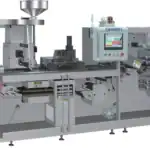
2025년 최고의 블리스터 포장기 추천
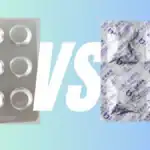
스트립팩 vs. 알루알루 블리스터 - 어떤 것이 귀하의 제품에 더 적합할까요?
블리스터 팩이 제약업계의 가장 중요한 요새인 이유는 무엇일까요?
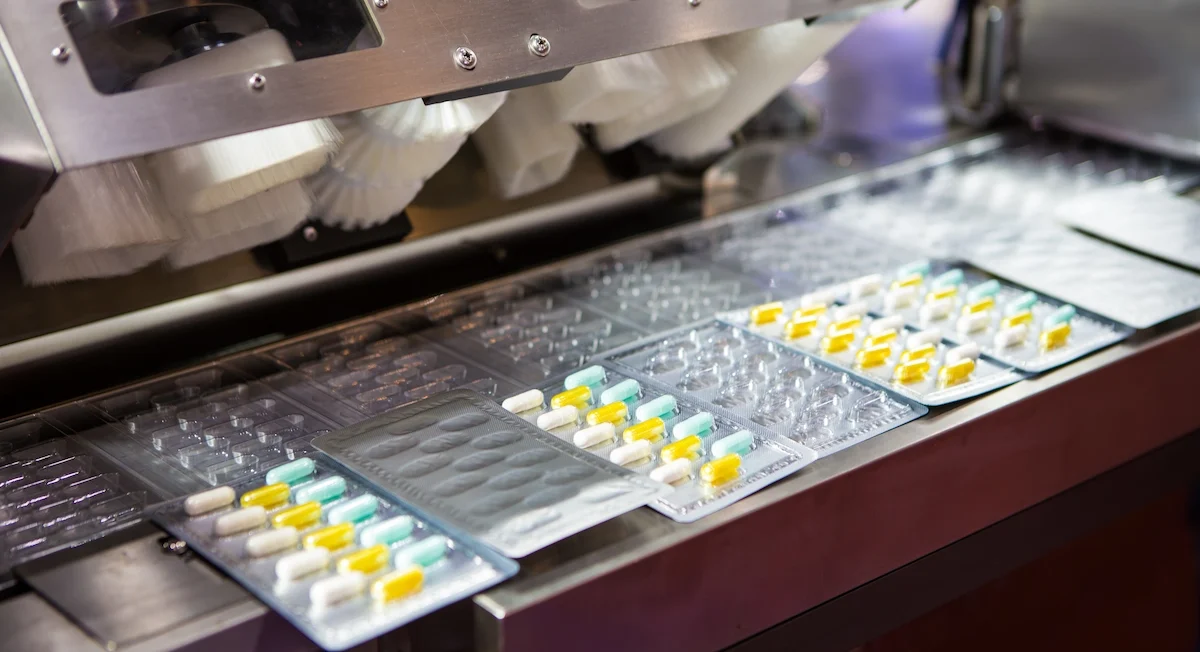
의학계에서는 신뢰가 전부입니다. 환자는 자신이 복용하려는 작은 정제나 캡슐이 안전하고 순수하며 의도한 치료 효과를 발휘할 것이라는 믿음을 가지고 있습니다. 이러한 믿음은 제약 업계의 조용하고 겸손한 영웅, 바로 블리스터 팩. 단순한 플라스틱과 호일 조각이 아닌, 이 유비쿼터스 블리스터 포장 는 재료 과학과 정밀 공학의 놀라운 성과로, 귀중한 내용물을 수많은 위협으로부터 보호하도록 설계된 소형 요새입니다.
