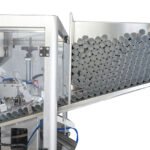
A Comprehensive Guide to Tube Filling Machines

Top 10 Softgel Machine Manufacturers In The World(2024)
Fluidized Bed Granulator: Process,Working Principle, Types, Purpose, and Setting Parameters
A fluidized bed granulator is a piece of pharmaceutical processing equipment used to convert powders into granules through a process called granulation. Granulation improves the properties of powders by increasing particle size, improving flowability, and reducing dust generation.
Overview of Fluid Bed Benefits and Applications
In a fluidized bed granulator, an air flow is introduced from below the powder bed to lift and agitate solid particles. This fluidization process transforms the dense powder into a fluid-like state for more uniform and efficient processing. The liquid binding solution (e.g. water, solvent) is then sprayed onto the fluidized powders to promote granule growth as particles stick together into larger masses.
Fluid bed granulator principle schematic
Fluidized beds provide very good mixing and temperature control capabilities. These features allow customization of process parameters like airflow rate, spray rate, inlet air temperature and humidity to produce granules with desired properties. Common design variations include top spray, bottom spray, and tangential spray to optimize fluidization and spraying.
Pharmaceutical-Machinery-Fluidized Bed-grandpack
Fluidized bed technology can also be integrated with a wide range of additional secondary processing operations like milling, coating, drying depending on requirements. This flexibility makes fluid bed granulation one of the most useful technologies across many industries including pharmaceuticals, food, chemicals, fertilizers and more.
Explaining the Fluid Bed Granulation Process
The fluid bed process involves several key stages:
1. Powder feeding
The starting material, usually an inert carrier powder mixed with active drug particles or ingredients, is loaded into the granulator chamber from overhead. Powder should be free flowing to fluidize properly.
2. Fluidization and preheating
An airflow is introduced from the bottom to lift particles up. As air velocity increases, a point is reached where the drag forces equals particle weight, and the bed becomes suspended and behaves like a fluid. The bed is preheated to operating temperature during this time.
3. Liquid spray
Once bed reaches fluidized state and temperature, liquid solution is sprayed onto the fluidized particles through nozzles. This liquid contains a binder or granulating agent. As droplets contact particles surfaces, the liquid spreads and binds particles into larger agglomerates.
4. Wet massing
As more liquid is added, larger irregular granules start to form. At the proper liquid saturation, nearly spherical and well-formed granules are achieved.
5. Drying and cooling
Heated inlet air or separate heating coils remove moisture from wet granules to harden them. Cool-down phase brings granules to suitable discharge temperature.
6. Screening
Final granules are passed through vibrating screens or mills to achieve size distribution requirements. Oversized materials are recycled for further processing or milling.
What is the difference between spray drying and fluid bed granulation?
The key difference is that spray drying is a one-step process that dries liquid or slurry into powder in one continuous step whereas fluid bed granulation converts powders into granule agglomerates in multiple batch steps.
In spray drying, feed liquids are atomized via nozzles into a hot drying chamber. The droplets undergo rapid moisture evaporation to yield solid dried particles in single steps.
In fluid beds, already powdered starting materials are fluidized for binder liquid addition and subsequent wet granulation. Separate drying stage converts moist granules into hardened final product. Additional screening/milling steps further modify particle size distribution.
So fluid beds involve granule formation and growth mechanics over multiple phases whereas spray drying focuses only on rapid particle drying rate kinetics in one stage.
What are the parameters for fluid bed granulation?
Next, you will need to get to know about the fluid bed granulation process. Common process parameters that can be adjusted in fluid bed granulation include:
- Airflow rate: Higher airflow intensifies fluidization and mixing but can disrupt growth if excessively turbulent. Typical range is 10-100 m3/hr/m2.
- Inlet air temperature: Usually 40-80°C. Higher is needed for increased drying but may be limited by binder or active ingredient sensitivity.
- Liquid spray rate: Typically, 5-100 g/min. Fast spraying promotes fines while slow rate causes saturation and uncontrolled growth into large lumps.
- Atomization air pressure: 2-6 bars. Creates fine droplets for better distribution. Higher pressures improve atomization quality.
- Nozzle configuration: Top spray, bottom spray, tangential spray options depending on desired flow patterns. Multiple nozzles can be used.
- Granulation liquid: Water, solvents, or aqueous solutions. Viscosity and binder affect granule growth mechanics.
- Bed humidity: Impacts drying rate. Controlled via inlet air conditions or separate drying stage.
- Screening/milling: Final particle size distribution controlled through additional secondary processing steps.
What Is The Purpose Of A Granulator Machine?
The main purposes of a granulator in pharmaceutical processing include:
- Improve powder flow properties: Granulation transforms fine cohesive powders into free-flowing granular materials by increasing average particle size and reducing surface area. This allows easier handling and processing of materials throughout manufacturing.
