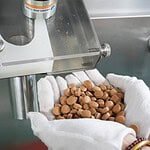
The Ultimate Guide To Rotary Tablet Press Machines
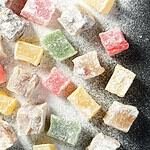
Which is more popular in the health care product market: gummies or compound tablets?
Thermoforming Blister Packaging Machine – Definition, Types, How It Works, and Why You Need One!
Do you know the see-through plastic “bubbles” that hold a pill or a mint or a tiny toy?
They’re called blister packs, and they’re produced using some really efficient machines.
In this article, I will cover all the aspects of blister packaging and also the machinery used to produce blister packaging. You'll learn:
- What Thermoforming blister packaging is?
- The different types of Thermoforming blister packaging?
- How Thermoforming blister packaging machines work?
- The parts of a Thermoforming blister machine?
- How to use a Thermoforming blister machine?
- And more!
Let's get started!
What is a Thermoforming Blister Packaging Machine?
A Thermoforming Blister Packaging Machine is a type of equipment used in the pharmaceutical, food, and consumer goods industries to package products into rigid, clear plastic "blisters." These blisters are formed by heating a plastic sheet to a pliable temperature and then molding it into a cavity where the product is placed.
A flexible lid material, often foil or another type of plastic, is then sealed over the blister to secure the product inside. This process is primarily used for packaging tablets, capsules, consumer goods, hardware, and other products that require individual, clear protection.
There are a number of names for Thermoforming Blister Packs they're also called bubble packs, clamshells or display packs. But they all have that same distinctly bubble-like shape. You’ve likely encountered (and grappled with) blister packs of assorted shapes and sizes:
- Drug tablets and capsules
- Cart filled with packs of gum and mints at checkout
- Things you can get on store shelves, such as toys, gadgets
- Hardware (screws and nails) from the home center
The products are safely held within their molding of blister packs. And the clear plastic means you can see what you’re getting before you buy it.
But how did blister(Thermoforming) packs become so popular?
Well their story stretches back to the 1930s. The engineers worked out how to shape flexible materials into bubble forms through the application of heat and pressure.
The early rituals of blister packing could preserve goods in ways that boxes and bottles could not. The packs were lightweight, inexpensive to produce and easy to stack and ship.
Over the next few years, more powerful spells were created to both produce the blister packs faster, and also seal them more securely. Soon industries across the land understood their wizardly advantages:
- Pharmacies preferred blister packs to protect each pill and to make dosing easy. No more searching for loose medicines!
- Confections like candy and gum loved the bright display of their products in blister packs. And they were selling to everyone!
- Hardware manufacturers praised such blister packs for keeping the little things inside them from getting scratched and dented. Now there was a way to send every widget and gizmo correctly!
Ths packaging had great features. Even today, blister packs are prized for such attributes as:
- Inexpensive production cost
- Durable protection
- Child proof and Tamper resistant
- Lightweight and compact
- Recyclable materials
- Crystal clear visibility of contents
And all of these many gifts have surely earned blister packs a permanent place among the pantheon of packaging!
Types of Thermoforming Blister Packaging
Not Thermoforming Blister Packs are all the same, there are a diverse range of products! Like noble clans, blister packs are part of three broad tribes:
Plastic-Paperboard Packs
The majority of blister packs use heat-sealed plastic bubbles on paperboard backing.
Plastic-paperboard packs are the most easily and least expensively manufactured. That makes them perfect for cheap items that don’t need much protection.
The next time you are waiting in a checkout line, take a gander and you’ll probably see these plastic blister packs, backed with paper, containing low-cost items.
Plastic-Plastic Packs
All the packs are 100% plastic materials from the bubbles to the backing.
As an added benefit, the all-plastic construction makes for an excellent moisture barrier. That’s how plastic-plastic blister packs keep contents ultra-dry.
These plastic bubble societies will be found on moisture-sensitive valuables that are protected, such as:
- Electronics that were submerged but do not short-circuit
- Metal parts that can rust and corrode
- Stale would spoil dry products (eg crisps and crackers) shallowly.
Air-abrasive, its plastic shell is made from corrosion-resistant materials, so it's protecting its cargo from humidity.
