
GrandPack présente ses machines d'emballage pharmaceutique avancées au CPHI et au PMEC China 2025
Comment la granulation en lit fluidisé révolutionne la fabrication pharmaceutique ?
La danse des particules
Dans le monde de la fabrication pharmaceutique, la précision n'est pas seulement un objectif ; c'est une obligation. Le passage d'une poudre fine, souvent indisciplinée, de principe actif (API) à un comprimé parfait et uniforme est une merveille d'ingénierie chimique et mécanique. Depuis des décennies, la granulation, processus qui consiste à transformer des poudres fines en granules plus résistants, plus denses et plus prévisibles, constitue un défi majeur. Si les méthodes traditionnelles ont fait leurs preuves, l'industrie pharmaceutique moderne exige davantage d'efficacité, de contrôle et de qualité. C'est là que réside l'élégance de la science. granulation en lit fluidisé (FBG) occupe le devant de la scène, transformant le processus d’un travail en plusieurs étapes en une forme d’art parfaitement intégrée.
Cette plongée en profondeur explorera les principes derrière cette technologie révolutionnaire, ses avantages considérables pour la production de formes posologiques solides supérieures et la manière dont les équipements de pointe, comme les solutions proposées par Grand, établissent de nouvelles références pour la fabrication cGMP.
Avant la danse : pourquoi avons-nous besoin de granulation ?
Imaginez essayer de construire un mur solide et stable avec du sable fin. C'est quasiment impossible. Les particules ne collent pas entre elles, elles produisent de la poussière et leur écoulement est imprévisible. Les poudres pharmaceutiques se comportent souvent de la même manière. Les poudres brutes, en particulier les mélanges principes actifs-excipients, souffrent fréquemment des problèmes suivants :
Faible fluidité : Il est donc difficile de déplacer le matériau de manière uniforme à travers l'équipement de traitement et dans les matrices de comprimés.
Forte tendance à la ségrégation : Les particules de différentes tailles dans le mélange peuvent se séparer, ce qui entraîne un contenu médicamenteux non uniforme dans le comprimé final, ce qui constitue un défaut de qualité critique.
Faible densité apparente : La poudre est trop « moelleuse », ce qui la rend difficile à compresser en un comprimé durable.
Génération de poussière : Présente des risques d’exposition de l’opérateur et de contamination croisée.
La granulation résout ces problèmes en « collant » les particules de poudre ensemble pour former des agglomérats plus gros et plus uniformes. Ces granulés s'écoulent comme un liquide, résistent à la ségrégation, se compriment parfaitement et sont pratiquement exempts de poussière.
Démystifier le lit fluidisé : comment la magie opère
Fondamentalement, la granulation en lit fluidisé est un procédé « monopot ». Cela signifie que les trois étapes critiques de mélange, granulation et séchage tout se déroule dans la même chambre, ce qui représente un progrès significatif en termes d'efficacité par rapport aux méthodes plus anciennes qui nécessitaient un équipement séparé pour chaque étape.
Décomposons ce processus élégant, en faisant référence à un système avancé typique comme le Séchoir granulateur à ébullition série Grand FL.
Étape 1 : L'ouverture - Préparation de l'air et fluidisation
Le processus commence avant même que la poudre n'entre en jeu. L'air d'admission est aspiré dans le système par un puissant ventilateur. Dans une machine conforme aux BPF, cet air n'est pas seulement l'air ambiant ; il est méticuleusement purifié. Comme l'indiquent les spécifications des équipements de pointe, système de filtration à trois étages (HEPA primaire, moyen et haute efficacité) est standard, garantissant que l'air entrant dans la chambre est stérile et exempt de contaminants. Cet air purifié est ensuite chauffé à une température précise et prédéfinie.
Le mélange de poudre est chargé dans le récipient. L'air chauffé et filtré est ensuite propulsé vers le haut à travers une plaque de distribution d'air spéciale située au fond du récipient. La vitesse de cet air est soigneusement contrôlée. En augmentant, elle atteint un point où la traînée aérodynamique exercée sur les particules neutralise la gravité. Le lit de poudre se dilate et les particules sont suspendues dans le flux d'air, se déplaçant librement et aléatoirement. C'est le état « fluidisé »—la poudre se comporte comme un liquide en ébullition, créant l'environnement idéal pour l'étape suivante. C'est la danse des particules.
Étape 2 : L'acte principal - Atomisation et agglomération du liant
Les particules étant en suspension dans un état homogène et fluide, une solution de liant liquide est introduite. Cette opération s'effectue via une buse de pulvérisation de haute précision, généralement positionnée en haut (granulation par pulvérisation par le haut). La buse atomise le liant en microgouttelettes.
