
Tablet Counting Machine: Introduction, Working Principle, Types, Main Components and Tips to Buy
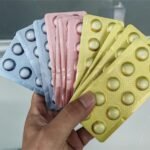
Types of blister packaging in pharmaceutical industry
The Blister Packaging Process: A Complete Step by Step Guide
Blister packaging is one of the most popular packaging processes that you can find in the pharmaceutical industry. However, it is also possible to find the applications of blister packaging in many other industries such as consumer goods and medical devices. This is a comprehensive and versatile packaging technique. It offers protection, visibility, and even tamper-evidence.
Read on and let’s learn more about the blister packaging process from start to finish. We will help you get a clear idea of each, and every step associated with the process.
Understanding the Blister Packaging Method
Before we go into details, it is important to have a basic idea of what the blister packaging method is all about. A blister package usually consists of two main components. They include:
- The blister – Which is a formed plastic cavity
- The packaging material – Usually a foil or card
A blister packaging machine will mold the plastic cavity precisely to match the shape of the product. It will eventually create a protective and secure enclosure. This enclosure will allow consumers to see the item, while keeping it safe from external contamination.
Step by Step Guide to the Blister Packaging Process
Let’s now deep dive and explore the different steps linked with the blister packaging process:
Step 1 – Design and Preparation
The very first step of blister packaging is to analyze the product to package. This involves measuring the exact dimensions of the product. Then it is important to assess the overall sensitivity of the product to different environmental factors. Packaging providers should determine specific protection requirements as well.
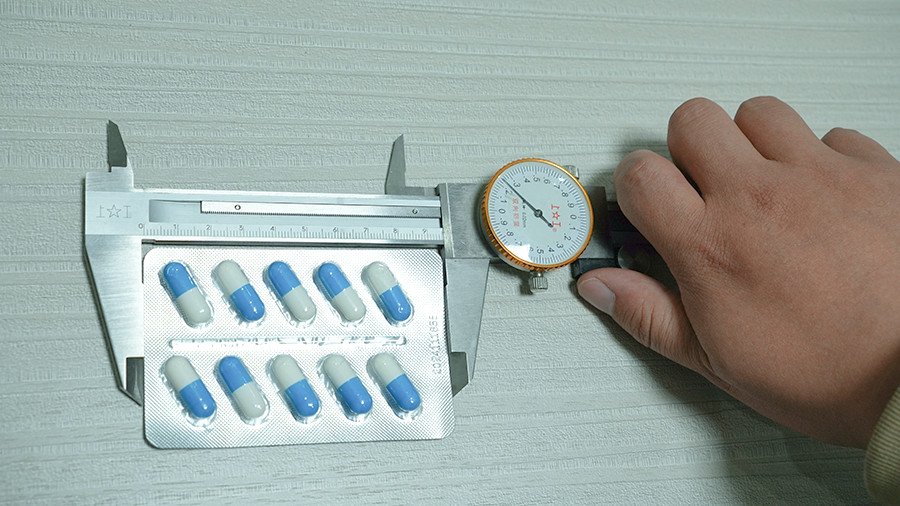
Design-and-Preparation
Upon analysis, they can start the packaging design process. This is where the designers create a blueprint with precise cavity dimensions and material specifications. It will incorporate structural integrity considerations. In most instances, these blueprints will have branding and aesthetic considerations as well.
Step 2 – Material Selection
Selecting the right material is important to the overall blister packaging process as well. The two most important components include:
Blister Cavity Material
Some of the most common materials available for manufacturing the blister cavity include:
- Polyvinyl Chloride (PVC): This is the most common, cost-effective, and versatile blister cavity material available.
- Polypropylene (PP): This material offers higher temperature resistance.
- Cyclic Olefin Copolymer (COC): This material is ideal for sensitive pharmaceutical products.
- Polyethylene Terephthalate Glycol (PETG): This material offers excellent clarity and strength.
Backing Material
Backing material would vary depending on the specific packaging and product requirements. Some of the most common backing materials include:
- Aluminum Foil: This material provides excellent barrier protection
- Paper/Cardboard: It is a cost-effective and printable material available
- Combination Foils: Combination foils can offer multiple layers of protection
- Lidding Films: This material offers flexible sealing options
Step 3 – Forming the Blister Cavity
Formation of the blister cavity is one of the most precise steps in blister packaging. It involves few important steps as well. They include:
Preparation of the Mold
The manufacturer will create a custom mold to match the specifications of the product. These molds usually have a high-quality aluminum or steel construction. Precision engineering will ensure that they maintain overall cavity size and shape throughout.