Aluminum-Plastic Packs
Aluminum-plastic is used for packing the most important goods.
They fuse durable aluminum foil backing onto tough plastic bubbles. Aluminum acts as a barrier to air, light, and moisture.
And that’s why aluminum-plastic packs are trusted to preserve its precious contents, like:
- Drugs that must retain their effectiveness
- Devices that are sterilised before use
- Caustic chemicals that can eat through plastic
- Perishable food that is sensitive to air
Therefore, aluminum-plastic packs answer the call when contents need maximum protection!
It turns out that each blister pack clan has its way to play. Now that you know the big tribes, watch for them on your travels!
Parts of a Thermoforming Blister Packaging Machine
We tracked down the origins and variations of the magic blister packs. But how exactly do they come to exist? What are these miraculous devices that call them up?
Let's inspect the anatomy of thermoforming blister packaging machines to learn their secrets!
Material Feeder
Our journey begins here, where the blister forming film is loaded. This is a square sheet of thin plastic that is going to be shaped into bubbles.
The forming film unwinding station holds a huge roll of the film and unwinds it into the blister machine.
Preheating Station
Next is the hot preheating cavern, where the forming movile film is transferred. Heating plates use fire to heat up and soften the film, allowing for shaping.
That magic gives the film flexibility, which allows it to be sliced, shaped into blisters.
Forming Station
Here, the mold descends to push the film into bubble shapes using gusts of air. This shapes the actual blister cavities.
Potions Reservoir
While blisters form, the machine's hopper reservoir holds potions, tonics or whatever goods need packaging.
These items are dispensed into the open blister bubbles as they pass beneath the hopper.
Heat Sealing Station
The filled blister packs journey to the sealing sanctum next.
A hot surface presses another plastic film - called the lidding film - onto the blisters. This uses heat to seal the film across the pack, creating an airtight barrier.
Stamping Station
Some blister packs travel to the stamping station where embossing plates press designs and patterns into the plastic.
This station also makes perforated lines for easy opening.
Cutting Crucible
Finally at the cutting crucible, a magical blade slices through the blister packs, dividing them into individual units.
The finished blister packs exit the machine while leftover film gets rewound.
How Does It Work?
This is how the blister machines work step by step:
Step I - Setting the Stage
First, our machine operator sets the giant rolls of forming film and lidding film.
And these two sheets of thin plastic will become the blisters and sealing layer.
Step II - Softening the Film
Next up on the stage is the preheating station. The forming film enters and gently glides in between, lamination film.
300 degrees might be nothing to you, but the plates are blasted with flames that heat them to hotter than 400°F! The movie becomes squishy until it’s malleably pliable.
Step III - Molding the Blisters
Once it’s prepped for molding, the film proceeds to the forming station.
There the magical forming mold comes down, air jets blowing into the void as it does. The mold processes the heated film into bubbling shapes within its troughs.
Before you know it, an entire sheet of blister bubbles is sprouting! We are molded film, eager for its contents.
Step IV - Filling the Blisters
And then we come to the next section - the actual products!
The goods cascade from the hopper into the exposed blister bubbles beneath it.
Each blister pack contains pills, mints, toys, hardware or whatever the machine is packaging.
Step V - Sealing the Packs
The filled blisters move down the line to the sealing station.
The thin lidding film at the top is unwound and heat sealed onto the blisters that are filled. This process involves compression of two films with special heated plates.
The heat welds the plastic films together in a hermetic, tamper-evident seal!
Step VI - The Final Touches
In one last flourish, the sealed blister packs go through even more stations:
- This is where textured plates squish decorative patterns and shapes into the pack, at the embossing station.
- The perforating station places very small blades that poke dotted lines to make things easier to open.
These final touches make up the protective outer layer of the blister pack.
Step VII - Separating the Packs
Finally, a die that cuts down that large blister sheet into individual packs.
Our finished pouch jars tumble out, full and ready to guard their content!
Blister packaging for another full house, though recycling some stray plastic film does occur and the show goes on!
Tips for Care and Operation
With great power comes great responsibility, oh wise wizard. So if you are lucky enough to have your own machine for blister packaging, you have to use it wisely!