En traversant le lit fluidisé, ces gouttelettes entrent en contact avec les particules de poudre en suspension, mouillant ainsi leur surface. Le mouvement constant et aléatoire des particules provoque leur collision. À cet endroit, le liant liquide agit comme un pont, les agglomérant. agglomérerCe processus se poursuit, les particules se développant progressivement couche par couche, formant des granulés.
Le niveau de contrôle est ici extraordinaire. Selon une étude du Journal international de pharmacieDes paramètres clés tels que le débit de pulvérisation du liant, la pression d'atomisation et la température de l'air d'admission influencent directement les caractéristiques finales des granulés, notamment la granulométrie et la densité. Les systèmes modernes contrôlés par PLC permettent aux opérateurs d'affiner ces variables afin d'obtenir les granulés aux propriétés exactes requises pour une formulation spécifique.
Étape 3 : La finale - Séchage intégré
Une fois la granulométrie et la densité souhaitées atteintes, la pulvérisation du liant est interrompue, mais le flux d'air chaud fluidisé se poursuit. Le processus passe en douceur de la granulation au séchage, le tout dans la même chambre. Le flux continu d'air chaud élimine efficacement l'humidité des granulés jusqu'à l'atteinte d'un point final cible, souvent déterminé par la température du produit ou la perte à la dessiccation (LOD).
Diagramme de séchage en une étape
Comme les granulés restent fluidifiés pendant le séchage, le processus est incroyablement efficace et uniforme. Il n'y a pas de points chauds et le produit final présente un taux d'humidité résiduelle très faible et constant, essentiel à sa stabilité et à sa durée de conservation.
Les avantages considérables de la technologie du lit fluidisé
Le passage à la granulation en lit fluidisé dans l’industrie pharmaceutique n’est pas seulement une tendance ; il est motivé par des avantages tangibles et convaincants.
Efficacité et débit inégalés : Le procédé monocuve réduit considérablement le temps de traitement. Il n'est pas nécessaire de transférer la masse humide d'un mélangeur vers un sécheur séparé, ce qui permet de gagner du temps, de réduire les coûts de main-d'œuvre et de minimiser les pertes de matière.
Granulés de qualité et de consistance supérieures : L'environnement contrôlé produit des granulés hautement uniformes, poreux et sphériques. Il en résulte une excellente fluidité et compressibilité, ce qui permet d'obtenir des comprimés plus homogènes en termes de poids et de dureté. La distribution granulométrique homogène (PSD) est un élément fondamental de la qualité par conception (QbD).
Doux pour les API sensibles à la chaleur : Comparé au séchage traditionnel sur plateau, le séchage en lit fluidisé fonctionne à des températures plus basses pendant des durées plus courtes grâce à son efficacité élevée. Il constitue donc le choix idéal pour les formulations contenant des principes actifs thermosensibles.
Sécurité renforcée et conformité aux BPF : En tant que système fermé, le FBG réduit considérablement la production de poussière, minimisant ainsi l'exposition des opérateurs et évitant la contamination croisée entre les lots. Les machines modernes sont équipées de dispositifs de sécurité tels que soupapes de surpression mécaniques automatiques pour gérer toute accumulation de pression inattendue, garantissant un environnement de fonctionnement sûr.
Grand : Ingénierie de l'avenir de la granulation
Comprendre la théorie est une chose ; disposer du bon outil en est une autre. C'est là que l'engagement envers l'excellence technique devient primordial. Des entreprises comme Grandiose se sont concentrés sur la création Granulateurs à lit fluidisé et Sécheurs-granulateurs à ébullition GrandPack qui non seulement exécutent le processus de manière impeccable, mais intègrent également les dernières avancées en matière d'automatisation et de conformité.
Leurs systèmes, comme le Série FL, incarnent les principes de la fabrication pharmaceutique moderne :
Automatisation et intégrité des données : Equipé d'un Système PLC et IHM intuitiveCes machines offrent une automatisation complète et un suivi des processus. La capacité de stockage, d'exportation et d'impression des données de lots est essentielle à la tenue des registres et est conçue pour soutenir Conformité à la partie 11 du 21 CFR.
Nettoyage validé : Pour maximiser le temps de disponibilité et garantir la pureté, une option Système de nettoyage automatique WIP (Wash-In-Place) intégrable. Cela permet d'obtenir un processus de nettoyage reproductible et validable, essentiel dans une installation multi-produits.
Contrôle de précision : Les réglages variables du débit d'air, de la température et du débit de pulvérisation permettent le développement et l'exécution de recettes de granulation robustes et reproductibles, permettant aux formulateurs d'atteindre le profil de produit souhaité en toute confiance.
Au-delà de la granulation : la technologie de la plateforme
La polyvalence de la technologie du lit fluidisé va même au-delà de la granulation. Le même équipement de base, avec quelques modifications mineures (comme un insert Wurster pour la pulvérisation par le bas), peut être utilisé pour :
Revêtement de particules : Application d'enrobages fonctionnels pour le masquage du goût, la libération entérique ou la libération prolongée.
