
4 Types of Veterinary Medicine Formulations: Which One Suits Your Needs?
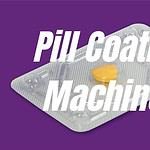
3 Critical Roles of Pill Coating Machines in Medical Research
How high-speed tablet machine revolutionize production?
In today’s fast-paced manufacturing landscape, efficiency and precision are paramount. High-speed tablet machines, also known as advanced pill presser or pill maker machines, have transformed the way industries produce tablets—whether for pharmaceuticals, nutraceuticals, or chemicals. As a cornerstone of modern production lines, these tablet machines combine cutting-edge engineering with the robust reliability of Chinese manufacturing, ensuring that every tablet is uniform in quality and consistency.
What Is a Tablet Machine?
At its core, a tablet machine compresses granular or powdered materials into solid tablets. There are two main types:
Single Punch Tablet Machine: This design uses a single punch mechanism that moves vertically to compress materials into tablets. Although suitable for small-batch or trial production (approximately 60–100 tablets per minute), the uneven force distribution can lead to density variations and issues like cracking.
Rotary Tablet Machine: Featuring multiple punches arranged around a rotating turret, these machines apply continuous, uniform pressure. The rotary design is the foundation for high-speed tablet machines and has become the industry standard for mass production.
High-speed versions of these machines maintain a minimum peripheral speed of 60 m/min, ensuring rapid and efficient production. Whether you refer to it as a pill machine or a pill presser, the principles remain the same: applying consistent, controlled force to produce high-quality tablets.
The Mechanics Behind High-Speed Tablet Machines
High-speed tablet machines incorporate several key components that work in harmony to produce tablets efficiently:
1. Rotating Turret and Punch Set
Press punches
The heart of the machine is the rotating turret. As it rotates, each set of punches passes sequentially through various stations:
- Filling Station: Powdered material is loaded into die cavities.
- Pre-Compression Station: A light pressure is applied to expel air from the material, ensuring uniform density.
- Main Compression Station: A hydraulic system applies the final, high-pressure force.
- Ejection Station: Finished tablets are ejected from the die.
2. Forced Feeding Mechanism
The forced feeding system, is critical in ensuring that each die cavity receives a consistent amount of material. This system employs an electric motor coupled with a worm gear reducer and a series of impellers to evenly distribute the powder. By maintaining a steady feed, the machine minimizes air pockets that could otherwise compromise tablet quality.
3. Pre-Compression and Main Compression
The pre-compression phase is essential. It serves two purposes:
- Air Expulsion: By applying initial pressure, it forces air out of the die cavity.
- Material Cohesion: It improves the compactibility of the material, setting the stage for the main compression.
In the main compression phase, hydraulic systems provide the bulk of the pressure. Using principles from classical physics, the tablet’s hardness (H) can be expressed as:
H ∝ F / A
where F is the applied force and A is the die area. This formula illustrates an axiom of tablet production: uniform pressure distribution is key to achieving consistent tablet density.
4. Lubrication and Hydraulic Systems
Lubrication Systems
To maintain smooth operation, high-speed tablet machines integrate advanced lubrication systems. Two types are typically employed:
- Oil Lubrication System: Utilizing an electric pump, oil is delivered at a set pressure (around 2.5 MPa) to critical contact points, reducing friction and wear.
- Dry Lubrication System: Involves a manual pump that applies high-temperature lubricant to moving parts, ensuring clean and effective lubrication.
In addition, a sophisticated hydraulic system controls both the pre-compression and main compression phases. This system includes pressure sensors, a hydraulic pump station, and safety valves that ensure the pressure does not exceed preset limits (typically around 8 MPa). The integrated design not only safeguards the machine but also guarantees that every tablet meets stringent quality standards.
Key Features and Advantages
High-speed tablet machines boast a range of advantages that make them indispensable in modern manufacturing:
Consistent Quality
By utilizing both pre-compression and main compression stages, these machines ensure that each tablet has uniform density and hardness. The controlled environment reduces the likelihood of defects such as cracking or uneven weight distribution.
High Efficiency
With speeds exceeding 60 m/min, high-speed tablet machines can produce thousands of tablets per hour. This rapid production rate is vital for meeting large-scale production demands while maintaining cost-effectiveness.
