
Tablet Press Machine; Types, Working Principle, Production Steps All You Need To Know
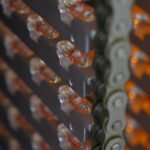
Liquid Capsule Filling Machine: Introduce,Working Steps,DIY and Application
Overview of China’s Tablet Press Market
Development History of Tablet Press Machines in China:
Tablet press machines were introduced earlier in Europe and the United States, with nearly a century of history. In China, the first development came in 1949 when Tianxiang Huaji Iron Factory in Shanghai replicated a British 33-punch tablet press. By 1951, based on an American 16-punch press, China created its own 18-punch machine. This marked one of the earliest pharmaceutical machines manufactured domestically.
By 1957, China designed and built the ZP25-4 tablet press. In 1960, the country successfully developed the 60-30 model, featuring automatic rotation and compression. The machine was capable of producing various types of tablets, including medicinal, sugar, calcium, and coffee tablets. During the same year, the ZP33 and ZP19 models were introduced.
Mass production of the ZP series tablet presses began in the 1970s, with leadership from Shanghai First Pharmaceutical Machinery Factory and Nantong Sanktaya Machinery Co., Ltd. Significant progress was made during China's "Seventh Five-Year Plan" when the Aerospace Department’s 206 Institute developed the HZP26 high-speed tablet press. This was a major milestone in Chinese pharmaceutical machinery.
In 1980, the Shanghai First Pharmaceutical Machinery Factory created the ZP-21W tablet press, a machine that met the international standards of the early 1980s. Considered an innovative product, it helped further China's technological advances. By 1987, China had introduced microcomputer control technology from Germany's Fette company, leading to the development of the P3100-37 rotary tablet press. This press featured automatic control for tablet weight and pressure, automatic counting, and waste tablet rejection, with a sealed design that met GMP cleanliness standards.
The late 1990s saw more innovation when Shanghai Tianxiang Jiantai Pharmaceutical Machinery Co., Ltd. developed the ZP100 series rotary tablet press and the GZPK100 series high-speed rotary press. These machines marked important advancements in China’s pharmaceutical manufacturing capabilities.
With the 21st century came further developments. GMP certification became more prevalent, leading to the introduction of fully GMP-compliant ZP series rotary tablet presses. Notable models included the ZP35A from Shanghai and the ZP35D from Nantong Sanktaya Machinery. High-speed rotary tablet presses made progress in areas like production output, pressure signal collection, and waste rejection. These machines achieved outputs of over 300,000 tablets per hour, with pre-pressure reaching 20kN and main pressure exceeding 80kN or even 100kN.
High-speed models such as the GZPLS-620 and GZPK3000 series from Nantong Sanktaya and the PG50 series from the Beijing Aviation Manufacturing Engineering Institute showcased these advancements. These machines brought greater efficiency and precision to tablet production.
Advances in manufacturing technology and increased demand for specialized equipment led to the development of tablet presses for specific uses. These included the ZP5 rotary tablet press for laboratory applications, dry powder rotary presses for compressing powders, and explosion-proof ZPYG51 series rotary presses for making explosive tablets. These developments highlight China’s ongoing innovation and expansion of tablet press applications across various industries.
Current Status of the Tablet Press Market in China and Internationally:
Large variety and quantity:
Tablet presses have been a key part of China’s pharmaceutical industry for a long time, making them one of the oldest machines used in the field. Over time, they became some of the first pharmaceutical machines China exported, thanks to their large production capacity. This has helped China become a major player in the global market.
Today, China has about 40 manufacturers producing around 2,000 tablet presses each year. With roughly 60 different models available, these machines can create all kinds of tablets. From simple round tablets to more complex ones like double-layered or engraved designs, the variety is impressive and meets a wide range of needs.
China now leads the world when it comes to the number of manufacturers and the variety of tablet presses produced. These machines can handle specialized designs like ring-shaped or core-coated tablets. This versatility has made China a global leader in tablet press manufacturing.
Ease of operation:
Chinese manufacturers have been putting more emphasis on product quality, focusing on a "quality-first" approach. This shift has come as the demand for better standards in tablet production continues to grow both within China and internationally. Because of this, there’s been a strong push to create more reliable and efficient tablet presses.
Many pharmaceutical companies in China produce a wide range of tablets, often in smaller batches. To keep up, manufacturers have designed machines that are easier to use and clean. These user-friendly features make it faster to switch between production runs, especially when making different kinds of tablets.
