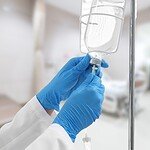
Infusion bag filling machines are inseparable from modern medical care

Grand CEO Bruce Fu Visits Thai Pharma Partners in Thailand
The Science and Applications of Dry Granulation Machines: A Deep Dive into Roll Compactor Machines
Dry granulation machines have become a game changer in many industries, especially in pharmaceuticals, food processing, and chemicals. In this blog post, we explore the principle, function, detailed explanation, and maintenance of dry granulation machines. We focus on the roll compactor machine technology, while incorporating key terms such as roller compactor, roller compactor pharmaceutical, and roller compactor.
1. Understanding the Working Principle
Dry granulation machines operate on a unique and efficient method that uses the inherent crystal water in powders to create granules. The process begins by feeding dry powder materials with certain crystals into a hopper. A pre-compression screw conveys the powder with a uniform density to the pressing rollers. The pressing rollers then apply consistent pressure and shape the powder into compacted sheets. These sheets fall into a crusher where they are broken down into granules. Finally, a screen filters the granules. Only those that meet the preset size range fall into the final container. This process is fully automated, ensuring consistency and high productivity.
Dry Granulation Machines (Experimental)
This system eliminates the need for water, ethanol, or wetting agents. By avoiding the traditional wet granulation steps—wetting, kneading, and drying—the dry granulation process saves time and energy. The core idea behind a roll compactor machine is to use the crystal water already present in the material to create granules in one smooth, continuous process[1].
2. Key Benefits and Applications
2.1 Core Benefits
Dry granulation machines offer several benefits:
Efficiency: They convert powders into granules directly, cutting out extra steps found in wet granulation.
Uniformity: The pre-compression and pressing process ensures granules have high density and consistent weight.
Environmental Friendliness: No extra solvents or additives mean reduced chemical use and lower environmental impact.
Cost-Effective Production: Fewer processing steps reduce overall production costs and energy consumption.
2.2 Industrial Applications
These machines have a wide range of applications. In the pharmaceutical industry, a roller compactor pharmaceutical system is critical for ensuring batch-to-batch consistency. It is especially useful for producing small batches in research labs as well as large-scale production in manufacturing facilities.
In the food and dairy sectors, the machine helps produce granulated products that require precise control over size and density. The chemical industry also benefits from its ability to handle viscous and heat-sensitive materials that are hard to process using traditional methods.
Companies looking to purchase a roller compactor for sale can find systems designed to meet varying production capacities and specifications. Whether you need a small experimental unit or a full-scale industrial machine, the versatility of these systems makes them an attractive choice.
Solid dosage form process flow chart
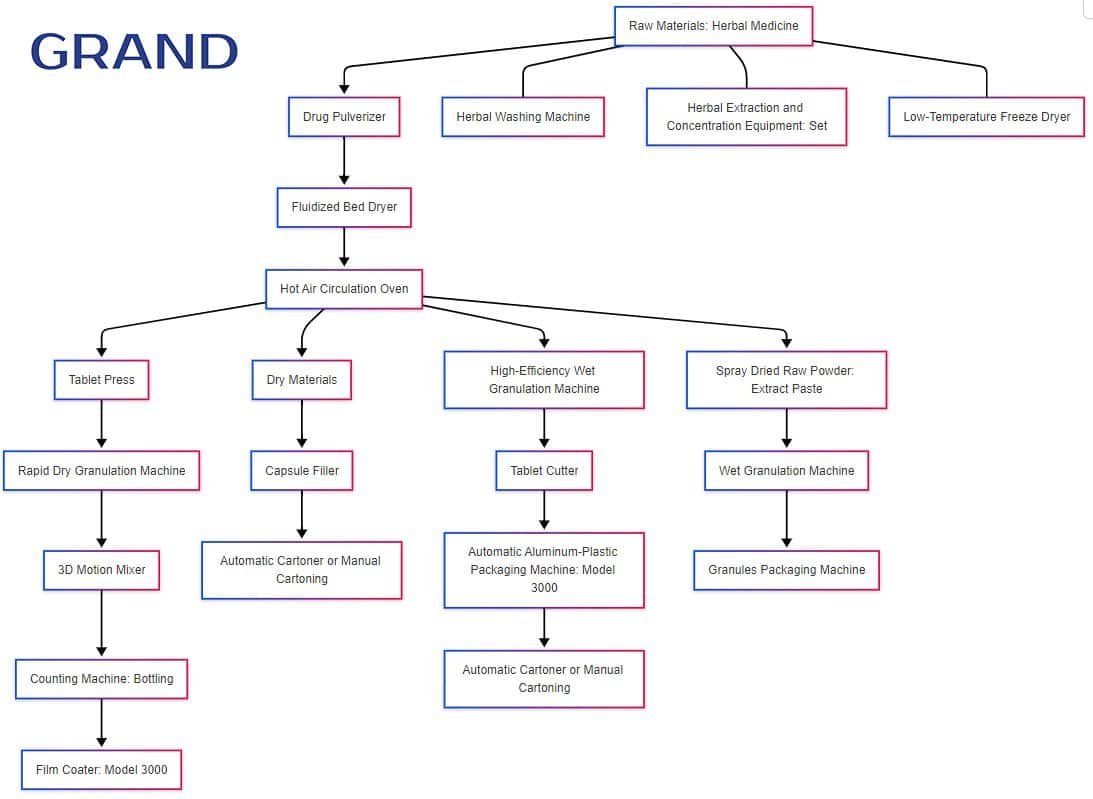
3. Detailed Technical Explanation
3.1 The Pre-Compression and Extrusion Process
The heart of a roll compactor machine is its ability to pre-compress dry powders. The machine uses a pre-compression screw that moves the powder towards the pressing rollers. When the material reaches the rollers, it is compacted into a dense sheet. This sheet then falls into a crusher, where it is broken down into granules of a specified size range. The process is controlled and monitored by a PLC (Programmable Logic Controller) system. This ensures that all parameters—such as pressing pressure, roller speed, and feeding speed—are maintained within tight tolerances.
