
Do Gummy Vitamins Really Work?
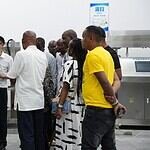
Kenyan Delegation Visits Grand Company-Company News
Capping Machines: Types, Applications and Efficiency, the Most Complete Guide
Summary
Modern manufacturing relies on precise, high‑speed equipment to keep pace with market demand. At the heart of many bottling and packaging operations lies the cap filling machine, an indispensable element of advanced capping systems and a seamless capping line. Whether you’re in beverages, pharmaceuticals, cosmetics, or chemicals, understanding the roles, varieties, and benefits of capping machines can transform your production efficiency and product quality.

1. What Is a Capping Machine and Why You Need a Cap Filling Machine
A capping machine automates the placement and tightening of caps, lids, or closures on containers. Often referred to as a “cap filling machine,” it ensures that every bottle, jar, or tube is sealed consistently—crucial for product safety, shelf life, and consumer satisfaction.
Sealing Integrity: Prevents leaks, contamination, and spoilage.
Speed & Throughput: Modern capping systems handle hundreds to thousands of units per minute.
Quality Consistency: Eliminates human error, maintaining torque accuracy and alignment.
Without a reliable cap filling machine in your capping line, manual capping would introduce variability, slow down production, and increase labor costs.
2. Types of Capping Machines
Capping machines come in various designs to match container types, cap styles, and production speeds. Here are the most common categories:
1.Screw Capping Machines
Ideal for threaded caps on plastic, glass, or metal bottles.
Variants include spindle cappers (individual heads) and chuck cappers (grip‑and‑twist mechanisms).
2.Snap Capping Machines
Used for press‑on or snap‑on caps (e.g., dispensing closures on condiment bottles).
Simple push‑down action; high speed for sports‑drink style lids.
3.Press Capping Machines
Apply downward force to seat caps (common in food jars).
Can incorporate torque control to avoid over‑ or under‑tightening.
4.Roller Capping Machines
Utilize rubber or silicone rollers to twist caps as containers pass underneath.
Smooth, continuous motion—excellent for medium to high speeds.
Containers move in a circular turret, passing under multiple capping heads.
Built for ultra‑high throughput (over 600 bottles per minute).
6.Inline Capping Machines
Containers on a straight conveyor are capped in sequence.
Flexible: easy changeovers between container sizes and cap types.
Selecting the right type hinges on cap geometry, container material, desired throughput, and integration needs.
3. What Products Require Capping?
Many industries depend on capping machines to seal products reliably:
Beverages: Water, soft drinks, juices, sports drinks, energy drinks.
Pharmaceuticals: Syrup bottles, supplement vials, medical ointments.
Cosmetics & Personal Care: Lotions, creams, serums, shampoos.
Chemical & Household: Cleaning agents, detergents, automotive fluids.
Food & Condiments: Sauces, jams, oils, dressings.
Any product that uses a bottle or jar closure benefits from automation: consistent torque preserves product integrity, and speed meets market demand.
4. Integrating Capping Machines into Your Capping Line
A modern capping line comprises multiple stations—filling, rinsing, capping, labeling, and packing—all linked by conveyors. Key considerations for integration:
Layout & Footprint: Inline vs. rotary machines affect floor space.
Container Handling: Guide rails, star wheels, and timing screws ensure containers are correctly oriented for capping.
Control Systems: PLCs synchronize filling and capping speeds to avoid jams or gaps.
Changeover Flexibility: Quick‑change tooling supports multiple container sizes with minimal downtime.
Quality Inspection: Torque sensors and vision systems verify cap presence and tightness.
Seamless communication between filling and capping modules reduces bottlenecks and maximizes uptime.
5. Why You Need a Capping Machine
Regulatory Compliance: Many products (especially in pharma and food) require precise seals to meet FDA or ISO standards.
Labor Savings: Automating cap placement frees staff for value‑added tasks and reduces repetitive‑strain injuries.
Waste Reduction: Proper sealing decreases rejects, leaks, and product spoilage.
Brand Reputation: Consistent seals inspire consumer trust—no one wants a leaking bottle.
For any mid‑ to high‑volume operation, a cap filling machine isn’t just a luxury; it’s a necessity.
6. How Capping Machines Improve Efficiency
High Throughput: Modern machines handle from 30 CPM (containers per minute) in small‑scale operations up to 1,200 CPM in large pharmaceutical lines.
Minimal Downtime: Features like quick‑release chucks and tool‑less adjustments support rapid changeovers.
Automated Feedback: Integrated torque and presence sensors immediately flag defects, preventing downstream issues.
Reduced Maintenance: Modular heads and self‑lubricating components lower service intervals.
Scalable Architecture: Add or remove capping heads to match production demands without replacing the entire system.
By automating cap application, you not only raise your line speed but also elevate overall equipment effectiveness (OEE).
7. Spotlight on Grand Capping Machine Features
The Grand capping machine exemplifies next‑level performance and user‑centric design within capping systems:
Innovative Vibratory‑Bowl Lifting Frame: Single‑operator setup—fully adjusted in under five minutes, no footcup repositioning needed.
Space‑Saving Integrated Design: Occupies just 1–2.5 m², with built‑in bottle‑height adjustment—ideal for compact capping lines.
Auto‑Alarm & Shutdown: Inner‑stopper sensor triggers alarms or immediate shutdown if a cap plug is missing, reducing waste.
Uni‑Directional Infeed/Outfeed: Bottles enter and exit in the same direction, guaranteeing jam‑free, stable flow.
Precision Plug‑Positioning: Compensates for minor diameter variances in glass bottles, ensuring perfect cap seating.
Mechanical Anti‑Burst + 4‑Jaw Capping Head: Prevents seal‑bursting from misaligned caps and accommodates the most common cosmetic and pharmaceutical packaging specs.
Integrating a Grand cap filling machine into your capping line elevates throughput, reliability, and quality control—all while minimizing floorspace.
Conclusion
Choosing the right capping machine transforms your production—from slow, error‑prone manual capping to lightning‑fast, precise automation. Whether you opt for a rotary, inline, or specialty press cap filling machine, integrating it into a robust capping line gives you the consistency, compliance, and capacity today’s markets demand.
For manufacturers seeking top‑tier performance, the Grand capping machine delivers a compact footprint, rapid changeovers, and advanced safety features—making it an ideal centerpiece of any modern capping system.