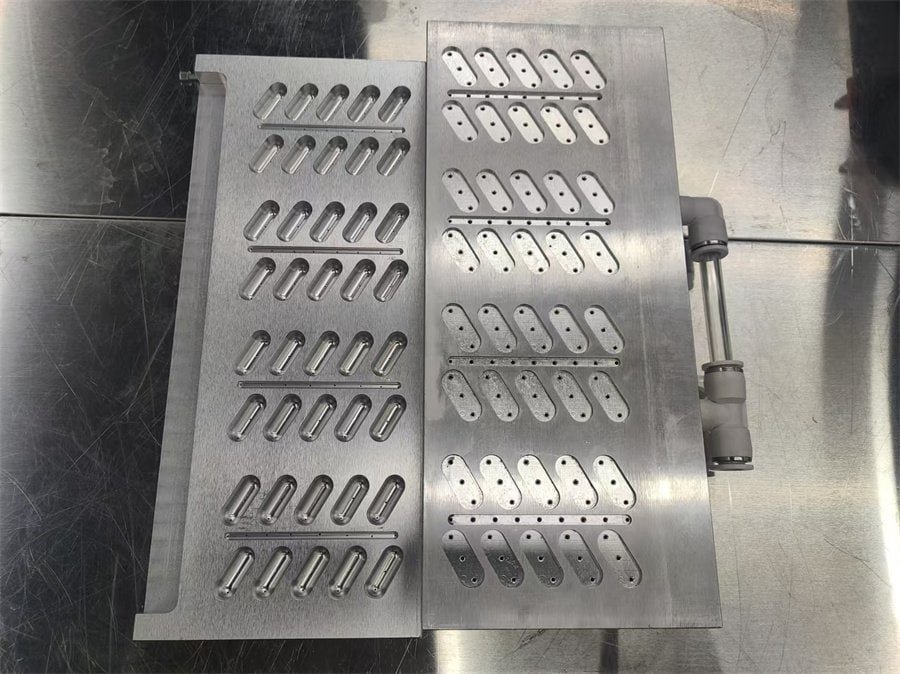
Preparation of the Mold
Thermoforming Process
The thermoforming process will start off with heating the plastic sheet. With rising temperature, the selected plastic sheet will get to its forming temperature. This process involves careful temperature controls. It helps with preventing overall material degradation. However, different materials require some specific temperature ranges.
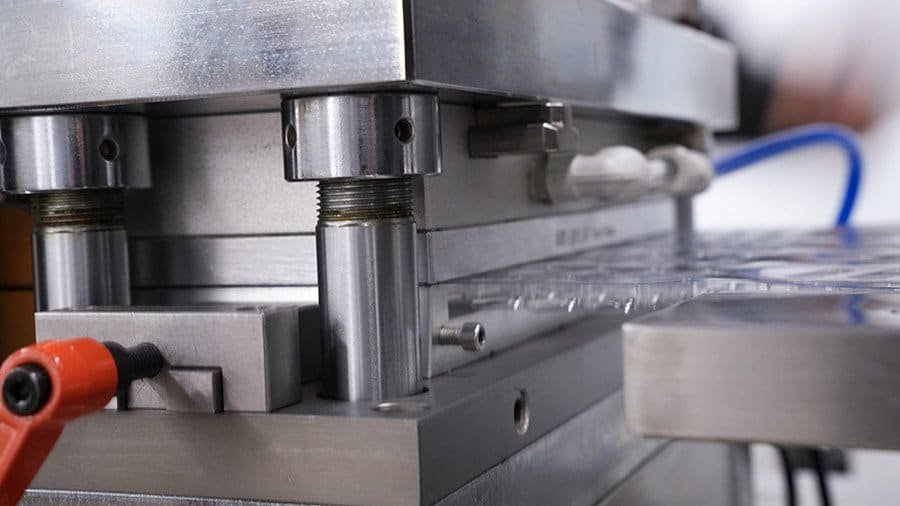
Thermoforming Process
Forming the Cavity
After taking out the heated plastic from the mold, the manufacturer will apply vacuum or pressure into it. This can help them with creating a precise cavity shape. Then they will use cooling systems to rapidly set formed plastic.
