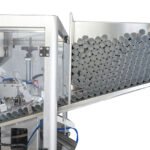
Tüp Dolum Makinelerine İlişkin Kapsamlı Bir Kılavuz

Dünyanın En İyi 10 Softgel Makinesi Üreticisi (2024)
Akışkan Yataklı Granülatör: İşlem, Çalışma Prensibi, Türleri, Amacı ve Ayar Parametreleri
Akışkan yataklı granülatör tozları bir işlemle granüllere dönüştürmek için kullanılan bir ilaç işleme ekipmanıdırled granülasyon. Granülasyon, parçacık boyutunu artırarak, akışkanlığı iyileştirerek ve toz oluşumunu azaltarak tozların özelliklerini iyileştirir.
Akışkan Yatak Avantajları ve Uygulamalarına Genel Bakış
Akışkan yataklı bir granülatörde, katı parçacıkları kaldırmak ve çalkalamak için toz yatağının altından bir hava akışı verilir. Bu akışkanlaştırma işlemi, yoğun tozu daha düzgün ve verimli bir işleme için akışkan benzeri bir duruma dönüştürür. Sıvı bağlayıcı çözelti (örneğin su, çözücü) daha sonra akışkanlaştırılmış tozların üzerine püskürtülerek, parçacıkların birbirine yapışarak daha büyük kütleler oluşturmasıyla granül büyümesinin teşvik edilmesi sağlanır.
Akışkan yataklı granülatör prensip şeması
Akışkanlaştırılmış yataklar çok iyi karıştırma ve sıcaklık kontrol yetenekleri sağlar. Bu özellikler, aşağıdaki gibi işlem parametrelerinin özelleştirilmesine olanak tanır: hava akış hızı, püskürtme hızı, giriş hava sıcaklığı ve istenilen özelliklere sahip granüller üretmek için nem. Yaygın tasarım varyasyonları arasında akışkanlaştırmayı ve püskürtmeyi optimize etmek için üstten püskürtme, alttan püskürtme ve teğetsel püskürtme bulunur.
İlaç-Makineleri-Akışkan Yatak-grandpack
Akışkan yatak teknolojisi, gereksinimlere bağlı olarak öğütme, kaplama, kurutma gibi çok çeşitli ek ikincil işleme operasyonlarıyla da entegre edilebilir. Bu esneklik, akışkan yatak granülasyonunu ilaç, gıda, kimyasallar, gübreler ve daha fazlası dahil olmak üzere birçok sektörde en kullanışlı teknolojilerden biri haline getirir.
Akışkan Yatak Granülasyon Prosesinin Açıklanması
Akışkan yatak prosesi birkaç temel aşamadan oluşur:
1. Toz besleme
Başlangıç malzemesi, genellikle aktif ilaç parçacıkları veya bileşenleriyle karıştırılmış inert bir taşıyıcı toz, granülatör odasına yukarıdan yüklenir. Tozun düzgün bir şekilde akışkanlaşması için serbest akışlı olması gerekir.
2. Akışkanlaştırma ve ön ısıtma
Parçacıkları yukarı kaldırmak için alttan bir hava akışı verilir. Hava hızı arttıkça, sürükleme kuvvetlerinin parçacık ağırlığına eşit olduğu bir noktaya ulaşılır ve yatak askıya alınır ve bir sıvı gibi davranır. Yatak bu süre boyunca çalışma sıcaklığına önceden ısıtılır.
3. Sıvı sprey
Yatak akışkan hale ve sıcaklığa ulaştığında, sıvı çözelti nozullar aracılığıyla akışkanlaştırılmış parçacıklara püskürtülür. Bu sıvı bir bağlayıcı veya granülasyon maddesi içerir. Damlacıklar parçacık yüzeyleriyle temas ettikçe, sıvı yayılır ve parçacıkları daha büyük kümeler halinde bağlar.