Advanced Automation
Modern tablet machines feature fully automated processes, including automatic reject systems for defective tablets. Integrated sensors and control systems monitor every stage of production, enabling real-time adjustments to ensure optimal performance.
Chinese Manufacturing Excellence
One of the standout benefits of these machines is their origin. Made in China signifies not only competitive pricing but also adherence to rigorous quality control standards. Chinese manufacturers have mastered the art of producing durable, high-performance equipment that meets global GMP standards.
Technical Innovations in Tablet Machines
High-speed tablet machines incorporate several technical innovations that set them apart:
Forced Feeding System
The forced feeding mechanism guarantees that each die cavity receives a consistent dose of material. This system mitigates the risk of air entrapment—a common issue that can lead to non-uniform tablet density. By using synchronized motors and precise gear systems, manufacturers can achieve unparalleled dosing accuracy.
Dual-Stage Compression
The dual-stage compression process, consisting of pre-compression followed by main compression, is a testament to the machine’s sophistication. Pre-compression removes excess air and begins the binding process, while main compression delivers the final force needed to form a solid tablet. This two-step process is crucial for achieving the desired tablet hardness and uniformity.
Integrated Lubrication Systems
The dual lubrication systems (oil and dry) ensure that every moving part operates smoothly. For example, the oil lubrication system delivers oil through a network of channels and injectors, minimizing friction. This attention to detail not only enhances the machine's longevity but also contributes to consistent tablet quality.
Hydraulic and Pneumatic Controls
The combination of hydraulic and pneumatic systems allows for precise control of pressure and tablet ejection. The hydraulic system’s use of accumulators, pressure sensors, and valves ensures that the applied pressure is both consistent and adjustable. This flexibility is essential for producing tablets with varying compositions and sizes.
Mathematical Foundations and Production Axioms
The operation of high-speed tablet machines can be underpinned by fundamental mathematical formulas. As mentioned earlier, the tablet’s hardness can be approximated by:
H ∝ F / A
This relationship underscores a core production axiom: uniform pressure yields uniform tablets. When the applied force (F) is consistent across all dies, and the die area (A) remains constant, the resulting tablets will exhibit uniform density and strength.
Additionally, the equation for pressure:
P = F / A
can be rearranged to calculate the necessary force for a desired tablet hardness. For example, if a tablet must reach a specific hardness level and the die area is known, manufacturers can adjust the hydraulic pressure accordingly. These equations are not just theoretical—they are applied daily in the design and operation of pill maker machines.
Applications Across Industries
High-speed tablet machines have versatile applications across multiple sectors:
Pharmaceutical Industry
In pharmaceutical production, these machines serve as efficient pill presser systems. They produce tablets for medications, nutritional supplements, and over-the-counter remedies with precision and consistency, meeting strict regulatory standards.
Food and Nutraceutical Sectors
The food industry also benefits from tablet machines, particularly in the production of compressed food products such as nutritional tablets, candy, and other edible items. The ability to produce uniform, high-quality tablets quickly makes these machines invaluable in large-scale food production.
Chemical and Industrial Applications
Beyond food and pharmaceuticals, tablet machines are used in the chemical industry for producing catalysts, disinfectant tablets, and other specialized products. The high-speed operation and precision control make them ideal for various industrial applications.
Conclusion
High-speed tablet machines represent a significant leap forward in manufacturing technology. They combine advanced engineering principles with the unmatched reliability of Chinese manufacturing to deliver efficient, high-quality production solutions. Whether you refer to them as a tablet machine, pill presser, pill maker machine, or simply a pill machine, these devices are at the forefront of modern production technology.
By incorporating dual-stage compression, forced feeding systems, integrated lubrication, and precise hydraulic controls, these machines set a high standard for tablet production. The mathematical foundations, such as the relationship P = F / A, provide a clear rationale for their design and operation. Moreover, the consistent quality, high efficiency, and automation offered by these systems ensure they remain indispensable in the pharmaceutical, food, and chemical industries.
In an era where manufacturing demands are continually evolving, investing in a high-speed tablet machine is not just a decision for enhanced productivity—it's a commitment to quality, reliability, and technological innovation. Embrace the power of modern pill presser technology and let the excellence of Chinese manufacturing propel your production capabilities to new heights.