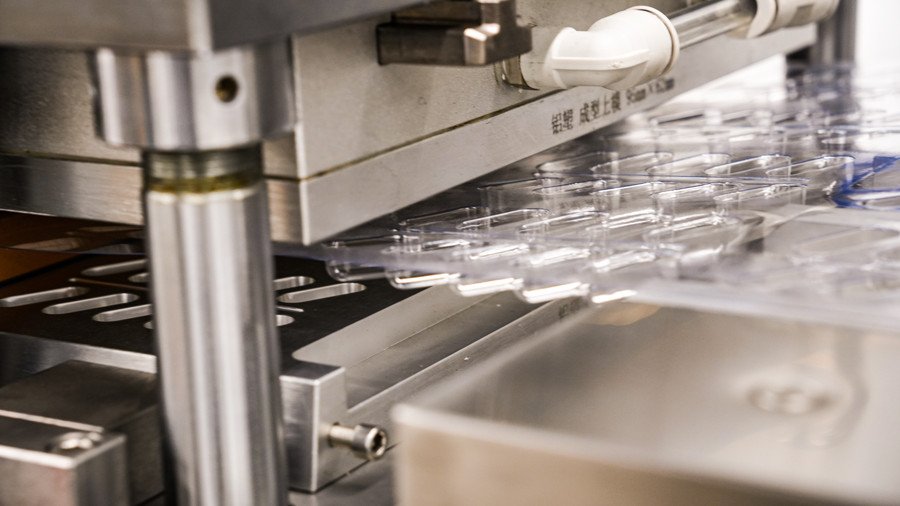
Forming-the-Cavity
Step 4 – Placement of Product
This is also one of the most important steps in blister packaging. Without care and precision, it will not be possible to get the best results out of this process.

Placement-of-Product
Product placement can take place through a manual process or an automated process. Manual placement is ideal for low-volume or specialized products. However, automatic placement is the most common placement method for high-volume products. This is where robotic systems will ensure accurate and consistent positioning of the product placement. There are vision systems that will verify the accurate placement of the product.
Whether its manual placement or automated placement, quality control is important. The blister packaging manufacturers follow different quality control methods. They include weight verification, dimensional accuracy verification, and even visual inspection to identify defects.
Step 5 – Sealing the Package
Upon successful product placement, it is possible to proceed with sealing the package. There are different sealing techniques that blister packaging manufacturers follow for this. Let’s take a look at them in detail.
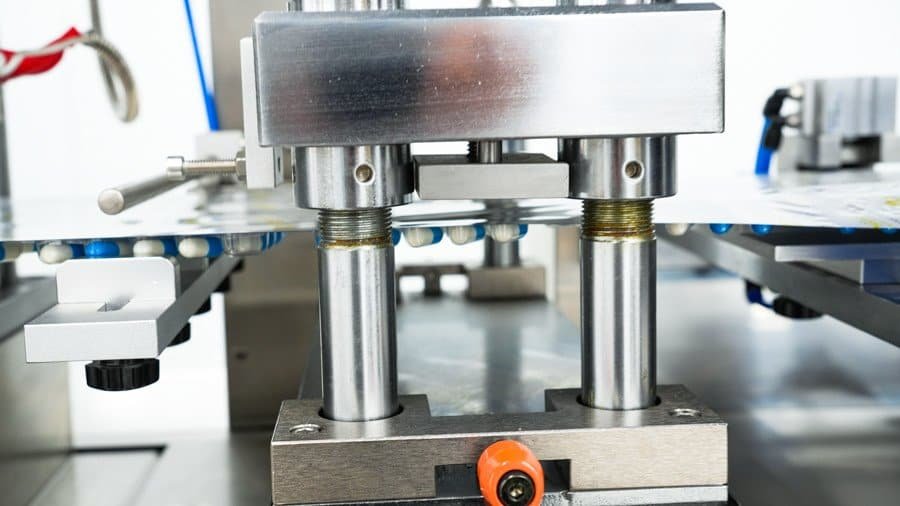
Sealing the Package
- Heat Sealing: This is the most common method available for sealing products. In fact, most products are okay with heat sealing.
- Ultrasonic Sealing: If the products within packaging are sensitive to heat, you can’t proceed with heat sealing. This is where manufacturers take a look at ultrasonic sealing methods.
- Cold Sealing: Another alternative for heat sealing is cold sealing. It uses pressure sensitive adhesives to ensure the overall sealing process.
This process would involve few important sealing parameters as well. They include temperature control, pressure application, and dwell type. On top of them, it is important to seal to ensure integrity testing as well.
Step 6 – Cutting and Separation of Packaging
After successful sealing of blister packaging, manufacturers can take a look at cutting techniques. There are different cutting techniques that manufacturers use as well. Let’s explore them in brief:
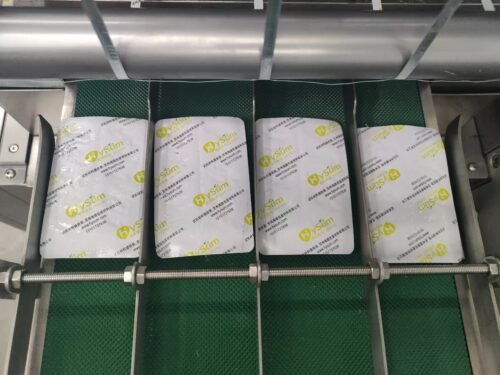
Cutting and Separation of Packaging
- Die cutting – Die cutting machines will separate the individual packages.