4. Islak kütleleme
Daha fazla sıvı eklendikçe, daha büyük düzensiz granüller oluşmaya başlar. Uygun sıvı doygunluğunda, neredeyse küresel ve iyi biçimli granüller elde edilir.
5. Kurutma ve soğutma
Isıtılmış giriş havası veya ayrı ısıtma bobinleri ıslak granüllerden nemi alarak onları sertleştirir. Soğuma aşaması granülleri uygun deşarj sıcaklığına getirir.
6. Tarama
Son granüller boyut dağılımı gerekliliklerini karşılamak için titreşimli eleklerden veya değirmenlerden geçirilir. Büyük boyutlu malzemeler daha ileri işleme veya öğütme için geri dönüştürülür.
Sprey kurutma ile akışkan yataklı granülasyon arasındaki fark nedir?
Temel fark, püskürtmeli kurutmanın sıvıyı veya bulamacı tek bir sürekli adımda toza dönüştüren tek adımlı bir işlem olması, akışkan yataklı granülasyonun ise tozları birden fazla parti adımında granül aglomeralarına dönüştürmesidir.
Sprey kurutmada, besleme sıvıları nozullar aracılığıyla sıcak bir kurutma odasına atomize edilir. Damlacıklar, tek adımlarda katı kurutulmuş parçacıklar elde etmek için hızlı nem buharlaşmasına uğrar.
Akışkan yataklarda, halihazırda toz haline getirilmiş başlangıç malzemeleri bağlayıcı sıvı ilavesi ve ardından ıslak granülasyon için akışkanlaştırılır. Ayrı kurutma aşaması nemli granülleri sertleştirilmiş son ürüne dönüştürür. Ek eleme/öğütme adımları parçacık boyutu dağılımını daha da değiştirir.
Yani akışkan yataklar, birden fazla fazda granül oluşumu ve büyüme mekaniğini içerirken, püskürtmeli kurutma sadece tek bir aşamada hızlı parçacık kuruma hızı kinetiğine odaklanır.
Akışkan yataklı granülasyonun parametreleri nelerdir?
Daha sonra, akışkan yataklı granülasyon prosesi hakkında bilgi edinmeniz gerekecektir. Akışkan yataklı granülasyonda ayarlanabilen yaygın proses parametreleri şunlardır:
- Hava akış hızı: Daha yüksek hava akışı akışkanlaşmayı ve karıştırmayı yoğunlaştırır ancak aşırı türbülanslıysa büyümeyi bozabilir. Tipik aralık 10-100 m3/saat/m2'dir.
- Giriş hava sıcaklığı: Genellikle 40-80°C. Daha yüksek sıcaklıklar daha fazla kurutma için gereklidir ancak bağlayıcı veya aktif bileşen hassasiyeti nedeniyle sınırlı olabilir.
- Sıvı püskürtme oranı: Tipik olarak 5-100 g/dak. Hızlı püskürtme ince tanecikleri teşvik ederken, yavaş püskürtme doygunluğa ve büyük topaklara kontrolsüz büyümeye neden olur.
- Atomizasyon hava basıncı: 2-6 bar. Daha iyi dağıtım için ince damlacıklar oluşturur. Daha yüksek basınçlar atomizasyon kalitesini artırır.
- Nozul konfigürasyonu: İstenilen akış desenlerine bağlı olarak üstten püskürtme, alttan püskürtme, teğetsel püskürtme seçenekleri. Birden fazla nozul kullanılabilir.
- Granülasyon sıvısı: Su, çözücüler veya sulu çözeltiler. Viskozite ve bağlayıcı granül büyüme mekaniğini etkiler.
- Yatak nemi: Kuruma hızını etkiler. Giriş hava koşulları veya ayrı kurutma aşaması ile kontrol edilir.
- Eleme/öğütme: Son parçacık boyutu dağılımı, ilave ikincil işlem adımlarıyla kontrol edilir.
Granülatör Makinasının Amacı Nedir?
