
Machine à compter les comprimés : introduction, principe de fonctionnement, types, principaux composants et conseils d'achat
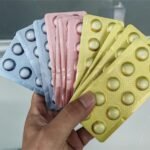
Types d'emballages sous blister dans l'industrie pharmaceutique
Le processus d'emballage sous blister : un guide complet étape par étape
L'emballage sous blister est l'un des procédés d'emballage les plus populaires que vous pouvez trouver dans l'industrie pharmaceutique. Cependant, il est également possible de trouver des applications d'emballage sous blister dans de nombreuses autres industries telles que biens de consommation et dispositifs médicauxIl s'agit d'une technique d'emballage complète et polyvalente. Elle offre protection, visibilité et même inviolabilité.
Continuez à lire et découvrez-en plus sur le processus de conditionnement sous blister du début à la fin. Nous vous aiderons à avoir une idée claire de chaque étape associée au processus.
Comprendre la méthode d'emballage sous blister
Avant d'entrer dans les détails, il est important d'avoir une idée de base de ce qu'est la méthode d'emballage sous blister. Un emballage sous blister se compose généralement de deux éléments principaux. Ils comprennent :
- La cloque – C’est une cavité plastique formée
- Le matériau d’emballage – Généralement une feuille ou une carte
UN la machine d'emballage sous blister moulera la cavité en plastique pour épouser précisément la forme du produit. Il créera à terme une enceinte protectrice et sécurisée. Cette enceinte permettra aux consommateurs de voir l'article, tout en le préservant de toute contamination extérieure.
Guide étape par étape du processus d'emballage sous blister
Plongeons maintenant en profondeur et explorons les différentes étapes liées au processus de conditionnement sous blister :
Étape 1 – Conception et préparation
La toute première étape de l'emballage sous blister consiste à analyser le produit à emballer. Cela implique de mesurer les dimensions exactes du produit. Il est ensuite important d'évaluer la sensibilité globale du produit à différents facteurs environnementaux. Les fournisseurs d'emballages doivent également déterminer les exigences de protection spécifiques.
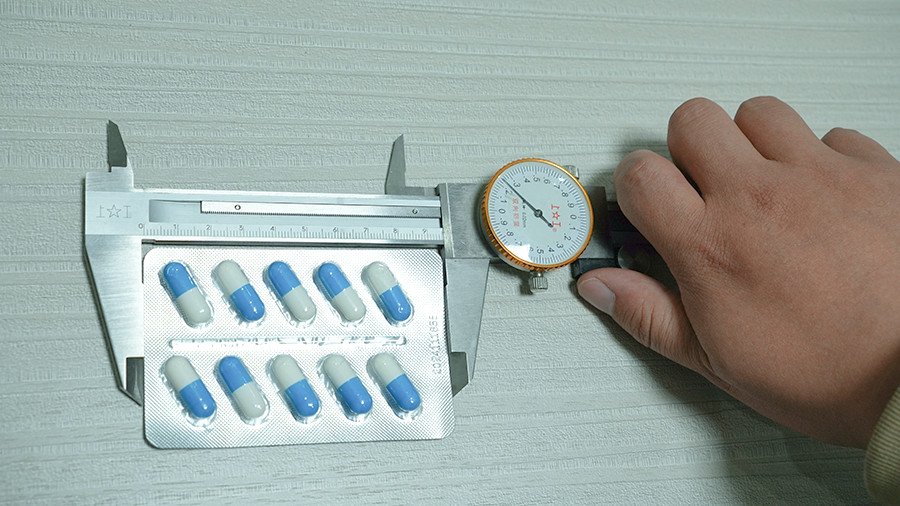
Conception et préparation
Après analyse, ils peuvent commencer le processus de conception de l'emballage. C'est à ce moment-là que les concepteurs créent un plan avec des dimensions précises des cavités et des spécifications de matériaux. Il intégrera des considérations d'intégrité structurelle. Dans la plupart des cas, ces plans tiendront également compte des considérations de marque et d'esthétique.
Étape 2 – Sélection des matériaux
Le choix du bon matériau est également important pour l'ensemble du processus d'emballage sous blister. Les deux composants les plus importants sont les suivants :
Matériau de la cavité de la boursouflure
Certains des matériaux les plus courants disponibles pour la fabrication de la cavité du blister comprennent :
- Chlorure de polyvinyle (PVC) : il s’agit du matériau de cavité de blister le plus courant, le plus rentable et le plus polyvalent disponible.