- Laser cutting - If there are delicate or complex shapes, die cutting method will not deliver the best results. This is where laser cutting becomes important.
No matter what, the manufacturers will ensure clean edges and consistent package size when cutting the packages. That’s because it has a significant impact on customer satisfaction.
Upon cutting, the manufacturers take a look at trimming and finishing of blister packaging as well. This is where they focus on removing excessive material. It is done with edge smoothing process. Then the manufacturers can ensure final shape refinement.
Step 7 – Quality Assurance and Inspection
Rigorous quality assurance is important throughout the blister packaging process. It will ensure that manufacturers are delivering what exactly the customers are looking forward to receiving. There are multiple inspection processes that they follow to ensure quality. They include:
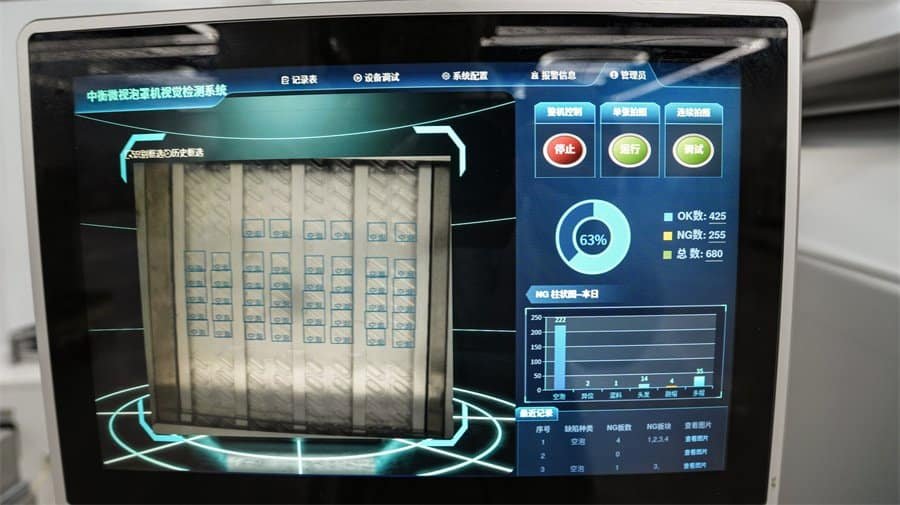
Quality Assurance and Inspection
- Ensuring quality through automated vision systems
- Verification of the weight of packaging
- Seal strength testing
- Checking the overall dimensional accuracy of the packages.
Then the manufacturers will proceed with sampling and validation. This involves statistical process control. It incorporates regular calibration of equipment as well. Moreover, this process would ensure compliance with the industry standards.
Step 8 – Packaging and Storage
After blister packaging, there is a need to look at storage as well. This usually involves secondary packaging. Secondary packaging involves grouping blister packs into larger containers. They can provide convenience with storage and transportation. However, such secondary packaging can serve the purpose of acting as a protective outer packaging as well. Along with that, the manufacturers will focus on labeling and barcoding of blister packages too.
There are few important storage considerations that they need to be mindful about. Temperature and humidity control holds a prominent place. Otherwise, the effort spent on blister packaging the goods will be in vain. Moreover, it is not a good idea to expose blister packaging to direct sunlight. Proper inventory management is important as well.
Exploring the Emerging Trends in Blister Packaging
Now you have an overall idea on how the blister packaging process would look like. In the meantime, it is important to take a look at the emerging trends in blister packaging as well. One of the most significant trends that you can see out there is biodegradable materials. There is a high demand among consumers to go ahead with environmentally friendly packaging solutions. Hence, the blister packaging manufacturers have to provide them with biodegradable packaging solutions. Along with that, they need to be mindful about reducing overall plastic usage as well. This is the main reason why recyclable packaging solutions are gaining a lot of attention.
When it comes to advancements in blister packaging, we can’t simply ignore smart packaging technologies. Some of the newest innovations that you can find behind these packages involve RFID tracking and temperature-resistant indicators. They come with digital information integrations as well. This can benefit the end consumers as well as retailers who sell the goods to the market.
Final Words
By now, you have a clear idea of how the blister packaging process looks like. This is a highly sophisticated process. It involves engineering precision, material science, and manufacturing expertise. From the initial design to final quality checks, it is important to maintain standardization. Along with technological advancements, we can expect blister packaging to be more efficient in the future. It will play a major role behind product protection and presentation as well.