병은 그 자리를 차지하지만, 병으로의 전환은 블리스터 포장 고형 제형에 대한 안전성은 확고한 위치를 차지해 왔으며, 그럴 만한 이유가 있습니다. 이 기술은 탁월한 수준의 보호, 무결성, 그리고 환자 안전을 제공합니다. 이 글에서는 이 중요한 기술을 분석하여 재료의 과학적 원리, 그 이점, 그리고 첨단 기술을 탐구합니다. 블리스터 포장 기계 현대 의학의 필수적인 수호자를 만드는 데 필요합니다.
요새의 해부학: 블리스터 팩 해체
ㅏ 블리스터 팩 간단해 보이지만, 그 구성 요소는 약물을 위한 안정적인 미세 환경을 조성하기 위해 엄격한 과학적 기준에 따라 선택되었습니다.
- 형성 필름(공동 요새): 제품을 담는 투명한 플라스틱 공간입니다. 일반적으로 플라스틱 시트를 가열하여 금형에 넣는 열성형을 통해 만들어집니다. 일반적인 재료는 다음과 같습니다.
- PVC(폴리염화비닐): 블리스터 포장의 핵심입니다. 비용 효율적이며 습기를 효과적으로 차단합니다.
- PVDC(폴리염화비닐리덴): PVC에 코팅되는 경우가 많은 PVDC는 습기와 산소 모두에 대한 탁월한 차단 효과를 제공합니다. PVC와 PVDC 중 어떤 것을 선택할지는 약물의 민감도에 따라 달라집니다. 여기서 핵심 지표는 수증기 투과율(WVTR); WVTR이 낮을수록 습기에 대한 보호가 더 좋다는 것을 의미합니다.
- 뚜껑이 있는 호일(뚫을 수 없는 문): 이것은 제품 내부를 밀봉하는 포일 백킹입니다. 일반적으로 단단하게 강화된 알루미늄으로 제작되어 거의 완벽한 차단막을 제공합니다. 산소 투과율(OTR) WVTR은 0에 가까워 약물을 대기로부터 효과적으로 차단합니다. 이는 약물 분해의 일반적인 경로인 산화를 방지하는 데 매우 중요합니다.
- 궁극의 요새: 콜드 폼 포일(Alu-Alu): 흡습성이 높거나 빛에 민감한 약물의 경우 표준 열성형 블리스터 팩 충분하지 않을 수도 있습니다. 여기가 알루알루 블리스터 팩 이 공정에서는 알루미늄 라미네이트를 "냉간 성형"(즉, 스탬핑)하여 캐비티 형태로 만듭니다. 순수 알루미늄이기 때문에 습기, 산소, 빛으로부터 완벽한 차단막을 형성하여 최고 수준의 보호 기능을 제공합니다.
"이유": 블리스터 포장의 우수성을 뒷받침하는 4가지 기둥
전 세계적으로 채택 블리스터 팩 제약 산업의 핵심적 요구를 직접 해결하는 4가지 확실한 장점을 바탕으로 구축되었습니다.
1번째 기둥: 흔들리지 않는 제품 보호 및 안정성. 모든 의약품 포장의 주요 기능은 약물을 보호하는 것입니다. 블리스터 팩의 밀폐된 공간은 각 용량을 외부 환경으로부터 격리하여 습기, 산소, 빛, 미생물 오염으로부터 보호합니다. 이를 통해 공장에서 환자에게 전달될 때까지 약물의 화학적, 물리적 무결성을 유지하여 유효기간까지 안전하고 효과적인 상태를 유지합니다.
2번째 기둥: 보장된 복용량 무결성 및 환자 준수. 모든 정제가 혼합된 병과 달리 각 복용량은 블리스터 팩 별도로 개최됩니다. 이는 두 가지 주요 환자 안전 이점을 제공합니다.
- 복용량 정확도: 태블릿이 서로 깨지거나 깨지는 것을 방지합니다.
- 규정 준수: 그만큼 블리스터 카드 요일이나 기타 표시를 인쇄하여 환자가 복용량을 추적하고 처방된 복용량을 준수할 수 있도록 명확하고 시각적인 방법을 제공합니다. 이 간단한 기능은 환자의 복약 순응도를 크게 향상시키는 것으로 나타났습니다.
