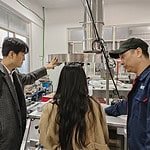
3 Tempat dan 8 Langkah untuk Mengimpor Mesin Pengemas Blister dari Tiongkok
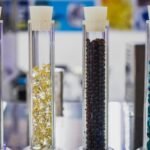
Mesin Pembuat Kapsul Gel Lunak: Jenis, Prinsip Kerja, Aplikasi dan Tips Membeli
Granulator dalam Industri Farmasi – Tinjauan Komprehensif
Manufaktur farmasi merupakan industri yang kompleks. Jika Anda berencana untuk terjun ke dunia manufaktur farmasi, Anda akan berhadapan dengan banyak mesin yang kompleks. Mesin Granulator adalah contoh sempurna bagi mereka.
Peran granulator adalah mengubah bubuk atau material partikulat halus menjadi butiran yang seragam dan mengalir bebas. Proses ini penting untuk menciptakan produk farmasi dengan kualitas yang konsisten. Granulator juga akan menawarkan kemudahan pemrosesan yang lebih baik dan penghantaran obat yang optimal. Baca terus dan mari pelajari lebih lanjut tentang granulator secara mendetail.
Apa itu Granulator? 
Granulator adalah peralatan khusus yang digunakan dalam industri farmasi, kimia, dan lainnya. Granulator dapat mengubah bahan bubuk atau halus menjadi butiran. Dengan kata lain, alat yang sangat diperlukan ini dapat mengubah bahan mentah menjadi bentuk yang lebih mudah ditangani. Oleh karena itu, granulator memainkan peran utama dalam pembuatan produk obat.
Apa itu Granulasi dalam Farmasi?
Granulasi adalah teknik yang mengubah partikel halus menjadi butiran. Dengan kata lain, teknik ini mengubah partikel seperti bubuk menjadi struktur yang lebih stabil. Transformasi ini bukan sekadar proses mekanis. Proses ini dapat meningkatkan kualitas, stabilitas, dan kinerja formulasi farmasi.
Apa Tujuan Granulator?
Ada banyak alasan untuk menggunakan granulator dalam industri farmasi. Berikut adalah alasan utamanya:
- Meningkatkan Kemampuan Aliran
Granulator mampu mengubah serbuk halus dan kohesif menjadi butiran yang mengalir bebas. Butiran ini mudah ditangani dan diproses pada tahap produksi. Produsen farmasi dapat dengan mudah memproses butiran selama pembuatan tablet dan pengisian kapsul.
- Meningkatkan Kompresibilitas
Granul memiliki kemampuan kompresibilitas yang lebih baik daripada serbuk halus. Hal ini penting saat membuat tablet yang seragam dan kuat dengan kandungan obat yang konsisten. Hal ini membantu perusahaan farmasi untuk meningkatkan kualitas obat mereka.
- Distribusi Obat yang Seragam
Proses granulasi dapat memastikan distribusi Bahan Farmasi Aktif (API) yang lebih merata. Hal ini dapat membantu memastikan dosis obat yang konsisten setiap saat.
- Mengurangi Debu
Proses mengubah serbuk halus menjadi butiran besar dapat meminimalkan timbulnya debu. Hal ini pada akhirnya dapat meningkatkan keselamatan di tempat kerja. Selain itu, hal ini juga dapat membantu mengurangi kehilangan produk.
- Mengontrol Rilis
Teknik granulasi khusus juga dapat digunakan untuk mengendalikan formulasi pelepasan obat. Teknik ini membantu produsen farmasi membuat obat sesuai dengan rekomendasi.
Apa Proses Granulasi dalam Industri Farmasi?
Sebelum membeli granulator, penting untuk mengetahui seperti apa proses granulasi. Berikut ini gambaran keseluruhan prosesnya.
Langkah 1 – Persiapan Bahan Baku
Langkah pertama adalah menganalisis secara menyeluruh semua sifat fisik dan kimia bahan baku. Ini membantu memastikan bahwa semua bahan memenuhi spesifikasi kualitas dan kemurnian. Selain itu, ini juga melibatkan evaluasi distribusi ukuran partikel awal bubuk. Selain itu, proses ini mungkin melibatkan pengukuran dan pengendalian kadar air bahan.