Farmasötik işlemede granülatörün temel amaçları şunlardır:
- Toz akış özelliklerini iyileştirin: Granülasyon, ortalama parçacık boyutunu artırarak ve yüzey alanını azaltarak ince kohezif tozları serbest akışlı granüler malzemelere dönüştürür. Bu, üretim boyunca malzemelerin daha kolay elleçlenmesini ve işlenmesini sağlar.
- Tekdüze karıştırmayı etkinleştir: Akışkan yatakta ilaç maddeleri ve yardımcı maddelerin karıştırılması daha etkili ve homojendir ve bu da son tabletlerde veya kapsüllerde tutarlı dozaja yol açar. Ayrışma en aza indirilir.
- Toz seviyelerini azaltın: Granüller, ince tozlara kıyasla daha düşük toz emisyonuna sahip olduğundan, güvenliği, çevre kontrolünü, kayıp önlemeyi ve kaliteyi artırır.
- Parçacık özelliklerini geliştirin: Granül sertliği, yoğunluğu ve boyut özellikleri, tabletleme, kapsül doldurma ve son ilaç salım profili gibi sonraki proseslere uyacak şekilde işleme sırasında özelleştirilir.
- Kararlılığı artırın: Nem, hava veya diğer bileşenlerle uyumsuzluklara duyarlı ilaçlar, stabil granül yapıları içinde stabilize edilebilir. Raf ömrü artırılır.
Bu sayede granülatörler, farmasötik ürünün kritik kalite özellikleri üzerinde önemli esneklik ve kontrol olanağı sağlamaktadır.
Akışkan Yataklı Granülatörün İşlevi Nedir?
Akışkan yataklı granülatör, çok sayıda önemli farmasötik işleme işlevine hizmet eder:
- İyi biçimli granül yapıları üretir: Akışkanlaştırılmış koşullar, uygun sıvı doygunluğu ile mükemmel granül büyümesine olanak tanıyan sık ve nazik parçacık çarpışmaları sağlar ve aşırı boyut büyümesini en aza indirir.
- Homojen ve verimli kurutmayı teşvik edin: Hava-partikül arayüzleri arasındaki yüksek ısı transfer oranları sayesinde hızlı nem giderimi sağlanır. Sıcaklık homojendir ve bu da lokal aşırı kurumayı önler.
- Sürekli çalışmaya izin ver: Akışkan yataklar, toz besleme, granülasyon, kurutma ve boşaltma gibi birçok işlemi sabit durumda gerçekleştirerek verimliliği en üst düzeye çıkarır.
- Süreç değişkenleri üzerinde hassas kontrolü etkinleştirin: Sıcaklık, hava akışı, püskürtme hızı vb. gibi kritik parametreler ölçülebilir ve tutarlı granül kalitesi elde etmek için doğru bir şekilde kontrol edilebilir.
- İyi toz-sıvı teması sağlayın: Akışkanlaştırma, etkili agregasyon için tüm toz yüzeylerinin püskürtmeye maruz kalmasını sağlar. Mekanik karıştırıcıların aksine durgun bölgeler yoktur.
- Esnek ölçeklendirmeye izin verin: Akış desenleri ve proses verimliliği farklı kap boyutlarında nispeten tutarlıdır, bu nedenle ölçekleme diğer teknolojilere kıyasla basitleştirilmiştir.
Görüldüğü gibi akışkan yataklar, optimum proses verimliliği ve kontrolü altında hassas kurutma, granülasyon ve partikül tasarım işlemleri için kullanılan çok yönlü çok amaçlı ünitelerdir.
Akışkan Yataklı Granülatör Çeşitleri
Endüstriyel üretimde kullanılan akışkan yataklı granülatör sistemlerinin birkaç yaygın çeşidi vardır. Derinlemesine inceleyelim ve orada bulabileceğiniz farklı akışkan yataklı granülatör türlerine bir göz atalım.