- Polypropylène (PP) : Ce matériau offre une résistance à la température plus élevée.
- Copolymère d’oléfine cyclique (COC) : Ce matériau est idéal pour les produits pharmaceutiques sensibles.
- Polyéthylène téréphtalate glycol (PETG) : ce matériau offre une excellente clarté et résistance.
Matériau de support
Le matériau de support varie en fonction de l'emballage spécifique et des exigences du produit. Certains des matériaux de support les plus courants comprennent :
- Feuille d'aluminium : ce matériau offre une excellente protection barrière
- Papier/Carton : C'est un matériau économique et imprimable disponible
- Feuilles combinées : les feuilles combinées peuvent offrir plusieurs couches de protection
- Films d'operculage : Ce matériau offre des options d'étanchéité flexibles
Étape 3 – Formation de la cavité de la cloque
La formation de la cavité du blister est l'une des étapes les plus précises de l'emballage sous blister. Elle comprend également quelques étapes importantes. Elles comprennent :
Préparation du moule
Le fabricant créera un moule personnalisé pour répondre aux spécifications du produit. Ces moules ont généralement une construction en aluminium ou en acier de haute qualité. Une ingénierie de précision garantira qu'ils conservent la taille et la forme globales de la cavité.
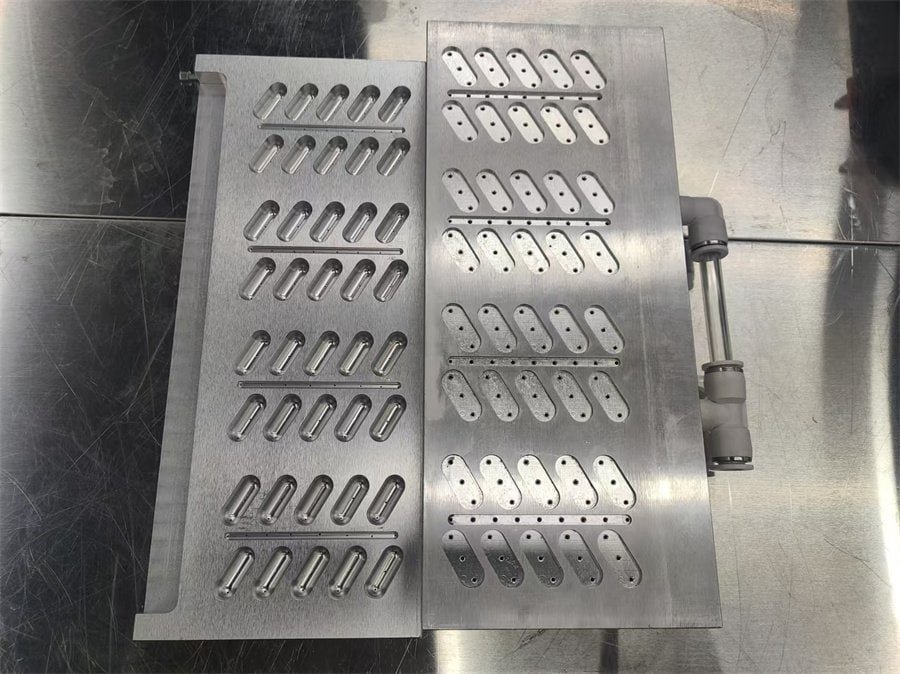
Préparation du moule
Procédé de thermoformage
Le processus de thermoformage commence par le chauffage de la feuille de plastique. Avec l'augmentation de la température, la feuille de plastique sélectionnée atteindra sa température de formage. Ce processus implique des contrôles de température minutieux. Il permet d'éviter la dégradation globale du matériau. Cependant, différents matériaux nécessitent des plages de température spécifiques.
