the workspace. The powder is pneumatically conveyed through sealed pipes to a two-stage collection system (cyclone and baghouse filter), ensuring nearly 100% material recovery and a clean environment. Furthermore, the machine is designed for easy access and cleaning between batches to prevent cross-contamination.
