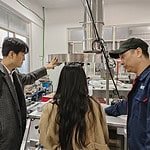
3 lugares y 8 pasos para importar máquinas empacadoras blíster desde China
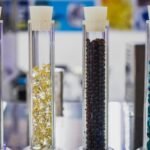
Máquina para fabricar cápsulas de gel blando: tipos, principios de funcionamiento, aplicaciones y consejos para comprar
Granuladores en la industria farmacéutica: una descripción general completa
La fabricación de productos farmacéuticos es una industria compleja. Si planea ingresar al mundo de la fabricación de productos farmacéuticos, tendrá que lidiar con muchas maquinarias complejas. Granuladores Son un ejemplo perfecto para ellos.
La función de un granulador es transformar materiales en polvo o partículas finas en gránulos uniformes y de flujo libre. Este proceso es esencial para crear productos farmacéuticos con una calidad constante. También ofrecerán una mejor procesabilidad y una administración óptima del fármaco. Siga leyendo y conozcamos más sobre los granuladores en detalle.
¿Qué es un granulador? 
Un granulador es un equipo especial que se utiliza en Industrias farmacéutica, química y otrasPuede convertir materiales en polvo o finos en gránulos. En otras palabras, esta herramienta indispensable puede transformar las materias primas en una forma que sea más fácil de manipular. Por lo tanto, los granuladores desempeñan un papel importante en la fabricación de productos farmacéuticos.
¿Qué es la granulación en productos farmacéuticos?
La granulación es la técnica que convierte las partículas finas en gránulos. En otras palabras, convierte las partículas en forma de polvo en una estructura más estable. Esta transformación no es solo un proceso mecánico. Puede mejorar la calidad, la estabilidad y el rendimiento de las formulaciones farmacéuticas.
¿Cuál es el propósito de un granulador?
Existen numerosas razones para utilizar un granulador en la industria farmacéutica. Estas son las principales:
- Mejorando la fluidez
Los granuladores son capaces de convertir polvos finos y cohesivos en gránulos que fluyen libremente. Estos gránulos son fáciles de manipular y procesar en las etapas de fabricación. Los fabricantes farmacéuticos pueden procesar fácilmente los gránulos durante la preparación de comprimidos y el llenado de cápsulas.
- Mejorando la compresibilidad
Los gránulos tienen una mejor compresibilidad que los polvos finos. Esto es importante para crear comprimidos uniformes y resistentes con un contenido de fármaco constante. Ayuda a las empresas farmacéuticas a mejorar la calidad de sus medicamentos.
- Distribución uniforme de medicamentos
El proceso de granulación puede garantizar una distribución más uniforme de los ingredientes farmacéuticos activos (API), lo que puede ayudar a garantizar una dosificación constante del medicamento en todo momento.
- Reducción del polvo
El proceso de convertir polvos finos en gránulos grandes puede minimizar la generación de polvo, lo que puede mejorar la seguridad en el lugar de trabajo y, además, ayudar a reducir la pérdida de producto.
- Control de liberación
También es posible utilizar técnicas de granulación específicas para controlar la liberación de fármacos, lo que ayuda a los fabricantes farmacéuticos a elaborar medicamentos de acuerdo con las recomendaciones.
¿Qué es el proceso de granulación en la industria farmacéutica?
Antes de comprar un granulador, es importante saber cómo es el proceso de granulación. A continuación, se ofrece una descripción general de todo el proceso.
Paso 1 – Preparación de las materias primas
El primer paso es analizar en profundidad todas las propiedades físicas y químicas de las materias primas. Esto ayuda a garantizar que todos los ingredientes cumplan con las especificaciones de calidad y pureza. Además, implica evaluar también la distribución inicial del tamaño de las partículas de los polvos. Además, este proceso puede implicar la medición y el control de los niveles de humedad de los ingredientes.
Paso 2 – Mezclar y combinar
El segundo paso es combinar todos los ingredientes secos, incluidos los ingredientes farmacéuticos y los excipientes. Durante el proceso de mezclado, es importante garantizar una distribución uniforme de todos los componentes. Los fabricantes farmacéuticos pueden utilizar mezcladores en V, mezcladores planetarios y mezcladores de alto cizallamiento para mezclar.
A la hora de mezclar los ingredientes también es importante optimizar el tiempo, ya que esto ayudará a que la mezcla quede perfecta.
Paso 3 – Granulación
Método de granulación húmeda
Este es el proceso más común. Comienza con la preparación del aglutinante, que implica crear la solución aglutinante líquida. Luego, los fabricantes agregan gradualmente la solución aglutinante a la mezcla de polvo. Esto ayudará a crear los grupos de gránulos iniciales mediante la mezcla mecánica. El control de la humedad es esencial durante todo este proceso. Esto garantizará la formulación adecuada de los gránulos.
Método de granulación en seco
El método de granulación en seco comienza con la aplicación de alta presión para comprimir la mezcla de polvo. Luego, los fabricantes crearán masas sólidas o cintas. Después, romperán las masas comprimidas en gránulos. El proceso de cribado garantizará un tamaño de gránulo uniforme al final del proceso.
Paso 4 – Secado
Este proceso implica eliminar el exceso de humedad de los gránulos. Existen tres técnicas principales de secado que siguen los fabricantes farmacéuticos, que son las siguientes:
- Secado en lecho fluido
- Secado en bandeja
- Secado al vacío
Durante todo el proceso de secado, es esencial mantener una temperatura precisa, ya que esto puede evitar la degradación del material. Durante este proceso, también es importante garantizar que el nivel de humedad final cumpla con las especificaciones.
