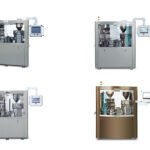
What Is a Capsule Filling Machine? Everything You Need To Know

The Ultimate Guide to Semi Automatic Capsule Filling Machine: Everything You Need to Know
What Is a Blister Pack Machine? Everything You Need To Know
Looking to boost your packaging efficiency? Discover blister pack machines—your comprehensive solution for enhancing productivity.
Blister pack machines have become a highly valuable asset, especially in the consumer products and pharmaceuticals industries, where accuracy and safety of the product are very important.
All that being said, in this blog we will walk you through everything you need to know about blister pack machines. We’ll also explain how they work, the benefits, along with the differences in machines. With the help of this in-depth article, it will help you pick the best one for your packing needs, no matter how big or small your business is.
Blister Packaging Market Size & Trends
According to a report on the blister machine market by Grandview Research, The global blister packaging market size was estimated at USD 28.66 billion in 2023 and is expected to grow at a CAGR of 7.4% from 2024 to 2030.
What Is a Blister Pack Machine?
Now that we’ve done a general overview, let’s dive into the details. To put it simply, a blister pack machine is a specialized machine utilized for the production of blister packaging, which is a widely employed technique for securely packaging various products such as pills, tablets, capsules, and even candies. The machine creates separate compartments, known as cavities or blisters, usually made of plastic. These compartments are subsequently filled with the product and sealed using a backing material like aluminum foil or plastic.
Blister pack machines are specifically engineered to automate this process, guaranteeing accuracy, productivity, and uniformity throughout extensive manufacturing quantities. There are a variety of blister pack machines, ranging from semi-automated to fully automatic versions, which may be tailored to meet individual manufacturing requirements. That said, each machine works differently and in various steps.
How Do Blister Packing Machines Work?
Blister packaging machines operate by performing a series of meticulously planned steps to produce blister containers that are both dependable and of the highest quality. Here’s a breakdown of how they work:
Step #1: Creating the Blisters
The process starts with the formation of the blister cavities. The machine receives a plastic sheet and applies heat to shape it into the desired blister form, utilizing either a vacuum or pressure forming method. This process generates the hollow spaces that will contain the individual products.
Blister mouth is being made
Step #2: Applying the Filler
After the blisters have formed, the machine transfers the sheet to the filling station. In this process, the individual items, such as pills, tablets, or capsules, are accurately inserted into each blister cavity. Automating this procedure helps guarantee precise positioning and accommodates fast-paced production.
Filling pills
Step #3: Applying the Sealant
Once the cavities have been filled, the machine proceeds to apply a backing material, often aluminum foil or plastic, to the surface of the filled blisters. Both heat and pressure are used to successfully bond the backing to the blister sheet. The tightly sealed blister packs are then separated into individual units, ready for the packaging and distribution process.
Encapsulating Aluminum Film
How Many Types of Blister Packaging Machines are There?
There are various types of blister packing machines, each designed to accommodate distinct materials and production requirements. Some of the most common machines include:
- Manual Blister Packing Machine: These machines are great for custom batches or small-scale production, but they need human labor to shape, fill, and seal the blisters. Although flexible, they work well for lower volume requirements.
- Tablet Blister Packing Machine:These devices, which are designed specifically for tablet packaging, provide precise positioning and tight sealing, making them essential to the manufacturing of pharmaceuticals.
- Alu Blister Packing Machine:The Automatic Alu Blister Packing Machine is specifically designed for use in the pharmaceutical and confectionery industries. The machine effectively encloses items such as tablets, pills, candy, and capsules, guaranteeing accurate and dependable packing in blister form for a wide range of uses.
- PVC Blister Packing Machine:These machines are commonly used for packing products that require clear visibility, including food, yogurt, cosmetics, contact lenses, medicines, sauces, and health products. That said, these machines make blisters using PVC plastic.
