
Top 4 Best-Selling NJP Series Capsule Filling Machines

Tablet Counting Machine: Introduction, Working Principle, Types, Main Components and Tips to Buy
Development History of Blister Packaging Machine
Development History of Blister Packaging Machine
Blister packaging machines play a major role in the packaging industry. In other words, manufacturers tend to use them for packing pharmaceutical, medical, and consumer products. These machines, are capable of protecting, preserving, and presenting certain products to consumers. That’s why they are so popular in the pharmaceutical and food processing industries.
If you are about to start a manufacturing facility to package pharmaceuticals or food, you will need to buy a Blister Packaging Machine. It will be a massive investment. That’s why you need to have a complete understanding of what they are, before you invest. It will even help you to make an informed decision at the time of investing.
What is a Blister Packaging Machine?
The role of a Blister Packaging Machine is to package consumer goods inside plastic blisters. These are small, pre-formed plastic bubbles, which seal to a cardboard backing. A Blister Packaging Machin will feed a roll of plastic film and form it into blister shapes using pressure and heat. It will also feed in the cardboard backing material separately. The sealing process will then seal the plastic to cardboard. This will create easy to open individual bubbles for each product item.
The most common applications of a Blister Packaging Machine include packaging:

Medicine
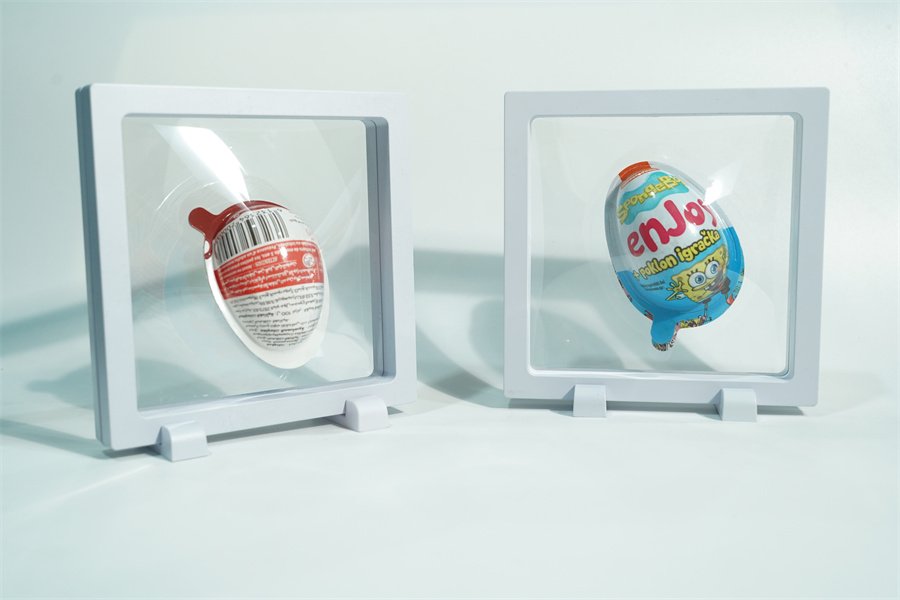
Food

Toys

Hardware
What Makes Blister Packaging Machine So Popular?
The sealed blister packs are capable of protecting products inside plastic bubbles. They also offer tamper evidence. Moreover, consumers can easily view the items.

sealed blister packs
Blister packaging is quite popular for retail items. That’s because this type of packaging can help to display items prominently. Moreover, they can also share other information such as branding, ingredients, expiration dates, and doses.
To create blister packing, you can use modern Blister Packaging Machines. But let’s take a quick look at the history of these machines and learn more about them.
History of Blister Packaging Machines
Blister Packaging Methods in the Pre-industrial Era
Before the industrial revolution, blister packaging was not a necessity at all. However, people who lived back in the day used materials such as clay containers, woven baskets, and animal skins for packaging. After some time, they switched to glass and ceramic vessels for storing and transporting goods. They just wanted to protect their contents from environmental degradation, physical damage, and contamination.
Industrial revolution was a significant turning point for Blister Packaging Machine industry. It introduced mass production techniques. As a result, manufacturers had to look for packaging methods that are simpler and more efficient. Moreover, they wanted to ensure convenience with marketing, preservation, and distribution.
Transition into Modern Packaging
Packaging industry could see significant improvements during the last 19th and early 20th centuries. A perfect example of this is the development of new materials such as cellophane during 1912. Along with this, people reduced the use of paper for packaging. That’s where plastic packaging became more mainstream.