Dry granulation machines internal details
The technology behind pre-compression is vital. By applying consistent pressure, the granules produced have uniform weight and density. This consistency is crucial in industries like pharmaceuticals, where precise dosing and uniformity can affect the safety and efficacy of the final product[2].
Highly efficient dry granulation machines
3.2 Automation and Control
Modern dry granulation machines come with advanced automation features. A PLC-based human-machine interface displays real-time data and process parameters. Operators can easily adjust settings like roller speed and feeding rate. The system also records production data, which can be printed or exported for quality control and traceability purposes.
Internal structure of efficient dry granulation machines
Automated control is a key selling point for the roller compactor. It not only reduces the need for manual intervention but also enhances safety and compliance with industry standards such as FDA and cGMP. This is especially important in pharmaceutical applications, where regulatory requirements are stringent.
3.3 Compact Design and Energy Efficiency
The design of dry granulation machines is compact and efficient. The compact footprint means that these machines take up minimal space, making them ideal for laboratories and production floors with limited room. Their design also facilitates easy mobility and installation.
Energy efficiency is another significant advantage. Since the process does not require additional solvents or extensive drying, energy consumption is kept to a minimum. Lower energy use translates directly into reduced operational costs, making these machines an attractive option for companies looking to enhance their bottom line[3].
4. Maintenance and Upkeep
Maintaining a dry granulation machine is critical for ensuring long-term performance and consistent product quality. Here are some essential tips for upkeep:
4.1 Regular Cleaning and Inspection
After each production run, it is important to clean the hopper, rollers, screens, and other key components. In industries like pharmaceuticals, cleanliness directly impacts product quality. Regular cleaning helps prevent material buildup, which could lead to blockages or wear. A daily cleaning routine, followed by periodic detailed inspections, is recommended[4].
4.2 Lubrication and Mechanical Checks
Despite the dry processing method, mechanical components such as shafts, gears, and bearings still experience friction. Regular lubrication of these parts is essential to prevent premature wear and ensure smooth operation. Following the manufacturer's guidelines for lubrication intervals can extend the machine’s service life.
4.3 Automation System Maintenance
The PLC control system is the brain of the machine. It is important to monitor the system regularly to ensure sensors and control modules are functioning properly. Any malfunction should be addressed immediately by qualified technical personnel. Keeping a log of all maintenance activities can help in diagnosing future issues and planning preventive measures.
4.4 Calibration and Upgrades
Over time, calibration drift can occur in any automated system. Regular calibration checks ensure that all parameters remain accurate. Upgrading the software and hardware components of the system, when needed, can also enhance performance and maintain compliance with evolving industry standards.
5. Future Trends and Market Outlook
The demand for roll compactor machine technology is on the rise. As industries increasingly adopt automated and energy-efficient processes, dry granulation systems are gaining more popularity. Manufacturers are continuously innovating to produce more compact, efficient, and versatile machines.
Academic research supports the evolution of this technology. Studies have shown that the pre-compression process improves granule uniformity and stability, which is particularly important for pharmaceuticals[5]. These advancements not only improve product quality but also open new avenues for processing materials that were previously challenging to handle.
Furthermore, market trends indicate a growing preference for roller compactor for sale products that offer customizable production capacities. This flexibility allows companies to tailor machines to their specific needs, whether for small-scale laboratory experiments or full-scale industrial production.
6. Conclusion
Dry granulation machines represent a significant shift from traditional wet granulation methods. The roll compactor machine leverages the natural crystal water in dry powders to create high-density, uniform granules in a single, continuous process. This method is efficient, environmentally friendly, and cost-effective.
Key advantages include the elimination of extra processing steps, compact design, high automation, and energy efficiency. With applications across pharmaceuticals, food processing, and chemicals, these machines are set to play a crucial role in modern manufacturing. Their ability to produce consistent granules meets the stringent quality demands of the pharmaceutical industry, making them indispensable for companies aiming for precision and reliability.
The robust automation and control systems ensure that operators can monitor and adjust the process in real-time, maintaining high production standards. Regular maintenance, including cleaning, lubrication, and system calibration, is essential to preserve the machine’s performance and longevity.
In summary, the dry granulation machine is not just a piece of equipment—it is a vital tool for achieving production excellence. For businesses looking to invest in a roller compactor or search for a reliable roller compactor for sale, the benefits are clear: enhanced efficiency, lower costs, and superior product quality. As technology advances, we expect further innovations that will continue to revolutionize dry granulation processes and expand their applications in various industries.
References
[1].Research on the use of pre-compression techniques in pharmaceutical processing, published in the Pharmaceutical Engineering journal.
[2].A study on granule uniformity and density in dry granulation, featured in Food Science publications.
[3].Design principles of energy-efficient granulation equipment discussed in Mechanical Design magazines.
[4].Guidelines for cleaning and maintenance in pharmaceutical manufacturing standards.
[5].Latest technological developments in roll compactor machines, as referenced in academic papers available on Google Scholar¹.
This detailed exploration of dry granulation machines highlights how the roll compactor machine works, its benefits, applications, and essential maintenance practices. If you are considering investing in this technology, the information provided here should serve as a solid foundation for your decision-making process.