- Fully Automatic Blister Packaging Machines: Fully automated, these machines manage every step of the process, from forming to sealing and cutting, which makes them perfect for high-volume production with excellent efficiency and reliability.
What Is the Application of Blister Packing Machines?
Blister packing machines are multifunctional devices utilized in many industries to securely package products within separate blister chambers. Within the pharmaceutical sector, packaging plays a vital role in safeguarding pills, tablets, and capsules by assuring precise dosages and shielding them from external elements like moisture and light. These machines are also extensively utilized in the nutraceutical and supplement industries, where there is a demand for precise packaging requirements.
In addition to the pharmaceutical industry, blister packing machines are utilized in the consumer goods sector, namely for the packaging of small objects such as candy, hardware, and electrical components. The machines offer a tamper-evident seal, making them well-suited for retail products that require both visibility and protection.
Moreover, blister packing machines can also be used in laboratories for the purpose of sample containment, as well as in the food industry for the packaging of individual servings.
Blister packaging machines are essential for businesses seeking fast, dependable, and functional packaging solutions since they can be customized to fit specific materials and blister sizes.
What Are the Benefits of Blister Packing Machines?
Blister packaging machines provide multiple benefits that make them a significant resource in diverse businesses. To start, blister packs offer significant advantages in terms of safeguarding products. They create a reliable barrier that protects against moisture, light, and contamination, ensuring the quality and longevity of delicate items such as pharmaceuticals and vitamins.
These machines also provide exactness and uniformity in packing, which is essential for upholding precise dosages and quality control in large-scale production. One important advantage is the tamper-evidence provided by sealed blister packs, which quickly reveal any tampering with the product, thereby improving consumer safety.
And finally, blister packaging machines provide flexibility as they are capable of processing numerous materials, including PVC, aluminum, and other types of polymers. Moreover, these machines may be tailored to accommodate diverse product shapes and sizes.
Their ability to adapt, together with their proficiency in automating the packaging process, enables organizations to save labor expenses and enhance production velocity while upholding stringent quality standards.
What Are the Main Parts of a Blister Packing Machine?
Now that we’ve gone over the basics, let’s quickly go over the main parts of a standard machine. A blister packaging machine has multiple essential components that work to produce secure and top-notch blister packets. The following are the primary components:
- Forming Station:This is the specific area where the blister cavities are created. Thermoforming involves applying heat to a plastic or aluminum sheet in order to mold it into the necessary blister shapes. On the other hand, cold forming involves pressing the sheet to get the desired outcome.
- Filling Station: The filling station precisely deposits the item, such as tablets, capsules, or other products, into each cavity once the blisters have formed.
- Sealing Station:The sealing station is the part where the blister cavities are enclosed with a backing material, often made of aluminum foil or plastic. The blisters are sealed by applying heat and pressure, which safeguards the contents.
- Cutting Station:After being sealed, the blister packs are divided into separate units. This station may also include the process of perforation, which is used to form smaller pieces within a larger sheet that may be easily separated.
- Control Panel: The control panel enables operators to configure and fine-tune parameters such as temperature, velocity, and sealing pressure. It offers live monitoring and guarantees optimal and constant machine performance.
All that said, every individual component in the blister packaging process has a vital function, working together to provide top-notch, reliable packaging for a diverse array of products.
What Is the Difference Between Manual and Automatic Blister Packing Machines?
To put it simply, manual blister packaging machines require comprehensive manual labor, with operators manually loading, filling, and sealing the blister packs. These machines are suited for small-scale production or custom batches, providing flexibility at a slower pace.
Automatic blister packaging machines, on the other hand, handle the entire process—from shaping and filling to sealing and cutting—without requiring any manual work. They are intended for high-volume production, ensuring consistency in quality, efficiency, and speed. Automatic machines are ideal for large-scale productions, as they reduce labor costs and boost total output.
All that being said, we hope that this extensive article has provided you with everything you need to know about blister pack machines. If you’d like to learn more about how these machines can help your business, give our experts at Grand a call or fill out a contact form to get started!