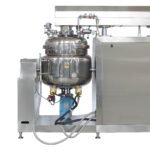
What is the Food Emulsifier Machine: Everything You Need To Know
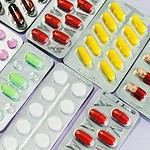
The Ultimate Guide to Blister Packaging
The Ultimate Guide To Gummy Candy Production Line
Overview
Gummy candy has successfully become one of the most favored worldwide treats that are popular among people of all ages due to this Gummy candy’s chewy texture, its bright colors and its fun shapes. Despite appearing simple, there is a complex production process behind each gummy bear, ring, or worm that turns elemental ingredients into the same uniform, mouth-delightful candies you find on the shelves. A gummy candy production line makes this process possible with a series of machines that fits together to form one big machine.
The gummy candy production line is an apparatus combining certain machines for the production of gummy candies with the ability to mix, cook, and shape gummies and, in synchronization with each other, to package gummies. These machines take the burden away from manufacturers when it comes to large scale production in order for them to meet high demand in quality. Other than producing traditional gummies, these production lines are employed in vitamin gummies deployment, CBD gummies production, as well as some other specialized titles that contain certain ingredients.
This guide is going to explore the core components of a gummy candy production line, what machines are involved, what they do, and step by step through the mixing to packaging part of the process. In this post, you’ll learn how to select the best setup and auxiliary equipment for efficient and high-quality gummy production that fits your business needs.
What Is a Gummy Candy Production Line?
A gummy candy manufacturing line is a whole setup meant to simplify every stage of candy production, from mixing to cooling, far more than a single machine. Every element contributes specifically to turn flavors, gelatin, sugar, and other ingredients into precisely formed, premium gummies. Quickly produce gummies that are all consistently the same size, shape and texture.
What Are the Integral Components of a Gummy Candy Production Line?
Many necessary machines on a gummy candy production line cooperate for effective production:
Mixing and Cooking System
The mixing and cooking system is where gummy making starts. To make a smooth, even gummy base, sugar, water, flavors, and ingredients like gelatin or pectin are cooked together. In this case, both the temperature and the amount of mixing must be exact because they have a direct effect on the texture and quality of the sweets that are made. While the cooking tanks break down the gassing agents to make a flat base that is ready to be shaped, the mixers make sure that the ingredients mix evenly.
Depositing System
The base mixture is then put into the machine for depositing, where it is shaped. At this point, the gummies have different forms, sizes, and textures. Feed hoppers keep the mixture warm to keep it fluid, and a number of nozzles fill the molds exactly. The fast and accurate filling process makes thousands of gummies in minutes and makes sure that each one is the same.
Cooling Tunnel
Once the gooey mixture is put into the molds, they are moved through a cooling tube so the gummies harden. The tunnel slowly drops the temperature so that the gummies can set without losing their shape. By keeping the temperature and humidity in the tunnel just right, the sweets don't get hard or sticky, so they keep their quality while they take on their final shape.
Packaging Equipment
Finally, packaging is added to the line of work. The gummies are weighed, put in order, and then put into bags or other packages here. Labeling and sealing mechanisms are often built into packing equipment to keep goods fresh and give retailers information about the products they sell. Every package meets the weight and quality standards thanks to automated scales and quality checks. This gets the sweets ready for sale or shipping.
How Do I Choose the Right Gummy Production Line for My Business?
Your output goals and budget, as well as the size of the business you want to use the gummy production line for, will help you choose the right manufacturer. These important things will help you decide:
- Production Capacity: So compute how many gummies you’d need to make. Tabletop depositors may be a good starting point for smaller operations, while high capacity floor standing or full production lines are used by larger operations.
- Automation Level: Inappropriate for high volume production, lines are fully automated and minimize labor with reduced error. Lesser cost but greater manual work is required by semi automated lines.
- Types of Gummies: Make sure the line is capable of working with the products that need — such as gelatin-based, pectin-based, or multi-color gummies.