These improvements in design and efficiency have had a real impact on the manufacturing process. The ability to quickly change between tablet types saves time and cuts costs. It’s made the production process smoother and more flexible, helping Chinese tablet presses compete better in global markets.
Low technological content and lack of innovation:
Even though there are over 40 companies in China making more than 60 types of tablet presses, many of these machines still aren’t very advanced. The designs have stayed pretty basic, with little improvement over time. Because of this, the industry hasn’t made the kind of progress needed to keep up with global competitors.
The lack of technological advancement has created real challenges. While manufacturers can produce a variety of tablet presses, most still rely on older methods. This makes it tough for them to offer the modern features that are now expected from tablet presses around the world.
If the industry doesn’t innovate, it risks falling further behind. There’s a clear need for more research and development to move the technology forward. Without that push, the industry will continue to struggle with producing machines that meet today’s standards for efficiency and precision.
Summary of the Status in China:
Even though new tablet press models are introduced each year, very few feature advanced technology or high added value. The industry suffers from repetitive development, with many manufacturers producing the same types of machines. To survive, smaller companies often imitate others' technology rather than creating their own innovations. Some companies have even resorted to producing low-quality products. Price wars are common, and because brand loyalty is weak, companies suffer when prices are cut, leading to brand devaluation. If this situation continues, it could lower the overall standards of tablet press design and manufacturing in China.
Most of China's tablet press manufacturers are privately owned but lack advantages in technology, equipment, and skilled personnel. This significantly restricts their ability to innovate. Many companies do not have proper research and development teams or innovation systems in place, and there is a lack of emphasis on technological advancement. As a result, their technical capabilities are limited, and the process of upgrading equipment and production technologies is slow. The shortage of skilled professionals in the industry is a critical issue, and this "talent crisis" is becoming a widespread problem throughout the sector.
Status of the International Tablet Press Market:
The gap between China's tablet press technology and that of developed countries keeps getting bigger. While Chinese manufacturers have made some progress, companies in places like Europe and the U.S. are pulling ahead with faster, more efficient machines. This growing divide is making it harder for China to keep up with global standards.
In Europe and the U.S., tablet press technology is advancing in important areas like high-speed production, airtight designs, and automation. These machines aren’t just faster—they’re also more precise and efficient, built for large-scale production. Meanwhile, Chinese manufacturers are finding it tough to match these innovations.
The top companies leading the way are mostly in Europe and the U.S., with names like FETTE and KORSCH from Germany, MANESTY from the U.K., COURTOY from Belgium, and STOKES from the U.S. Their machines are highly automated and meet strict industry regulations, including FDA standards and 21 CFR Part 11 requirements for electronic records and signatures. These features are becoming standard in the industry.
For China, closing this gap will be challenging without more investment in research and development. As global competition ramps up, Chinese manufacturers will need to innovate if they want to keep up with the advanced technology of their international rivals.
1. High Speed and High Output
Tablet press manufacturers have focused on achieving higher speeds and greater output for years. Today, some of the top machines around the world can produce up to 1 million tablets an hour or even more. This has completely changed the game, making production faster and more efficient than ever before.
Take Manesty’s Xpress700, for example—it can produce 1 million tablets per hour. Korsch’s XL800 goes slightly higher, with 1.02 million tablets an hour. Courtoy’s ModulD pushes that even further to 1.07 million, but Fette’s 4090i takes the lead, cranking out an incredible 1.5 million tablets per hour. These machines are miles ahead of what Chinese presses are currently capable of.
The difference in speed and output between international machines and those from China is huge. To close that gap, Chinese manufacturers will need to make serious improvements in their design, automation, and production methods. Without those advancements, it’s going to be tough for Chinese tablet presses to keep up with their global competitors.
2. Sealed Process and Isolation of People and Materials
International tablet presses are really good at keeping the entire process sealed, which is crucial for preventing cross-contamination. The granules used to make tablets are delivered through sealed containers and closed conveyor systems, making sure nothing from the outside gets in. This kind of control is essential for maintaining the quality and safety of the tablets.
These machines have systems in place to control dust and prevent particles from separating, keeping the tablets consistent. Once the tablets are formed, they move through a sealed system for screening, inspection, and metal detection before they’re packaged. This ensures the tablets stay clean and protected the whole way through.
Many Chinese tablet presses still use open or semi-sealed systems, which allows dust to escape during compression. This can lower the quality of the tablets and increase the risk of contamination. With GMP standards becoming more common, fully sealing the production process and isolating materials from people is becoming a must for tablet press design in China.