3번째 기둥: 절대적인 변조 증거. 보안에 대한 우려가 높아지는 시대에 변조 증거는 협상의 여지가 없습니다. 블리스터 팩 이 기능은 본질적으로 제공됩니다. 제품에 접근하려면 호일 밀봉을 영구적으로 파기해야 합니다. 명백하고 돌이킬 수 없는 증거를 남기지 않고는 개봉하고 다시 밀봉할 방법이 없습니다. 이를 통해 환자와 의료 제공자는 약물이 손상되지 않았다는 확신을 가질 수 있습니다.
알루알루 vs. 블리스터 포장: 제품에 가장 적합한 장벽 선택
4번째 기둥: 향상된 정보 및 브랜딩 판지 뒷면 블리스터 카드또는 포장된 상자는 귀중한 공간을 제공합니다. 제품명, 용량, 제조 번호, 유통기한을 명확하게 인쇄할 수 있습니다. 이 정보는 개별 용량에 그대로 유지되는 반면, 외부 포장은 폐기될 수 있는 병에 들어 있습니다.
"How": 현대식 블리스터 포장기 내부 살펴보기
이러한 완벽한 요새를 수백만 개 만드는 데는 정교하고 고속의 기술이 필요합니다. 정제 포장기. 이 프로세스는 복잡하지만 단일 부품으로 실행되는 4가지 핵심 단계로 나눌 수 있습니다. 블리스터 포장 기계.
- 형성 스테이션: 성형 필름은 풀리고 부드럽게 가열됩니다. 그런 다음 성형 스테이션으로 이동하여 가압 공기가 냉각된 금형으로 밀어 넣어 정밀한 캐비티를 형성합니다. 블리스터 포장. 을 위한 알루알루 물집을 만드는 이 스테이션에서는 열을 가하지 않고도 스탬프를 사용해 호일을 원하는 모양으로 눌러줍니다.
- 주유소: 새로 형성된 공동(cavity)들이 충전 스테이션으로 이동합니다. 여기서 전용 공급기(정제용 브러시 박스, 캡슐용 중력 공급기)가 각 공동에 단일 용량을 정확하게 주입합니다. 비전 시스템을 사용하여 모든 공동이 정확하게 충전되었는지 확인할 수 있습니다.
- 봉인 스테이션: 리딩 호일은 채워진 웹과 접촉합니다. 블리스터 포장 밀봉기 가열되고 종종 널링 처리된 플래튼이 정밀한 압력과 열을 가하는 스테이션입니다. 이렇게 하면 포일의 실란트 층이 성형 필름에 접착되어 각 캐비티 주변에 완벽한 밀폐 밀봉이 형성됩니다.
- 마무리 스테이션: 마지막 섹션에서 블리스터 팩 기계밀봉된 웹에는 제조 번호/유통기한 정보가 코딩됩니다. 그런 다음 천공 및 절단 다이를 통과하여 웹을 최종 개별 제품으로 분리합니다. 블리스터 팩 또는 카드를 포장하여 다음 단계의 포장을 준비합니다.
거대한 생태계: 블리스터 팩 너머
완벽한 블리스터 팩 중요한 성과이지만, 시장에 출시할 수 있는 제품을 만드는 여정은 여기서 끝나지 않습니다. 바로 이 부분에서 Grand의 완벽하고 통합된 제품군에 대한 전문성이 전략적 우위를 제공합니다.
완성된 물집 주머니 또는 카드가 원활하게 흐릅니다. 그랜드팩 블리스터 기계 포장 줄을 세우다 그랜드 카토닝 머신. 이 정교한 시스템은 전단지를 자동으로 공급하고, 블리스터 카드를 방향을 지정하고, 밀봉하기 전에 제품 상자에 삽입하여 최종 제품을 생성합니다. 캡슐 충전 블리스터 박스.