Here’s advice for befriending your machine:
- Take it easy - Always insert the film through the stations gingerly, or you may end up tearing and creating a jam.
- Warm, not hot - The plates should be warm enough that they can gently mold films. Avoid scorching!
- Turn out completely - Blisters should have the correct raw materials in them prior to sealing. Half-filled packs can fail.
- Use the right air pressures – Apply enough pressure that the molds blister completely, but not so much that it pushes it.
- Watch out for the blades - Blistered, soiled perforating and cutting blades are dangerous, so change them (frequently) so everything is spiffy.
- Watch out for clogged arteries - Pay attention to stations that might become bottlenecks and cause production to halt.
- Scheduled downtimes - Schedule regular action breaks to maintain and clean the machine.
- Repair mechanical issues - Make sure to troubleshoot any mechanical problems so you have a happy machine.
A little due diligence and vigilance and your bubble wand will spit out plastic bubbles without a problem!
Thermoforming vs Cold Forming
There are lots of secrets of blister packing machines. However, there is another trick up the sleeve - THE competing spell of cold forming!
Maybe, cold forming powers would be better instead. Now let’s contrast the two blister magic arts:
Thermoforming | Cold Forming |
Heats plastic film to mold it | Presses layers of aluminum together instead |
Much lower production cost | More expensive process |
High-speed operation | Slower production rate |
Recyclable after use | Not easily recycled |
Basic barrier against air/moisture | Maximum barrier properties |
As you see above, each spell has its pros and cons:
- Thermoforming is cheaper and quicker to conduct. It is sufficient for most normal blister pack operations.
- For the worthy contents requiring an ironclad barrier, though, an aluminum cold end will always trump a plastic one.
So pack carefully, then pick which magic is best for the quest!
Thermoforming Blister Packaging Machine Applications
Thermoforming blister packaging machines have a wide range of applications across various industries:
Pharmaceutical Industry: The most common application, where tablets and capsules are packaged to protect them from moisture, air, and contamination. Thermoforming machines allow for precise dosing and easy access for consumers.
Food Packaging: Food products like candies, mints, and snacks can be efficiently packaged using blister packs, keeping them fresh and tamper-resistant.
Consumer Electronics: Small electronic components, such as batteries, cables, and gadgets, are often packaged in thermoformed blister packs to ensure they are securely held in place and visible to consumers.
Hardware and Tools: Small hardware items like screws, nails, and bolts can be packaged using blister packs to avoid damage during transportation and to display the product clearly.
Thermoforming Blister Packaging Machine Types
Thermoforming blister packaging machines are generally categorized based on their production capabilities, features, and the type of products they handle:
Single-Cavity Thermoforming Machines: Designed for small-scale production or products that require individual packaging. These machines form one blister at a time.
Multi-Cavity Thermoforming Machines: These machines are capable of producing multiple blisters in one cycle, making them ideal for large-scale production of pharmaceutical tablets, consumer goods, and more.
Automatic Thermoforming Machines: Fully automated machines that handle everything from film feeding, forming, product placement, sealing, and cutting. These machines are typically used in large manufacturing settings where speed and efficiency are critical.
Semi-Automatic Thermoforming Machines: These machines may require manual intervention for certain steps, such as product placement, making them more suitable for smaller production runs or for industries where customization is needed.
FAQ
What if I use the wrong thickness for the plastic sheet?
When the plastic sheet is too thin, blisters will burst during blasting. If the sheets are too thick, they will not heat (or mold) properly. Stick to what the machine manufacturer recommends for thickness - generally 10-20 mil. Things like thinner plastics like PET make the best blisters.
Can I speed up the time it takes to develop blisters?
We have a lot of defects when we try to blister too quick. This allows the plastic to fully conform to the mold cavities. Omitting this step may lead to misshaped or warped blisters. Log so you can get medium cycle times that make nice blisters on your machine.
What to do when my sewing machine jam?
Common jams are often caused by heat-softened plastic building up where it shouldn’t. And be sure to let your machine cool down, as the plastic films can become gummy if they overheat.” Any melted plastic on the heating plates or forming molds should be thoroughly cleaned off to avoid more jams.