Paso 5 – Dimensionamiento y selección
El proceso de reducción de tamaño descompondrá los trozos más grandes de gránulos en tamaños uniformes. Luego, los fabricantes utilizarán tamices mecánicos o molinos para el tamizado. El siguiente paso es asegurar la clasificación por tamaño. Aquí es donde separan los gránulos en partículas deseadas con rangos de tamaño apropiados. Luego es posible eliminar el polvo y otros gránulos de gran tamaño.
Paso 6 – Lubricación
El siguiente paso es incorporar los agentes lubricantes adecuados. Además, también es esencial que el recubrimiento sea uniforme. Para evitar que se peguen, los fabricantes reducirán la fricción durante los pasos de procesamiento posteriores. Además, también mejorarán el movimiento y la compresibilidad de los gránulos.
Paso 7 – Control de calidad
Durante el control de calidad, se realizarán pruebas físicas y análisis químicos. Las pruebas físicas tienen como objetivo evaluar las propiedades de los gránulos, que incluyen el tamaño de las partículas, la densidad aparente y el contenido de humedad. Por otro lado, el análisis químico confirmará la uniformidad de los ingredientes activos.
Paso 8 – Embalaje y almacenamiento
Es importante utilizar envases adecuados para el envasado. En este sentido, los envases con barrera de humedad desempeñan un papel fundamental. Una vez envasados, los gránulos deben almacenarse adecuadamente en condiciones específicas.
5 tipos comunes de granuladores farmacéuticos
Hay muchos tipos diferentes de granuladores disponibles para comprar. Es importante que elijas el adecuado al momento de adquirir uno. A continuación, se muestran 5 de los tipos de granuladores más comunes disponibles:
Granuladores oscilantes
Estos granuladores cuentan con un rotor oscilante que se mueve hacia adelante y hacia atrás durante el proceso de granulación. El polvo debe pasar a través de la malla o tamiz que oscila para crear partículas del tamaño deseado. El tamaño de los gránulos variará según el tamaño de los orificios disponibles en el tamiz. Es posible ajustar este tamaño al tamiz según sus necesidades. Además, también puede ajustar la velocidad de rotación según las propiedades del material.
Puede utilizar un granulador oscilante para procesar:
- Polvos sensibles a la humedad
- Aditivos alimentarios
Compactador de rodillos Granulador
Estas máquinas siguen la técnica de granulación en seco. Puede utilizarlas para convertir polvos en granuladores sin utilizar ningún líquido. Dentro del granulador, verá dos rodillos contrarrotativos diferentes. Después de verter el polvo, se comprimirá entre dos láminas de cinta. Luego, descompondrá la lámina compacta en gránulos.
Puede utilizar un granulador compactador de rodillos para procesar:
- Polvos sensibles a la humedad
- Polvos sensibles al calor
Granulador de alto cizallamiento
Se trata de granuladores de alta velocidad. En otras palabras, estos granuladores pueden mezclar polvos a alta velocidad al formar gránulos. Como resultado, puede experimentar un mayor nivel de eficiencia con ellos. Además, las intensas fuerzas mecánicas en estos granuladores garantizan una mezcla completa. Puede garantizar la consistencia tanto en la densidad como en el tamaño de estos granuladores.
Granulador vibratorio
Los granuladores vibratorios son ideales para completar el proceso de granulado. Son bastante similares a los granuladores con función oscilante. Sin embargo, no hacen girar las partículas para descomponerlas, sino que lo hacen mediante un proceso de vibración. Esto garantiza una descomposición precisa de los gránulos en los tamaños deseados.
Un granulador vibratorio es ideal para:
- Polvos sensibles al calor
- Polvos sensibles a la humedad
Granulador de lecho fluido
A Granulador de lecho fluido El proceso suspenderá los polvos a través de un vapor de aire que fluye hacia arriba. Luego creará un estado fluido. Esta es una etapa en la que las partículas se comportarían de manera similar a un fluido. Como resultado, puede garantizar una distribución uniforme de la humedad y el calor. Luego, la solución aglutinante entra en los fluidos y se adhiere para crear gránulos.
¿Cómo elegir un buen granulador?
¿Cómo puede elegir el mejor granulador que se adapte a sus necesidades? Tenga en cuenta los siguientes consejos:
- Necesidades de producción
Antes de comprar el granulador, debe comprender qué productos farmacéuticos necesita producir. Por ejemplo, debe adquirir un granulador de láminas para producir gránulos de comprimidos. El granulador que adquiera debe poder manejar también todos los tamaños de entrada y salida.
- Factores operacionales
Preste atención también a la facilidad de mantenimiento, el nivel de ruido y el consumo de energía del granulador. Esto le ayudará a que el granulador funcione de manera eficiente.
- Propiedades del material
Debes comprar el granulador adecuado en función de los materiales con los que trabajes. En este sentido, debes prestar atención a la dureza, la fluidez, el contenido de humedad y la fragilidad de los materiales con los que trabajes. Por ejemplo, si los materiales son sensibles a la humedad, debes adquirir un granulador en seco.
Obtenga un granulador de máxima calidad con Grand Pack
Ahora tienes una idea clara de qué son los granuladores. Si sigues los consejos que compartimos, puedes proceder a conseguir el granulador adecuado. Sin embargo, debes comprarlo en un lugar en el que puedas confiar. Ahí es donde Gran paquete Podemos ayudarle. No dude en consultar los granuladores que tenemos en Grand Pack y obtener el suyo. Si tiene alguna pregunta, no dude en ponerse en contacto con el equipo.