- Enable uniform blending: Mixing of drug substances and excipients is more effective and homogeneous in the fluidized bed leading to consistent dosage in the final tablets or capsules. Segregation is minimized.
- Reduce dust levels: Granules have lower dust emission compared to fine powders which improves safety, environmental control, loss prevention and quality.
- Develop particle characteristics: Granule hardness, density and size properties are customized during processing to suit downstream processes like tableting, capsule filling as well as final drug release profile.
- Improve stability: Drugs susceptible to moisture, air or incompatibilities with other ingredients can be stabilized inside stable granule structures. Shelf life is enhanced.
Thus, granulators allow considerable flexibility and control over critical quality attributes of the pharmaceutical product.
What Is The Function Of Fluid Bed Granulator?
The fluid bed granulator serves multiple important pharmaceutical processing functions:
- Produce well-formed granule structures: Fluidized conditions provide frequent, gentle particle collisions enabling excellent granule growth with proper liquid saturation and minimizes excessive size enlargement.
- Promote uniform and efficient drying: Rapid moisture removal is enabled by high heat transfer rates between air-particle interfaces. Temperature is uniform which prevents localized over-drying.
- Allow continuous operation: Fluidized beds perform several operations like powder feeding, granulation, drying and discharge in steady state thus maximizing productivity.
- Enable precision control over process variables: Critical parameters like temperature, airflow, spray rate etc. can be measured and controlled accurately to produce consistent granule quality.
- Provide good powder-liquid contact: Fluidization ensures exposure of all powder surfaces to spraying for effective aggregation. No stagnant regions exist unlike mechanical mixers.
- Allow flexible scale up or scale down: Flow patterns and process efficiency are relatively consistent across different vessel sizes thus scaling is simplified compared to other technologies.
As you can see, fluidized beds are versatile multipurpose units used for sensitive drying, granulation and particle design operations under optimal process efficiency and control.
Types of Fluid Bed Granulators
There are several common variations of fluid bed granulator systems used in industrial production. Let’s deep dive and take a look at the different types of fluid bed granulators that you can find out there.
Top Spray Fluid Beds
Top Spray Fluid Beds Granulator
The most widely used design where spray liquid is introduced through atomizing nozzles at the top of the granulator chamber above the fluidized powder. It offers:
- Simple, cost-effective vertical design suitable for most applications
- Uniform downward liquid dispersion onto fluidized particles
- Minimal risk of spray drying and crust formation
- Mostly spherically shaped and well-formed granules
Drawbacks include thick liquid deposition at particle surfaces and uneven overlapping granule layers.
Bottom Spray Fluid Beds
Fluid Beds Granulator with Botton
Here liquid is sprayed into an upward moving fountain of fluidized particles through an atomizing nozzle at the base of the chamber. It offers:
- Reduced over wetting compared to top spray
- Narrow residence time distribution
- Less chance of uncontrolled nucleation into fines
- More porosity and better drying efficiency
Limitation is poor controllability of upward spray in a downward flowing particle fountain.
Tangential Spray Fluid Beds
Tangential Spray Fluid Beds Gradulator
Nozzles are situated at the middle section of the granulator and angled tangentially to the radial air flow for swirling liquid-particle momentum interaction. Benefits include very uniform spray distribution and intermediate product attributes between top and bottom variants. Swirl mixing provides spherical granules. Limited scale up potential and operational complexity are main challenges.
Combinations like top-bottom, top-tangential or tangential-bottom configurations are also used. Overall, fluid bed variety and customizability is an important benefit enabling close achievement of desired granule specifications in pharmaceutical production.
Take Away
Fluidized bed granulation is a vital particle engineering operation in pharmaceutical manufacturing. It transforms powders into spherical granules with customized properties of stability, structure, flow and size that determine downstream processing as well as final product performance.
The fluidized bed enables several critical operations - mixing, agglomeration, moisture removal - to be performed in one integrated, continuous and efficient setup under precision variable control. With flexible integration with secondary processing steps like milling and coating, fluid bed technology offers unparalleled advantages across diverse applications in making high quality pharmaceuticals.
Related Articles:
- Fluid-Bed Granulation & Processing in Pharmaceutical Manufacturing. (2024, SEP, 19).UPM Pharmaceuticals. https://www.upm-inc.com/fluidized-bed-granulation-in-pharmaceutical-manufacturing
- Understanding Fluidized-Bed Granulation. (2024, SEP, 14). Pharmtech. https://www.pharmtech.com/view/understanding-the-value-of-excipient-grade
- Fluidized Bed Granulation: A Promising Technique. Int. J. Pharm. Sci. Rev. Res., 64(2), September - October 2020. https://globalresearchonline.net/journalcontents/v64-2/22.pdf