What do I do about blisters that aren’t developing properly?
Check your hopper, and make sure it is set up to dispense the right amount of product. You might need to change the vibration or the speed Or if things are getting stuck then slightly widen the fill holes. It requires a bit of trial and error to get these settings right for filling.
How do I make a perforated or scored line?
If you want to create openings or score lines, your machine should at least have an embossing or perforating unit. Dotted lines/creases to assist with tearing packs apart: In this station, there are specialized male/female perforating tools that punch out serpentine dotted lines or creases. Screen the size appropriate blister pack perforation tools
Do you seal blisters no heat?
Different types of plastic films require a heat sealing to provide a strong, tamper-evident seal. Cold glue seal is not too strong. You can still save on energy with lower temperature sealers, or cost-conscious impulse sealers.
Why do my pack graphics appear distorted?
This is when you fail to consider the stretching of the plastic during formation. Work with your graphic designer to pre-distort artwork to account for shaping. Or put graphics on the neutral axis so it does not stretch. This allows for better patterns on curved blisters and prevents for warped or wobbly patterns.
How do I cut individual blister packs apart?
Rotary cutters, steel rule dies, or lasers can all slice blister packs cleanly. Just be sure to align the cutter precisely before trimming. Poor alignment will leave packs stuck together or with rough edges. Indexing conveyors help match the cutter position.
What should I lubricate on my blister machine?
The thing is, there is no one-size-fits-all answer to the question of what parts of your blister machine to lubricate.
It makes blister machines run with more ease. Conveyor bushings, surface plates, linear slides, drive chains, and air cylinders should be oiled with light machine oil. Not lubricate the sealing station anymore, so that do not get any traces of oil.
How long will these machines live for?
With the care and proper maintenance, a decent blister machine will last you a decade or more. The answer is in replacing wear items (heating plates, seals and cutters, for example) to extend the life of your machine. Opting for a durable stainless steel or aluminum design adds to longevity as well.
Why are the bubbles on my blisters asymmetrical?
If you see uneven or lopsided blister bubbles, the plastic film is not being heated evenly. You need to check if your heating plates are in good condition without any burn and dirt. A bit of warmth makes the castable jiggle enough to seat in the entire mold.
Can I bring food with blisters not pills?
Yep, you sure can! Blisters are great for snack, candy, jerky, or stuff you eat. Just be sure the plastic films you choose are food-grade films that won’t leach chemicals. Just be sure to really clean your machine first, so no old medicine gunk gets into there.
What should I do if any melted plastic clogs my machine?
Don’t let gunk build up,stop the machine right away. Just make sure to scrape off any sticky melted bits. Next, insulate cooler plastics films - and run the cooling fan.
Final Thoughts
In this guide you’ve learned:
- Blister packaging provides visibility and product protection Blister packaging is normal packaging that consists of a cavity with a thermoformed plastic base and lid.
- Blister packs are created under heat using special machines through the form of heat and pressure.
- They have forming, filling, sealing, and cutting stations.
- Good operating practices are a must for blister manufacture.
- Thermoformation is a much faster and cheaper process than making a cold form blister.
Now you know a little more about these all feel-good machines! If you ever need to buy this machine, you can visit our website (your site here).
Thanks for reading!
Reference
1.Akash Gupta*Dr. Nimita Manocha and Dr. Vimukta Sharma1BM College of Pharmaceutical Education and Research, Indore, M.P.SJIF Impact Factor 8.084ISSN 2277– 7105.https://wjpr.s3.ap-south-1.amazonaws.com/article_issue/c90419ffed284cdefa71a12cf881ebcf.pdf
2.GLOBAL JOURNAL OF ENGINEERING SCIENCE AND RESEARCHES TO STUDY VARIOUS MATERIALS,METHODS AND HEAT SEALING PARAMETERS USED IN BLISTER PACKAGING PROCESS Rakesh*1, Vandana2 &Mohit Kumar3.September 2018] ISSN 2348 – 8034 DOI- 10.5281/zenodo.1412375 Impact Factor- 5.070.http://www.gjesr.com/Issues%20PDF/Archive-2018/September-2018/14.pdf