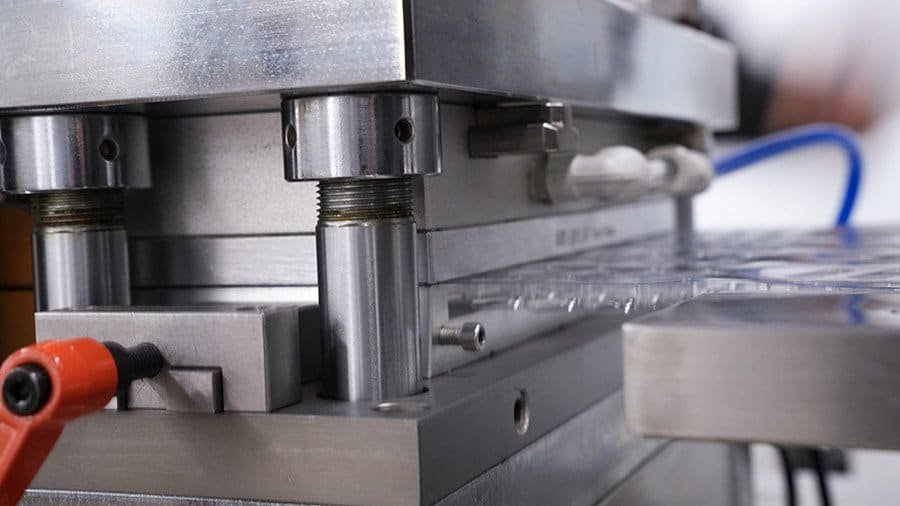
Procédé de thermoformage
Formation de la cavité
Après avoir retiré le plastique chauffé du moule, le fabricant applique un vide ou une pression à l'intérieur. Cela peut les aider à créer une forme de cavité précise. Ils utiliseront ensuite des systèmes de refroidissement pour durcir rapidement le plastique formé.
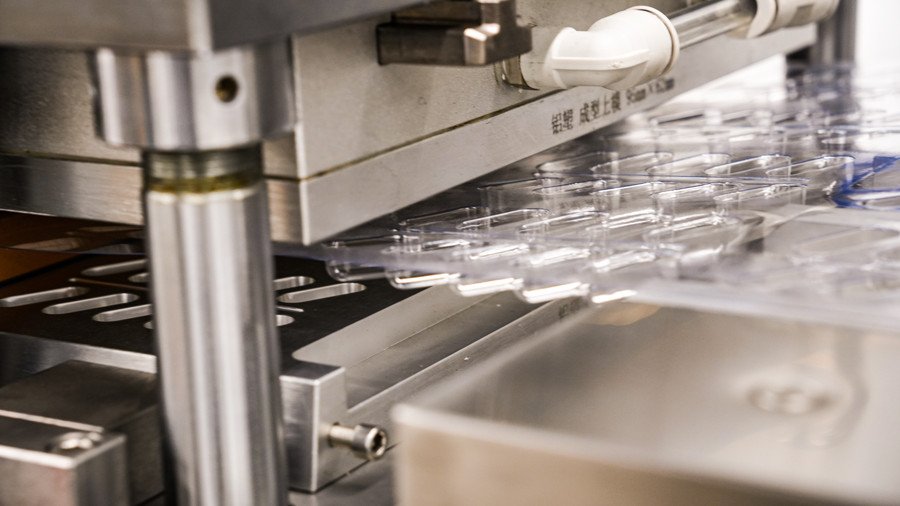
Formation de la cavité
Étape 4 – Placement du produit
C'est également l'une des étapes les plus importantes de la mise sous blister. Sans soin et précision, il ne sera pas possible d'obtenir les meilleurs résultats de ce processus.

Placement de produit
Le placement de produit peut être effectué de manière manuelle ou automatisée. Le placement manuel est idéal pour les produits à faible volume ou spécialisés. Cependant, le placement automatique est la méthode de placement la plus courante pour les produits à volume élevé. C'est là que les systèmes robotisés assureront un positionnement précis et cohérent du placement du produit. Il existe des systèmes de vision qui vérifieront le placement précis du produit.
Qu'il s'agisse d'un placement manuel ou automatisé, le contrôle qualité est important. Les fabricants d'emballages sous blister suivent différentes méthodes de contrôle qualité. Elles comprennent la vérification du poids, la vérification de la précision dimensionnelle et même l'inspection visuelle pour identifier les défauts.
Étape 5 – Sceller l’emballage
Une fois le placement du produit réussi, il est possible de procéder au scellage de l'emballage. Les fabricants d'emballages sous blister utilisent différentes techniques de scellage pour cela. Examinons-les en détail.