Jacques Brandenberger invented cellophane, which led to a growing demand for blister packaging. Image source: Cellophane was Invented by NIHF Inductee Jacques Brandenberger
The Concept of Blister Packaging Machines
Manufacturers wanted to create more secure, visible, and tamper-evident packaging solutions. It was a necessity in the pharmaceutical and medical industries. That’s because the manufacturers wanted to ensure product integrity. Moreover, they wanted to clearly represent the dosage presentations on packaging as well.
On top of everything, the pharmaceutical manufacturers wanted to improve medication preservation. Along with that, they wanted the packaging to be sterile as well. Otherwise, they won’t be able to address the consumer safety considerations.
This need led the manufacturers to create the experimental designs of first blister packaging solutions. According to historical records, the very first blister packaging solutions came out during the 1940s and 1950s. These were some rudimentary packaging solutions. That’s because people had to manually form plastic or aluminum sheets around product molds. The overall process was labor-intensive. It lacked the precision of modern machines as well.
Evolution of Blister Packaging Machines with Technology
Along with technological developments, people were able to make better blister packaging machines. Let’s take a look at how they could evolve along with time.
The First Generation of Blister Packaging Machine
The first generation of Blister Packaging Machines came out during the 1950s and 1960s. These machines came out with a significant technological leap as well. For example, they could offer semi-automatic operation to the users. This helped them with overcoming the manual and time-intensive work that they were doing.
However, the first generation of Blister Packaging Machines still had manual product loading. The packaging speeds were not very impressive. But they could still process around 10 to 30 packages per minute. It was much better than manual work. The sealing mechanism of these machines were basic. As a result, sometimes they didn’t offer the expected results. However, mechanical control systems were able to help people improve overall efficiency by making blister packaging.
Material Science Breakthroughs
Along with technology, the development of machines could gain a lot of advancement. In the meantime, material science could play an important role as well. It happened along with the introduction of new polymers and barrier films. They could dramatically expand the packaging possibilities.
Here are some of the most prominent material innovations that came out along with technology:
- Polyvinyl Chloride (PVC) was able to become the standard material for blister packaging. It is still the most popular material.
- Introduction of aluminum foil was able to play the role of barriers.
- Instead of just normal polyethylene, manufacturers were able to use high-density polyethylene.
- Introduction of advanced multi-layer barrier films was also a significant improvement in technology.
These improvements were able to enhance overall product protection. As a result, they could enhance customer satisfaction as well. Moreover, the advanced materials could offer better moisture resistance. It also enhanced chemical stability, while increasing transparency. This could align more with the needs of the pharmaceutical and food product manufacturers out there.
Industrial Applications and Expansion of Blister Packaging Machine
Pharmaceutical industry was the primary customer base of Blister Packaging Machines. As a result, some of the leading pharmaceutical companies actively invested in blister packaging innovation as well. It could help them with meeting the stringent regulatory requirements effectively. Moreover, they were able to cater to the need for precise medical packaging.
Here are some of the key requirements that pharmaceutical manufacturing companies had back in the day. They wanted to find solutions to all these requirements through advanced Blister Packaging Machine development.
- Representation of exact dosage in the product packaging.
- Introducing tamper-evident seals to packaging.
- Introducing child-resistant designs for packages.
- Enhancing overall shelf-life preservation of the products.
- Maintenance of sterility of medicine.
- Precise labeling and tracking of goods.
Even though pharmaceutical companies were driving innovation, many other industries could experience the benefits of innovation. Some of them include:
- Consumer electronics
- Personal care items
- Food packaging
- Medical devices
- Hardware and small component packaging
Integration of Technological Advancement and Automation
During the 1980s and 1990s, we could see heavy automation coming into play. It was able to create a significant impact on Blister Packaging Machine innovation.
Computer and Electronic Revolution
Starting 1980s, people started integrating computer technologies into Blister Packaging Machines. As a result, they were able to make the machines more intelligent. This is the time period where the Blister Packaging Machines started getting Programmable Logic Controllers (PLCs). They came out with digital control interfaces as well. On top of everything, these machines got precision sensor technologies.
Real-time quality monitoring systems could ensure the quality of Blister Packaging Machines produced during this time period. They also came with advanced temperature and pressure regulation. Along with that, some of the sophisticated machines came with complex statistical process control methodologies.
Here are some of the main features that we could see in Blister Packaging Machines introduced during this time period:
- High operating speeds up to 600 packages per minute.
- Handle multiple product formats simultaneously
- Integrate with enterprise resource planning (ERP) systems
- Perform real-time quality inspections
- Minimize material waste
- Adapt quickly to different packaging requirements
Sustainability and Environmental Concerns
After 2000s, all Blister Packaging Machine manufacturers started worrying about sustainability. As a result, the Blister Packaging Machines got green packaging capabilities. For example, these machines could work with biodegradable packaging materials. They reduced the overall plastic consumption. Moreover, these machines were able to operate energy efficiently as swell.
Integration of circular economy took place during this time period as well. Along with that, the manufacturers wanted to use recyclable packaging solutions.
Blister Packaging Machines Today
We live in a world where smart technologies are taking over many things. We can see that in Blister Packaging as well. For example, the Blister Packaging Machines today come with active packaging and embedded sensors. They can also offer temperature-indicating packaging solutions.
QR code and RFID integration is playing a significant role in the functionality of modern Blister Packaging Machines. They also have intelligent track and trace systems.
Along with time, the Blister Packaging Machines evolved to be more efficient. That’s why you can see them offering standardized packaging processes as of now. They are able to reduce production cost, while enhancing overall safety as well.