Granulation : Construire des couches sur un matériau de graine de base.
Séchage simple de la poudre : En tant que séchoir autonome très efficace.
Cela fait d’un processeur à lit fluidisé de haute qualité une plate-forme multifonctionnelle et un investissement judicieux pour toute installation de développement ou de fabrication pharmaceutique.
Conclusion : Choisir son partenaire pour la danse des particules
La granulation en lit fluidisé est plus qu'un simple procédé ; c'est un avantage stratégique. Elle permet de créer des formes galéniques solides de meilleure qualité, avec plus d'efficacité, de sécurité et un niveau de contrôle sans précédent. Face au durcissement des normes réglementaires et à la demande croissante de formulations complexes, la maîtrise de cette technologie est désormais incontournable.
Lors du choix d'un système, ne vous limitez pas aux spécifications de base. Privilégiez une construction robuste, un contrôle intelligent des processus et une conception fondée sur une compréhension approfondie des principes BPF. Un partenariat avec un fabricant comme Grand, qui fournit non seulement la machine, mais aussi l'expertise et le support, garantit que votre installation est équipée non seulement pour relever les défis d'aujourd'hui, mais aussi pour l'avenir de la fabrication pharmaceutique.
FAQ : À propos des granulateurs à lit fluidisé de Grand
1. Comment le système FBG de Grand garantit-il la pureté du produit et empêche-t-il la contamination croisée entre différents lots ? Les systèmes Grand sont conçus dès le départ pour être conformes aux BPF. La pureté des produits est préservée grâce à une approche multidimensionnelle : un environnement de traitement mono-cuve étanche minimise l'exposition ; un système de filtration HEPA en trois étapes assure un air de traitement stérile ; et le système WIP (Wash-In-Place) entièrement automatisé, en option, effectue un cycle de nettoyage validé pour éliminer complètement tous les résidus, garantissant ainsi l'absence de contamination entre les produits.
2. Le granulateur à lit fluidisé Grand est-il adapté au traitement de formulations contenant des API sensibles à la chaleur ? Absolument. C'est l'un de ses principaux atouts. Le procédé de fluidisation offre un transfert de chaleur incroyablement efficace, permettant de sécher les granulés à des températures et des durées nettement plus basses qu'avec les sécheurs à plateaux statiques. Le PLC du système assure un contrôle précis de la température de l'air d'admission, garantissant ainsi que la température du produit ne dépasse jamais son seuil critique, préservant ainsi la stabilité et l'efficacité des ingrédients sensibles.
3. Comment le granulateur de Grand prend-il en charge les exigences modernes d'intégrité des données telles que 21 CFR Part 11 ? Les granulateurs Grand sont équipés d'un automate programmable industriel performant et d'une IHM intuitive, constituant la base d'un système conforme. Le système de contrôle est conçu pour être conforme à la norme 21 CFR Part 11, avec des niveaux d'accès utilisateur sécurisés, des signatures électroniques et la possibilité d'enregistrer tous les paramètres critiques du processus (par exemple, temps, température, débit d'air, débit de pulvérisation). Toutes les données de lot peuvent être stockées, imprimées et exportées en toute sécurité pour créer un enregistrement de lot électronique complet et inaltérable, ainsi qu'une piste d'audit claire pour les contrôles réglementaires.
Développez votre entreprise avec Grand
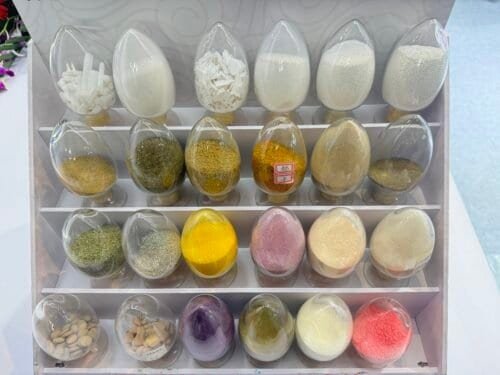
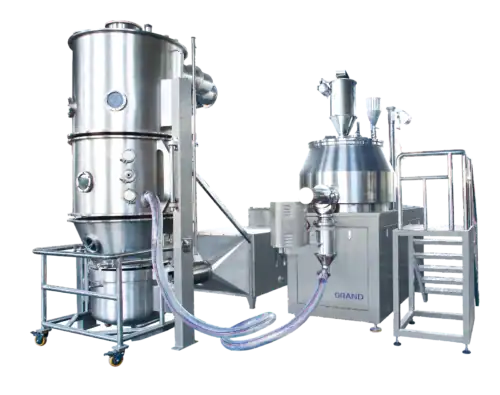