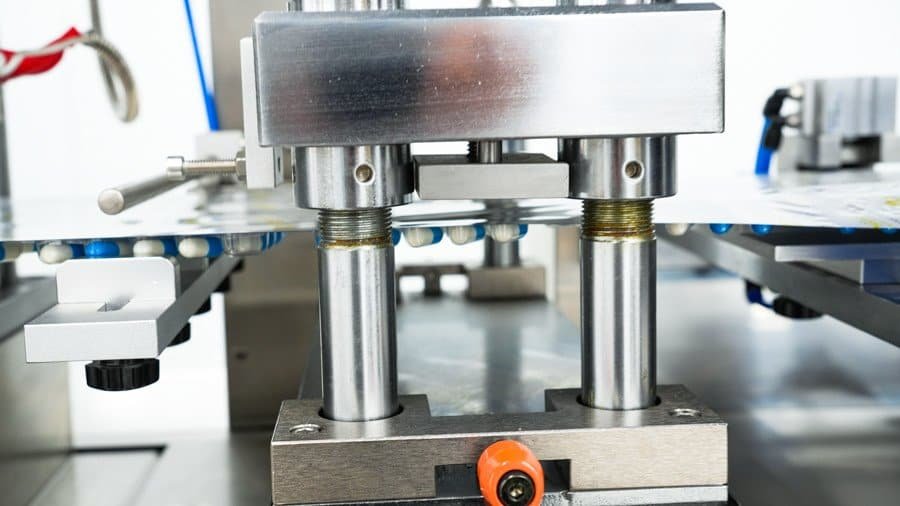
Sceller le paquet
- Thermoscellage : Il s'agit de la méthode la plus courante pour sceller les produits. En fait, la plupart des produits peuvent être thermoscellés.
- Scellage par ultrasons : Si les produits emballés sont sensibles à la chaleur, vous ne pouvez pas procéder au thermoscellage. C'est là que les fabricants se tournent vers les méthodes de scellage par ultrasons.
- Scellage à froid : Une autre alternative au thermoscellage est le thermoscellage à froid. Il utilise des adhésifs sensibles à la pression pour assurer le processus de thermoscellage global.
Ce processus implique également quelques paramètres d'étanchéité importants. Ils comprennent le contrôle de la température, l'application de la pression et le type de maintien. En plus de cela, il est important de sceller pour garantir également les tests d'intégrité.
Étape 6 – Découpe et séparation de l’emballage
Après avoir scellé avec succès un emballage sous blister, les fabricants peuvent s'intéresser aux techniques de découpe. Les fabricants utilisent également différentes techniques de découpe. Explorons-les brièvement :
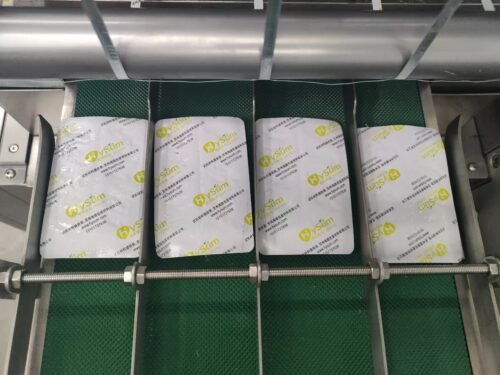
Découpe et séparation des emballages
- Découpe à l'emporte-pièce – Les machines de découpe sépareront les emballages individuels.
- Découpe laser - Si les formes sont délicates ou complexes, la méthode de découpe ne donnera pas les meilleurs résultats. C'est là que la découpe au laser devient importante.
Quoi qu'il en soit, les fabricants veilleront à ce que les bords soient nets et à ce que les dimensions des emballages soient uniformes lors de la découpe. En effet, cela a un impact significatif sur la satisfaction du client.
Lors de la découpe, les fabricants se penchent également sur la découpe et la finition de l'emballage sous blister. C'est là qu'ils se concentrent sur l'élimination de l'excès de matière. Cela se fait par un processus de lissage des bords. Les fabricants peuvent ensuite assurer le raffinement final de la forme.