Chinese manufacturers will need to improve their systems. Moving toward fully sealed processes will not only boost the quality of the products but also help them meet the stricter regulations found in international markets.
3. WIP (Wash In Place)
WIP (Wash In Place) technology has had a big impact on tablet presses, helping users save on operational costs. Manufacturers have streamlined the cleaning process by making it easier to clean machines without taking them apart. This feature has become something a lot of companies now look for in a tablet press.
Being able to disassemble parts for cleaning quickly means machines get cleaned thoroughly and faster between production runs. This cuts down on downtime since operators spend less time on maintenance, allowing the machines to get back to work sooner. As a result, productivity goes up, and companies can keep pace with their production demands.
WIP technology also helps companies meet high hygiene standards, which is crucial in industries like pharmaceuticals. By simplifying the cleaning process, businesses can ensure their machines stay efficient and meet regulatory requirements. This mix of cost savings and improved productivity has made WIP technology a must-have feature in modern tablet presses.
4. CFR Part 11 (Electronic Records and Electronic Signatures)
In August 1997, the FDA introduced 21 CFR Part 11, which set rules for using electronic records and signatures in manufacturing. This regulation made it much easier for industries like pharmaceuticals and food production to bring electronic systems into their operations. Electronic records can include anything from text and graphics to data stored on computers, all of which help track and manage production securely.
Image Source: https://www.ecfr.gov/current/title-21/chapter-I/subchapter-A/part-11
Electronic signatures under this regulation are considered just as valid as handwritten ones, allowing them to be used to identify individuals in manufacturing processes. In tablet presses, 21 CFR Part 11 enables features like equipment diagnostics, incident logs, and alarms. These systems keep detailed records of who operated the machines, when, and under what conditions, ensuring everything is well-documented and secure.
While international manufacturers have fully adopted this technology, it's still fairly new in China. Chinese companies are starting to see the benefits of electronic records and signatures but haven't fully integrated them yet. As the global market continues to push for higher standards, it’s likely that Chinese manufacturers will start adopting 21 CFR Part 11 more widely to meet these expectations and enhance data security.
Control Technology for Connecting to a Full Production Line
Tablet presses in countries like Germany and the UK are built to easily connect with a full production line. These machines have start, stop, and speed controls that seamlessly sync with other equipment, like sieving, dust collection, detection, and packaging systems. This kind of integration keeps tablet production flowing smoothly across the entire line, making the process more efficient.
A major advantage of this setup is the constant monitoring of external equipment to ensure safety and reliability. For instance, dust removal systems are continuously checked, and if suction pressure drops, the tablet press sends an alert and automatically stops. This smart monitoring prevents issues from escalating and helps maintain a smooth production flow.
While this advanced control technology has been used in places like Germany and the UK for some time, it’s just starting to be adopted in China. Chinese manufacturers recognize the benefits of these systems in improving reliability and streamlining production. As more companies in China invest in this technology, tablet manufacturing will become safer and more efficient.
The growing use of this technology in China is expected to significantly enhance production efficiency. By connecting tablet presses with the rest of the production line, manufacturers can cut down on downtime and keep operations running smoothly with fewer manual interventions. This not only saves time but also reduces the risk of human error.
In the long run, adopting these advanced systems will help Chinese manufacturers stay competitive globally. With better safety, reliability, and efficiency, they'll be able to meet international standards and produce higher-quality products. The move toward full production line integration marks a promising shift for the future of tablet manufacturing in China.
Remote Monitoring and Diagnostic Systems
As network and broadband technology have advanced, remote monitoring and diagnostics have become a common feature in tablet press machines. Many pharmaceutical companies now rely on computer-controlled presses, making remote monitoring incredibly valuable for keeping everything running smoothly. It allows manufacturers to track machine performance from anywhere, which helps improve efficiency and reduce the need for constant on-site oversight.
Top international manufacturers have already embraced this technology, letting their support teams diagnose and fix problems in real-time. If something goes wrong, the issue can be troubleshooted and resolved remotely, cutting down on downtime. Instead of waiting for someone to show up and fix the problem, companies can get back to production much faster.
This remote capability has also improved after-sales service. Companies don’t need to send technicians for every small issue anymore, which saves time and reduces repair costs. The result is smoother, more efficient production and less disruption.
For remote monitoring to work well, though, companies need the right infrastructure. This means having a solid network, the right hardware, and software to analyze data in real-time. Plus, you need trained staff who can monitor and understand the data to identify and fix any issues that come up quickly.