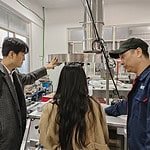
3 endroits et 8 étapes pour importer une machine d'emballage sous blister de Chine
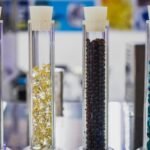
Machine de fabrication de capsules de gel mou : types, principes de fonctionnement, application et conseils d'achat
Granulateurs dans l’industrie pharmaceutique – Un aperçu complet
La fabrication pharmaceutique est une industrie complexe. Si vous envisagez de vous lancer dans le monde de la fabrication pharmaceutique, vous devrez faire face à de nombreuses machines complexes. Granulateurs sont un parfait exemple pour eux.
Le rôle d'un granulateur est de transformer de la poudre ou des particules fines en granulés uniformes et fluides. Ce processus est essentiel pour créer des produits pharmaceutiques de qualité constante. Ils offriront également une meilleure aptitude au traitement et une administration optimale du médicament. Lisez la suite et apprenons-en plus sur les granulateurs en détail.
Qu'est-ce qu'un granulateur ? 
Un granulateur est un équipement spécial utilisé dans industries pharmaceutiques, chimiques et autres. Il peut transformer des matériaux en poudre ou fins en granulés. En d'autres termes, cet outil indispensable peut transformer les matières premières en une forme plus facile à manipuler. Par conséquent, les granulateurs jouent un rôle majeur dans la fabrication de produits pharmaceutiques.
Qu’est-ce que la granulation dans les produits pharmaceutiques ?
La granulation est une technique qui transforme les particules fines en granules. En d'autres termes, elle transforme les particules pulvérulentes en une structure plus stable. Cette transformation n'est pas seulement un processus mécanique. Elle peut améliorer la qualité, la stabilité et les performances des formulations pharmaceutiques.
Quel est le but d'un granulateur ?
Il existe de nombreuses raisons d'utiliser un granulateur dans l'industrie pharmaceutique. Voici les principales raisons :
- Amélioration de la fluidité
Les granulateurs sont capables de transformer des poudres fines et cohésives en granulés fluides. Ces granulés sont faciles à manipuler et à traiter lors des étapes de fabrication. Les fabricants de produits pharmaceutiques peuvent facilement traiter les granulés lors de la fabrication de comprimés et du remplissage de gélules.
- Améliorer la compressibilité
Les granulés ont une meilleure compressibilité que les poudres fines. Cela est important pour créer des comprimés uniformes et robustes avec une teneur en médicament constante. Cela aide les sociétés pharmaceutiques à améliorer la qualité de leurs médicaments.
- Distribution uniforme des médicaments
Le processus de granulation peut assurer une distribution plus uniforme des principes actifs pharmaceutiques (API). Cela peut contribuer à garantir un dosage constant du médicament à tout moment.
- Réduire la poussière
Le processus de conversion de poudres fines en gros granulés peut minimiser la production de poussière. Cela peut éventuellement améliorer la sécurité sur le lieu de travail. De plus, cela peut également contribuer à réduire les pertes de produits.
- Contrôle de la libération
Il est également possible d'utiliser des techniques de granulation spécifiques pour contrôler les formulations de libération des médicaments. Cela aide les fabricants de produits pharmaceutiques à fabriquer des médicaments conformément aux recommandations.
Quel est le processus de granulation dans l’industrie pharmaceutique ?
Avant d'acheter un granulateur, il est important de savoir à quoi ressemble le processus de granulation. Voici un aperçu de l'ensemble du processus.
Étape 1 – Préparation des matières premières
La première étape consiste à analyser minutieusement toutes les propriétés physiques et chimiques des matières premières. Cela permet de garantir que tous les ingrédients répondent aux spécifications de qualité et de pureté. De plus, cela implique également d'évaluer la distribution granulométrique initiale des poudres. En outre, ce processus peut impliquer de mesurer et de contrôler les niveaux d'humidité des ingrédients.