- Space and Layout: Think about the space, as there has to be dedicated space for larger lines. Make sure the machine dimensions fit check, and there’s room for maintenance.
- Cost and Budget: Also compare the total costs along with maintenance, utilities, and training. Limit budgets can be worked with by using leasing or used equipment.
- Manufacturer Support and Warranty:Especially for maintenance, troubleshooting etc. choose a manufacturer that has a good reputation, good customer support and good warranties.
The Manufacturing Process of Gummy Candy
The gummy candy manufacturing process consists in several phases to produce a consistent, quality product:
Step 1: Preparing the Gummy Base
Putting gelatin or pectin, sugar, water, and flavorings in a cooking tank and measuring and mixing them together lets you heat them up and remove the gassing agent. Next, the blend might go through a homogenizer to make sure it has a smooth, even texture.
Step 2: Molding and Depositing
As the warm gummy mixture flows into an exactly fitting depositor that fits molds, it shapes each gummy. There are movements in the lines that get rid of air bubbles and make sure that the filling is even.
Step 3: Cooling and Setting
Molds are moved through a cooling tube, which lowers the temperature slowly so that the gummies harden. Changing the humidity stops things from sticking, and demolding takes the sweets out of molds that don't stick.
Step 4: Coating and Flavoring (Optional)
Using a revolving drum guarantees even coating when gummies are covered with sugar, oil, or wax for taste or a glossy finish.
Step 5: Packaging and Quality Control
Packed into bags or bottles, weighted and sorted gummies are labeled with product specifics. Before being sealed for freshness, a last quality check guarantees consistency in color, form, and texture.
What Are the Auxiliary Equipment for the Gummy Candy Production Line?
Although the backbone of a gummy manufacturing line is formed by its main components, auxiliary equipment adds production flexibility, quality enhancement, and streamlining of the process. An outline of necessary auxiliary tools is provided here:
1. Mixing and Cooking System
This includes cooking and mixing kettles and agitators to turn ingredients into the gummy base. The size and complexity of the system depend on the production rate. For small tasks, one mixing tank would be enough. For bigger ones, though, you might need several tanks with complex temperature control.
2. Oil or Wax Coating Machine
When the sweets are cool, they might go through a machine that coats them in oil or wax. This machine puts a small layer of wax or oil on the gummies to make them shiny and keep them from sticking together while they're being packed. Wax coats are used a lot, especially when making gummy bears.
3. Cooling Tunnel
A cooling tube is needed for higher production lines. It ensures that the gummies are set correctly without becoming sticky or misshapen. Several cooling zones in the tube could help lower the temperature gradually while keeping the shape and texture of the gummy bears.
4. Packaging System
A full packing system can be added to advanced production lines. This system can include scales for weights, machines for bagging, and machines for sealing. It takes care of everything, from sorting and weighing to packing and closing. This cuts down on the need for people to do these tasks and speeds up production.
Conclusion
Gummy candy production lines are needed to make candy on a large scale and effectively. They also make the change from raw materials to finished goods smooth. Every machine in the line, from the mixers to the cooling tunnels and packaging systems, ensures quality, output, and consistency. Producers can make premium gummies with exact tastes and textures if they know what role each ingredient plays. Companies can meet customer needs and grow by picking the right tools for the job based on space, price, and production needs..
Gummy Candy Production Line FAQ
What equipment do I need to make gummies?
Along with optional machines for added product features, you will need a mixer, depositor, cooling tunnel, and packaging system.
Where can I buy a gummy candy production line?
One can buy a line from manufacturers of confectionery equipment, or suppliers focused on candy production machinery.
How does the gummy candy production line work?
Every machine helps one stage in the process: ingredients are mixed, cooked, molded, cooled, and then packaged.
What types of candy can be produced with a gummy production line?
By varying molds and ingredients, these lines can create classic gummy forms, vitamin, CBD, and other confectionery products.
How to choose the right gummy production line manufacturer?
To meet your production requirements, pick a reputable manufacturer with a proven track record offering warranties, quality tools, and support.