Üst Sprey Sıvı Yatakları
Üst Sprey Akışkan Yatakları Granülatör
En yaygın kullanılan tasarım, püskürtme sıvısının granülatör haznesinin üstündeki akışkanlaştırılmış tozun üstündeki atomize edici nozullar aracılığıyla verildiği tasarımdır. Şunları sunar:
- Çoğu uygulamaya uygun, basit ve uygun maliyetli dikey tasarım
- Akışkanlaştırılmış parçacıklar üzerine düzgün aşağı doğru sıvı dağılımı
- Sprey kurutma ve kabuk oluşumu riski minimumdur
- Çoğunlukla küresel şekilli ve iyi biçimli granüller
Dezavantajları arasında parçacık yüzeylerinde kalın sıvı birikmesi ve granül katmanlarının düzensiz bir şekilde üst üste gelmesi yer alır.
Alt Sprey Akışkan Yatakları
Akışkan Yataklı Granülatör Bottonlu
Burada sıvı, haznenin tabanındaki atomize edici bir nozul aracılığıyla yukarı doğru hareket eden akışkanlaştırılmış parçacıkların bir çeşmesine püskürtülür. Şunları sunar:
- Üstten püskürtmeye kıyasla aşırı ıslatma azaltıldı
- Dar kalış süresi dağılımı
- Kontrolsüz bir şekilde ince parçacıklara dönüşme olasılığı daha azdır
- Daha fazla gözeneklilik ve daha iyi kurutma verimliliği
Sınırlama, aşağı doğru akan parçacık çeşmesinde yukarı doğru püskürtmenin kontrol edilebilirliğinin zayıf olmasıdır.
Tanjantsal Sprey Akışkan Yatakları
Tanjant Sprey Akışkan Yatakları Gradatör
Nozullar granülatörün orta bölümünde yer alır ve dönen sıvı-partikül momentum etkileşimi için radyal hava akışına teğetsel açılıdır. Avantajları arasında çok düzgün püskürtme dağılımı ve üst ve alt varyantlar arasında ara ürün nitelikleri bulunur. Döndürme karıştırma küresel granüller sağlar. Sınırlı ölçeklendirme potansiyeli ve operasyonel karmaşıklık başlıca zorluklardır.
Üst-alt, üst-teğetsel veya teğetsel-alt yapılandırmaları gibi kombinasyonlar da kullanılır. Genel olarak, akışkan yatak çeşitliliği ve özelleştirilebilirlik, farmasötik üretimde istenen granül özelliklerinin yakın bir şekilde elde edilmesini sağlayan önemli bir faydadır.
Götürmek
Akışkan yataklı granülasyon, ilaç üretiminde hayati bir parçacık mühendisliği işlemidir. Tozları, son işlem ve nihai ürün performansını belirleyen kararlılık, yapı, akış ve boyut açısından özelleştirilmiş özelliklere sahip küresel granüllere dönüştürür.
Akışkanlaştırılmış yatak, hassas değişken kontrolü altında, entegre, sürekli ve verimli bir kurulumda, karıştırma, aglomerasyon, nem giderme gibi çeşitli kritik işlemlerin gerçekleştirilmesini sağlar. İkincil işleme adımlarıyla esnek entegrasyonla, frezeleme ve kaplamaAkışkan yatak teknolojisi, yüksek kaliteli ilaçların üretiminde çeşitli uygulamalarda benzersiz avantajlar sunmaktadır.
İlgili Makaleler:
- İlaç Üretiminde Akışkan Yataklı Granülasyon ve İşleme. (2024, EYLÜL, 19).UPM İlaçları. https://www.upm-inc.com/fluidized-bed-granulation-in-pharmaceutical-manufacturing
- Akışkan Yataklı Granülasyonun Anlaşılması. (2024, EYLÜL, 14). Pharmtech. https://www.pharmtech.com/view/understanding-the-value-of-excipient-grade
- Akışkan Yatak Granülasyonu: Umut Vaat Eden Bir Teknik. Int. J. Eczacılık Bilimi Rev. Res., 64(2), Eylül - Ekim 2020. https://globalresearchonline.net/journalcontents/v64-2/22.pdf