Étape 2 – Mélanger et homogénéiser
La deuxième étape consiste à mélanger tous les ingrédients secs. Cela comprend les ingrédients pharmaceutiques ainsi que les excipients. Pendant le processus de mélange, il est important de garantir une répartition uniforme de tous les composants. Les fabricants de produits pharmaceutiques peuvent utiliser des mélangeurs en V, des mélangeurs planétaires et des mélangeurs à haut cisaillement pour le mélange.
Au moment de mélanger les ingrédients, il est également important de veiller à l'optimisation du temps. Cela les aidera à obtenir le mélange parfait.
Étape 3 – Granulation
Méthode de granulation par voie humide
Il s'agit du procédé le plus courant. Il commence par la préparation du liant, qui consiste à créer la solution de liant liquide. Ensuite, les fabricants ajoutent progressivement la solution de liant au mélange de poudre. Cela aidera à créer les grappes de granulés initiales grâce au mélange mécanique. Le contrôle de l'humidité est essentiel tout au long de ce processus. Il garantira une formulation appropriée des granulés.
Méthode de granulation à sec
La méthode de granulation à sec commence par l'application d'une pression élevée pour comprimer le mélange de poudre. Les fabricants créent ensuite des masses solides ou des rubans. Après cela, ils décomposent les masses comprimées en granulés. Le processus de criblage garantit une taille de granule uniforme à la fin du processus.
Étape 4 – Séchage
Ce procédé consiste à éliminer l'excès d'humidité des granulés. Les fabricants de produits pharmaceutiques utilisent trois principales techniques de séchage. Elles comprennent :
- Séchage en lit fluidisé
- Séchage sur plateau
- Séchage sous vide
Tout au long du processus de séchage, il est essentiel de maintenir une température précise. Cela peut empêcher la dégradation du matériau. Au cours de ce processus, il est également important de s'assurer que le niveau d'humidité final répond aux spécifications.
Étape 5 – Dimensionnement et criblage
Le processus de réduction de taille décomposera les gros morceaux de granulés en morceaux de taille uniforme. Les fabricants utiliseront ensuite des tamis mécaniques ou des broyeurs pour le criblage. L'étape suivante consiste à assurer la classification par taille. C'est là qu'ils séparent les granulés en particules souhaitées avec des plages de taille appropriées. Il est ensuite possible d'éliminer la poussière et les autres granulés surdimensionnés.
Étape 6 – Lubrification
L'étape suivante consiste à incorporer des agents lubrifiants appropriés. Parallèlement à cela, un revêtement uniforme est également essentiel. Pour éviter le collage, les fabricants réduiront la friction lors des étapes de traitement suivantes. De plus, ils amélioreront également le mouvement et la compressibilité des granulés.
Étape 7 – Contrôle de la qualité
Lors du contrôle qualité, des tests physiques et des analyses chimiques seront effectués. Les tests physiques visent à évaluer les propriétés des granulés. Ils comprennent la taille des particules, la masse volumique apparente et la teneur en humidité. D'autre part, l'analyse chimique confirmera l'uniformité des ingrédients actifs.
Étape 8 – Emballage et stockage
Il est important d'utiliser des contenants adaptés pour le conditionnement. Les emballages étanches à l'humidité jouent ici un rôle majeur. Après le conditionnement, les granulés doivent être stockés correctement dans des conditions spécifiques.
5 types courants de granulateurs pharmaceutiques
Il existe de nombreux types de granulateurs disponibles à l'achat. Il est important que vous fassiez le bon choix lorsque vous en achetez un. Voici 5 des types de granulateurs les plus courants disponibles :
Granulateurs oscillants
Ces granulateurs sont équipés d'un rotor oscillant. Il se déplace d'avant en arrière pendant le processus de granulation. La poudre devra passer à travers la maille ou le tamis qui oscille pour créer des particules de la taille souhaitée. La taille des granulés varie en fonction de la taille des trous disponibles sur le tamis. Il vous est possible d'ajuster cette taille au tamis en fonction de vos besoins. De plus, vous pouvez également ajuster la vitesse de rotation en fonction des propriétés de votre matériau.