Langkah 2 – Pencampuran dan Pengadukan
Langkah kedua adalah menggabungkan semua bahan kering. Ini termasuk bahan farmasi dan eksipien. Selama proses pencampuran, penting untuk memastikan distribusi semua komponen yang merata. Produsen farmasi dapat menggunakan V-blender, planetary mixer, dan high-shear mixer untuk pencampuran.
Saat mencampur bahan-bahan, penting juga untuk memastikan pengoptimalan waktu. Ini akan membantu menghasilkan campuran yang sempurna.
Langkah 3 – Granulasi
Metode Granulasi Basah
Ini adalah proses yang paling umum. Proses ini dimulai dengan persiapan binder, yang melibatkan pembuatan larutan binder cair. Kemudian, produsen secara bertahap menambahkan larutan binder ke dalam campuran bubuk. Larutan ini akan membantu pembuatan gugusan granul awal melalui pencampuran mekanis. Kontrol kelembapan sangat penting selama proses ini. Kontrol kelembapan akan memastikan formulasi granul yang tepat.
Metode Granulasi Kering
Metode granulasi kering dimulai dengan memberikan tekanan tinggi untuk memadatkan campuran serbuk. Kemudian, produsen akan membuat massa padat atau pita. Setelah itu, mereka akan memecah massa padat tersebut menjadi butiran. Proses penyaringan akan memastikan ukuran butiran yang seragam di akhir proses.
Langkah 4 – Pengeringan
Proses ini melibatkan penghilangan kelebihan air dari butiran. Ada tiga teknik pengeringan utama yang diikuti oleh produsen farmasi. Teknik-teknik tersebut meliputi:
- Pengeringan tempat tidur fluida
- Pengeringan baki
- Pengeringan vakum
Selama proses pengeringan, sangat penting untuk menjaga suhu yang tepat. Hal ini dapat mencegah degradasi material. Selama proses ini, penting juga untuk memastikan bahwa tingkat kelembapan akhir memenuhi spesifikasi.
Langkah 5 – Pengukuran dan Penyaringan
Proses pengurangan ukuran akan memecah potongan-potongan granul yang lebih besar menjadi ukuran yang seragam. Kemudian, produsen akan menggunakan saringan mekanis atau penggilingan untuk penyaringan. Langkah selanjutnya adalah memastikan klasifikasi ukuran. Di sinilah mereka memisahkan granul menjadi partikel yang diinginkan dengan rentang ukuran yang sesuai. Kemudian, debu dan granul berukuran besar lainnya dapat dihilangkan.
Langkah 6 – Pelumasan
Langkah selanjutnya adalah menambahkan bahan pelumas yang tepat. Selain itu, pelapisan yang seragam juga penting. Untuk mencegah lengket, produsen akan mengurangi gesekan selama langkah pemrosesan berikutnya. Selain itu, mereka juga akan meningkatkan pergerakan dan kompresibilitas butiran.
Langkah 7 – Kontrol Kualitas
Selama kontrol kualitas, pengujian fisik dan analisis kimia akan dilakukan. Pengujian fisik adalah tentang mengevaluasi sifat-sifat butiran. Ini termasuk ukuran partikel, kerapatan massa, dan kadar air. Di sisi lain, analisis kimia akan memastikan keseragaman bahan aktif.
Langkah 8 – Pengemasan dan Penyimpanan
Penting untuk menggunakan wadah yang tepat untuk pengemasan. Kemasan penghalang kelembapan memainkan peran utama di sini. Setelah pengemasan, butiran memerlukan penyimpanan yang tepat dalam kondisi tertentu.
5 Jenis Granulator Farmasi yang Umum
Ada banyak jenis granulator yang tersedia untuk dibeli. Penting bagi Anda untuk membuat pilihan yang tepat saat membeli satu. Berikut adalah 5 jenis granulator yang paling umum tersedia:
Granulator Osilasi
Granulator ini dilengkapi dengan rotor berosilasi. Rotor ini bergerak maju mundur selama proses granulasi. Serbuk harus melewati kasa atau saringan yang berayun untuk menghasilkan partikel dengan ukuran yang diinginkan. Ukuran granul akan bervariasi berdasarkan ukuran lubang yang tersedia pada saringan. Anda dapat menyesuaikan ukuran ini dengan saringan sesuai dengan kebutuhan Anda. Selain itu, Anda juga dapat menyesuaikan kecepatan putar sesuai dengan sifat material Anda.