하지만 자동화는 여기서 끝나지 않습니다. 이 상자들은 다음으로 전달될 수 있습니다. 그랜드 케이스 패커, 이를 그룹화하여 배송 케이스에 포장합니다. 마지막으로, 그랜드 로보틱 팔레타이저 이러한 케이스를 팔레트 위에 쌓아 안정적이고 추적 가능한 화물을 만들어 유통에 바로 투입할 수 있습니다. Grand는 완벽한 솔루션을 제공함으로써 원액 정제부터 최종 팔레트까지 원활하고 효율적이며 신뢰할 수 있는 프로세스를 보장합니다.
결론: 품질에 대한 약속, 호일로 봉인됨
그만큼 블리스터 팩 단순한 용기 그 이상입니다. 약물의 온전성과 환자의 안전을 위한 최후의 방어선 역할을 하는 고도로 설계된 시스템입니다. 이 시스템의 중요성이 커진 것은 개별 약물의 용량을 보호, 식별 및 확보하는 탁월한 능력 덕분입니다.
올바른 재료를 선택하고, 가장 중요한 것은 올바른 것을 선택하는 것입니다. 블리스터 포장 기계 모든 제약 제조업체에게 중요한 결정입니다. 고품질의 신뢰할 수 있는 기계는 이론적 보호를 보장합니다. 블리스터 포장 수백만 번 이상 완벽하게 구현되었습니다. 모든 포장에 품질에 대한 헌신이 담겨 있습니다.
FAQ: Grand의 캡슐 충전 및 포장 라인에 대한 정보
- 그랜드 캡슐 필러는 어떻게 캡슐을 부드럽게 다루어 고속 블리스터 포장 기계로 옮기기에 적합하도록 보장합니까? Grand의 캡슐 충진기는 부드러운 조작에 중점을 두고 설계되었습니다. 정밀하게 가공된 연마 공구와 최적화된 이송 메커니즘을 사용하여 캡슐에 가해지는 기계적 스트레스를 최소화합니다. 배출 과정은 부드럽고 제어되어, 충전되고 잠긴 캡슐이 완벽하게 손상되지 않고 올바른 방향으로 배출되어 후속 공정으로 원활하게 투입될 수 있도록 합니다. 블리스터 팩 기계.
- 그랜드 캡슐 필러를 그랜드 캡슐 필러와 동기화할 수 있나요? 블리스터 기계 포장 연속작업을 위한 라인? 물론입니다. 이것이 그랜드 생태계의 핵심 강점입니다. 저희 캡슐 필러와 블리스터 기계는 전자 통신을 지원하도록 설계되었습니다. 통합 제어 시스템을 통해 단일 연속 라인으로 통합될 수 있습니다. 블리스터 기계는 필러에서 캡슐을 "호출"하여 기계 간 버퍼를 항상 최적화할 수 있습니다. 이러한 동기화된 작동은 병목 현상을 제거하고 전체 라인의 효율성을 극대화합니다.
- 저희는 두 가지 다른 캡슐을 조합한 제품을 생산합니다. Grand에서 여러 제품을 담을 수 있는 블리스터 카드에 이러한 캡슐을 채우는 솔루션을 제공해 주실 수 있을까요? 네, 이러한 용도에 맞는 맞춤형 솔루션을 설계할 수 있습니다. 여기에는 각 캡슐 유형별로 하나씩, 두 개의 별도 동기화된 캡슐 필러를 사용하여 맞춤형 이송 시스템으로 공급하는 방식이 포함될 수 있습니다. 블리스터 포장기. 그런 다음 블리스터 기계는 동일한 지정된 공동에 다른 캡슐을 놓도록 프로그래밍됩니다. 블리스터 카드귀사의 다양한 제품 요구 사항에 대한 완전하고 자동화된 솔루션을 제공합니다.
참고문헌
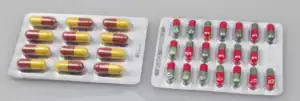
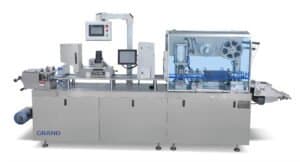