Vous pouvez utiliser un granulateur oscillant pour traiter :
- Poudres sensibles à l'humidité
- Additifs alimentaires
Granulateur à rouleaux compacteurs
Ces machines utilisent la technique de granulation à sec. Vous pouvez l'utiliser pour convertir des poudres en granulateurs sans utiliser de liquide. À l'intérieur du granulateur, vous verrez deux rouleaux contrarotatifs différents. Après avoir versé la poudre, elle se comprime entre deux feuilles de ruban. Ensuite, il décompose la feuille compacte en granulés.
Vous pouvez utiliser un granulateur à rouleaux compacteurs pour traiter :
- Poudres sensibles à l'humidité
- Poudres thermosensibles
Granulateur à haut cisaillement
Il s'agit de granulateurs à grande vitesse. En d'autres termes, ces granulateurs peuvent mélanger des poudres à grande vitesse lors de la formation de granulés. Par conséquent, vous pouvez en tirer un niveau d'efficacité plus élevé. De plus, les forces mécaniques intenses de ces granulateurs assurent un mélange complet. Vous pouvez garantir la cohérence de la densité et de la taille de ces granulateurs.
Granulateur vibrant
Les granulateurs vibrants sont idéaux pour compléter le processus de granulation. Ils sont assez similaires aux granulateurs à fonction oscillante. Cependant, ils ne font pas tourner les particules pour les décomposer. Au lieu de cela, cela se produit par un processus de vibration. Il assure une décomposition précise des granulés aux tailles souhaitées.
Un granulateur vibrant est idéal pour :
- Poudres thermosensibles
- Poudres sensibles à l'humidité
Granulateur à lit fluidisé
UN Granulateur à lit fluidisé Les poudres de traitement sont suspendues par un flux d'air ascendant. Un état fluide est alors créé. Il s'agit d'une étape où les particules se comportent comme un fluide. Ainsi, vous pouvez assurer une répartition uniforme de l'humidité et de la chaleur. La solution liante pénètre ensuite dans les fluides et se colle pour créer des granules.
Comment choisir un bon granulateur ?
Comment choisir le meilleur granulateur pour répondre à vos besoins ? Gardez à l'esprit les conseils suivants :
- Besoins de production
Avant d'acheter le granulateur, déterminez les produits pharmaceutiques que vous devez produire. Par exemple, vous devriez vous procurer un granulateur à feuilles pour produire des granulés de comprimés. Le granulateur que vous achetez doit également être en mesure de gérer toutes vos tailles d'entrée et de sortie.
- Facteurs opérationnels
Faites également attention à la facilité d'entretien, au niveau sonore et à la consommation électrique du granulateur. Cela vous aidera à faire fonctionner le granulateur efficacement.
- Propriétés matérielles
Vous devez acheter le bon granulateur en fonction des matériaux avec lesquels vous travaillez. C'est là que vous devez vous concentrer sur la dureté, la fluidité, la teneur en humidité et la fragilité des matériaux avec lesquels vous travaillez. Par exemple, si les matériaux sont sensibles à l'humidité, vous devez vous procurer un granulateur sec.
Obtenez un granulateur de qualité supérieure avec Grand Pack
Vous avez maintenant une idée claire de ce que sont les granulateurs. En suivant les conseils que nous avons partagés, vous pouvez procéder à l'achat du bon granulateur. Cependant, vous devez l'acheter auprès d'un endroit auquel vous pouvez faire confiance. C'est là que Grand Pack peut vous aider. N'hésitez pas à parcourir les granulateurs que nous avons chez Grand Pack et à obtenir le vôtre. Si vous avez des questions, n'hésitez pas à contacter l'équipe.