Étape 7 – Assurance qualité et inspection
Une assurance qualité rigoureuse est importante tout au long du processus de conditionnement sous blister. Elle garantit que les fabricants livrent exactement ce que les clients attendent avec impatience de recevoir. Ils suivent plusieurs processus d'inspection pour garantir la qualité. Ils comprennent :
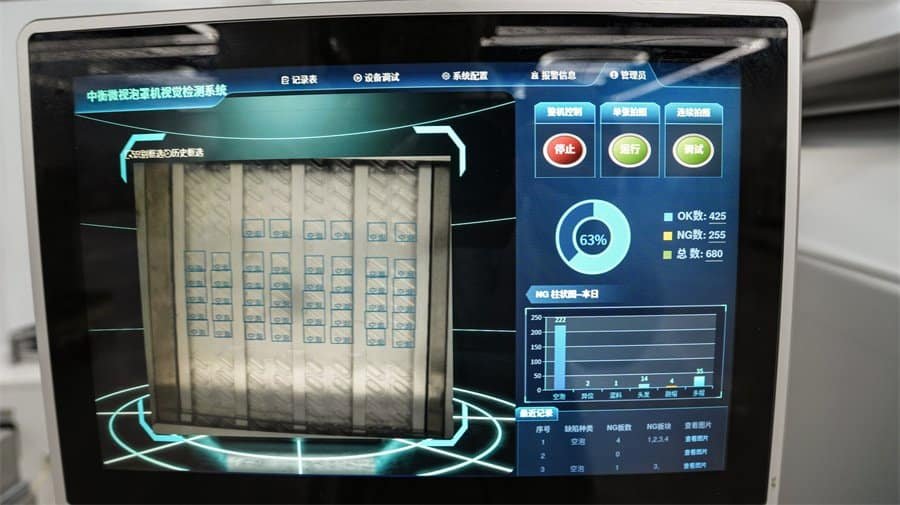
Assurance qualité et inspection
- Assurer la qualité grâce à des systèmes de vision automatisés
- Vérification du poids de l'emballage
- Test de résistance des joints
- Vérification de l'exactitude dimensionnelle globale des colis.
Les fabricants procèdent ensuite à l'échantillonnage et à la validation. Cela implique un contrôle statistique du processus. Il comprend également un étalonnage régulier des équipements. De plus, ce processus garantirait la conformité aux normes de l'industrie.
Étape 8 – Emballage et stockage
Après l'emballage sous blister, il faut également s'occuper du stockage. Cela implique généralement un emballage secondaire. L'emballage secondaire consiste à regrouper les plaquettes alvéolées dans des conteneurs plus grands. Ils peuvent être pratiques pour le stockage et le transport. Cependant, un tel emballage secondaire peut également servir d'emballage extérieur protecteur. Parallèlement à cela, les fabricants se concentreront également sur l'étiquetage et le codage à barres des plaquettes alvéolées.
Il y a quelques considérations importantes à prendre en compte lors du stockage. Le contrôle de la température et de l'humidité occupe une place importante. Sinon, les efforts consacrés à l'emballage sous blister des marchandises seront vains. De plus, il n'est pas judicieux d'exposer l'emballage sous blister à la lumière directe du soleil. Une bonne gestion des stocks est également importante.
Exploration des tendances émergentes en matière d'emballages sous blister
Vous avez maintenant une idée générale de ce à quoi ressemblerait le processus d’emballage sous blister. En attendant, il est important d’examiner également les tendances émergentes en matière d’emballage sous blister. L’une des tendances les plus significatives que vous pouvez observer est celle des matériaux biodégradables. Les consommateurs sont très demandeurs de solutions d’emballage respectueuses de l’environnement. Par conséquent, les fabricants d’emballages sous blister doivent leur fournir des solutions d’emballage biodégradables. Parallèlement à cela, ils doivent également veiller à réduire l’utilisation globale de plastique. C’est la principale raison pour laquelle les solutions d’emballage recyclables suscitent beaucoup d’attention.
En matière d'avancées dans le domaine des emballages sous blister, nous ne pouvons pas simplement ignorer les technologies d'emballage intelligentes. Certaines des innovations les plus récentes que vous pouvez trouver derrière ces emballages concernent le suivi RFID et les indicateurs de résistance à la température. Ils sont également dotés d'intégrations d'informations numériques. Cela peut profiter aux consommateurs finaux ainsi qu'aux détaillants qui vendent les marchandises sur le marché.
Derniers mots
Vous avez maintenant une idée claire de ce à quoi ressemble le processus de mise sous blister. Il s'agit d'un processus très sophistiqué. Il implique une précision technique, une science des matériaux et une expertise en fabrication. De la conception initiale aux contrôles de qualité finaux, il est important de maintenir la standardisation. Parallèlement aux avancées technologiques, nous pouvons nous attendre à ce que le conditionnement sous blister soit plus efficace à l'avenir. Il jouera également un rôle majeur dans la protection et la présentation des produits.