Anda dapat menggunakan granulator osilasi untuk memproses:
- Bedak yang sensitif terhadap kelembapan
- Bahan tambahan makanan
Granulator Pemadat Rol
Mesin ini menggunakan teknik granulasi kering. Anda dapat menggunakannya untuk mengubah bubuk menjadi granulator tanpa menggunakan cairan apa pun. Di dalam granulator, Anda akan melihat dua rol yang berputar berlawanan arah. Setelah menuangkan bubuk, rol akan memadat di antara dua lembar pita. Kemudian, rol akan memecah lembaran padat menjadi butiran.
Anda dapat menggunakan granulator pemadat rol untuk memproses:
- Bedak yang sensitif terhadap kelembapan
- Bubuk peka panas
Granulator Geser Tinggi
Ini adalah granulator berkecepatan tinggi yang tersedia. Dengan kata lain, granulator ini dapat mencampur serbuk dengan kecepatan tinggi saat membentuk butiran. Hasilnya, Anda dapat merasakan tingkat efisiensi yang lebih tinggi dari granulator ini. Selain itu, gaya mekanis yang kuat dalam granulator ini memastikan pencampuran yang menyeluruh. Anda dapat memastikan konsistensi baik dalam kepadatan maupun ukuran granulator ini.
Granulator Getar
Granulator getar sangat ideal untuk menyelesaikan proses granulasi. Granulator ini sangat mirip dengan granulator dengan fungsi osilasi. Namun, granulator ini tidak memutar partikel untuk memecahnya. Sebaliknya, proses ini terjadi melalui proses getaran. Proses ini memastikan pemecahan granul yang tepat hingga ukuran yang diinginkan.
Granulator getar ideal untuk:
- Bubuk peka panas
- Bedak yang sensitif terhadap kelembapan
Granulator Tempat Tidur Cairan
A Granulator Tempat Tidur Cairan akan menangguhkan serbuk pemrosesan melalui uap udara yang mengalir ke atas. Kemudian akan tercipta keadaan cair. Ini adalah tahap di mana partikel akan berperilaku mirip dengan cairan. Hasilnya, Anda dapat memastikan distribusi kelembapan dan panas yang merata. Kemudian larutan pengikat masuk ke dalam cairan dan saling menempel untuk menciptakan butiran.
Bagaimana Cara Memilih Granulator yang Hebat?
Bagaimana Anda dapat memilih granulator terbaik yang sesuai dengan tujuan Anda? Ingatlah kiat-kiat berikut ini:
- Kebutuhan produksi
Pahami produk farmasi apa yang perlu Anda produksi sebelum membeli granulator. Misalnya, Anda harus mendapatkan granulator lembaran untuk memproduksi butiran tablet. Granulator yang Anda dapatkan harus mampu menangani semua ukuran masukan dan keluaran Anda.
- Faktor operasional
Perhatikan juga kemudahan perawatan, tingkat kebisingan, dan konsumsi daya granulator. Ini akan membantu Anda menjalankan granulator secara efisien.
- Sifat material
Anda harus membeli granulator yang tepat berdasarkan bahan yang Anda gunakan. Di sinilah Anda harus fokus pada kekerasan, fluiditas, kadar air, dan kerapuhan bahan yang Anda gunakan. Misalnya, jika bahan tersebut sensitif terhadap kelembaban, Anda harus membeli granulator kering.
Dapatkan Granulator Berkualitas Tinggi dengan Grand Pack
Sekarang Anda sudah memiliki gambaran yang jelas tentang apa itu granulator. Dengan mengikuti tips yang kami bagikan, Anda dapat melanjutkan untuk mendapatkan granulator yang tepat. Namun, Anda perlu membelinya dari tempat yang dapat Anda percaya. Di situlah Paket Besar dapat membantu Anda. Jangan ragu untuk melihat-lihat granulator yang kami miliki di Grand Pack dan dapatkan granulator Anda. Jika Anda memiliki pertanyaan, jangan ragu untuk menghubungi tim.